 |
 |
 |
 |
 |
 |
 |
 |
 |
 |
 |
 |
 |
 |
 |
 |
 |
 |
 |
 |
 |
 |
 |
 |
 |
 |
 |
 |
 |
 |
 |
 |
 |
 |
 |
 |
 |
 |
 |
 |
 |
 |
 |
 |
 |
 |
 |
 |
 |
 |
 |
 |
 |
 |
 |
 |
 |
 |
 |
 |
 |
|
Lancia-Beta-Bastler
|
|
|
Ventile einschleifen!
|
|
|
|
Dies ist ein sehr wichtiges Thema! Sind die Ventile nicht mehr dicht, dann verliert der Motor an Kompression und natürlich auch an Leistung. Also sind dichte Ventile ein muss bei jeder Überholung. Dies muss sehr sorgfältig gemacht werden und ist auch mit wenig Spezialwerkzeug für jedermann machbar. Also schaut einfach zu, wie ich meine Ventile einschleife und auf Dichtheit überprüfe!
|
|
|
|
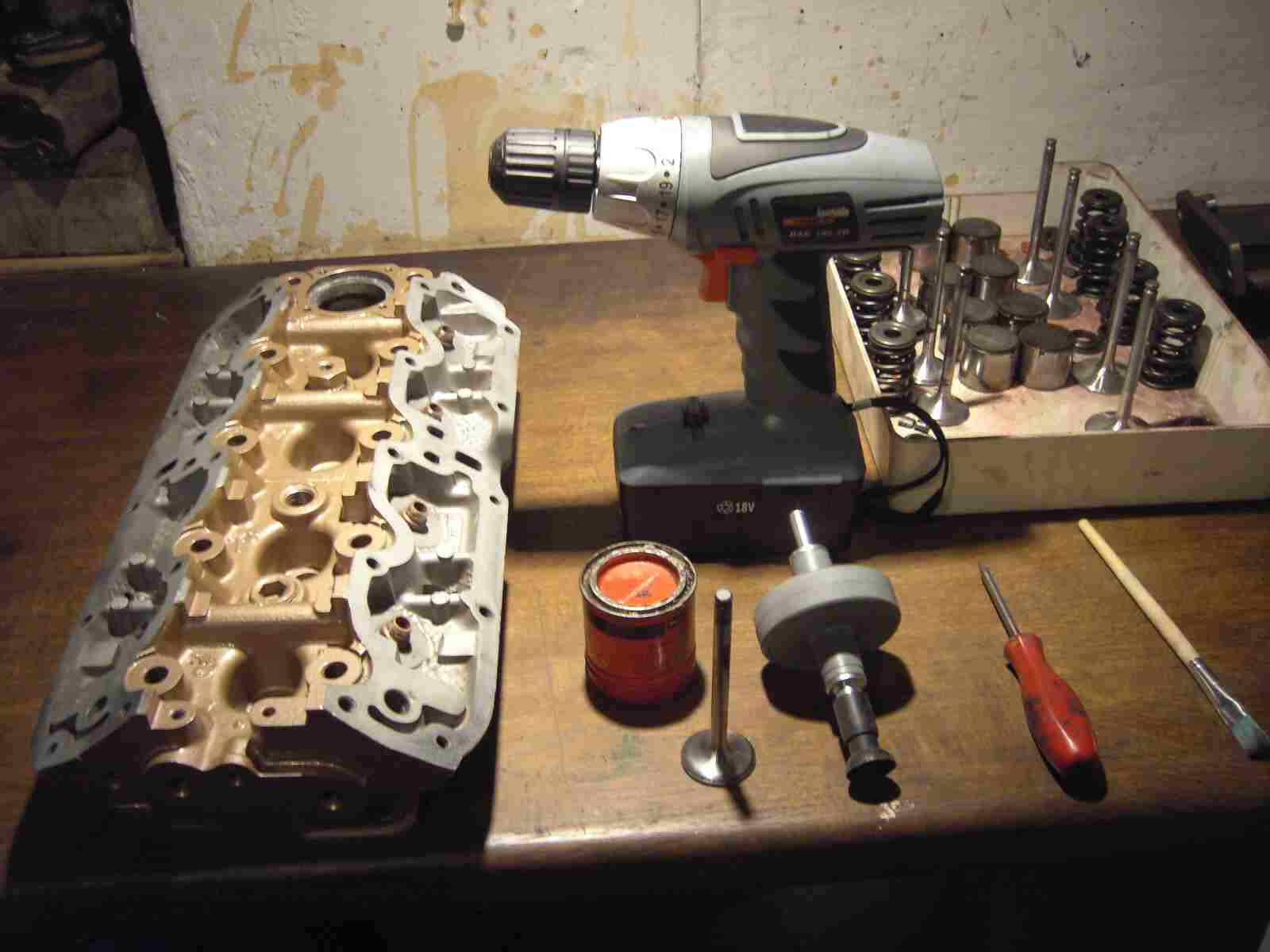 |
|
|
|
Was wird benötigt! Eine Dose Ventilschleifpaste, ein Ventileinschleifgerät und eine Akkubohrmaschine.
|
|
|
|
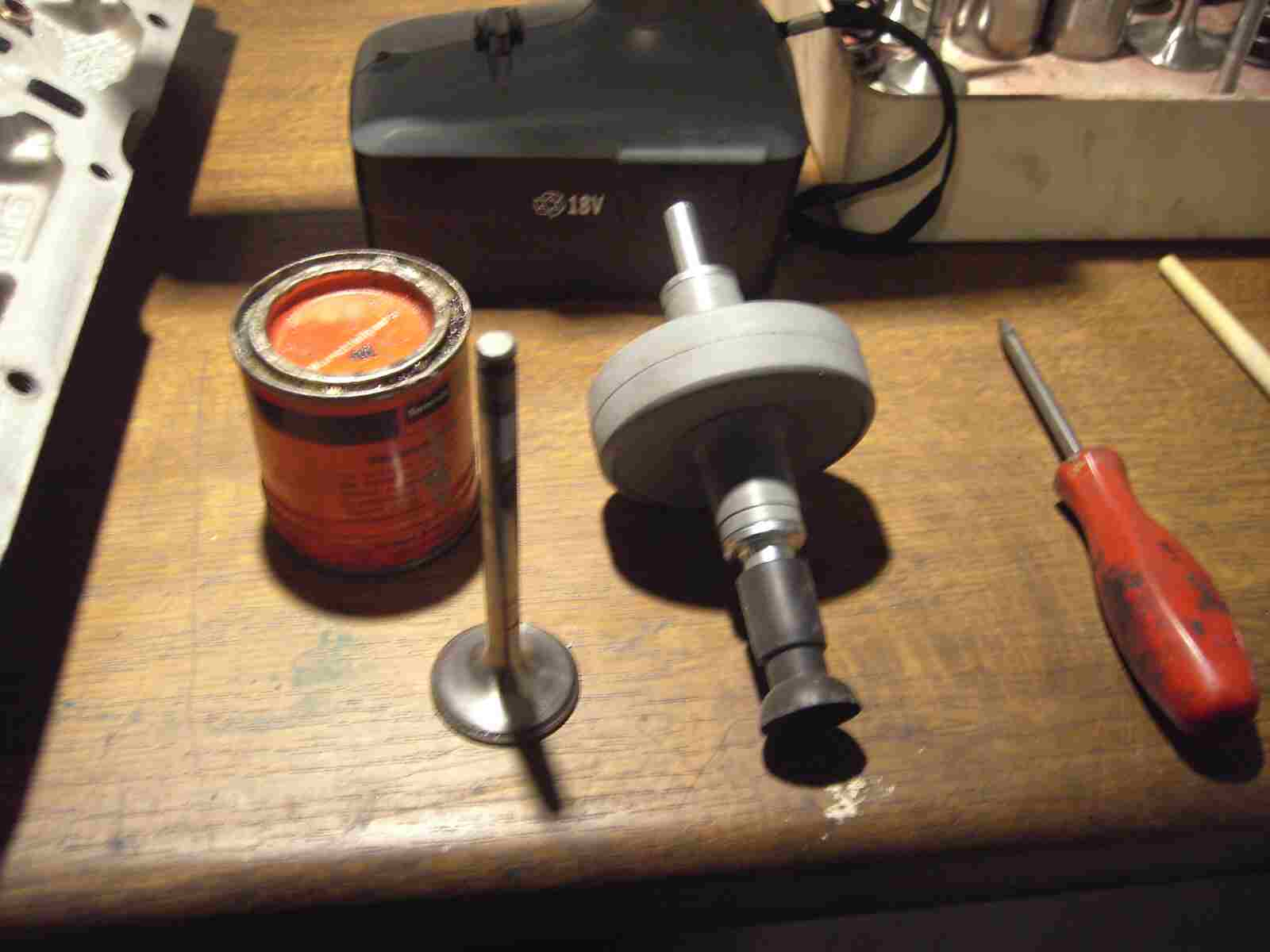 |
|
|
|
Die Ventilschleifpaste kostet etwa 10€ und besitzt zwei Kammern. In der einen befindet sich die grobe Vorschleifpaste und in der anderen die Nachschleifpaste. Das Ventileinschleifgerät kostet im Internet etwa 20€ -30€ und erspart Euch viel Handarbeit. Eine Akkubohrmaschine dürfte jeder in seiner Werkstatt haben.
|
|
|
|
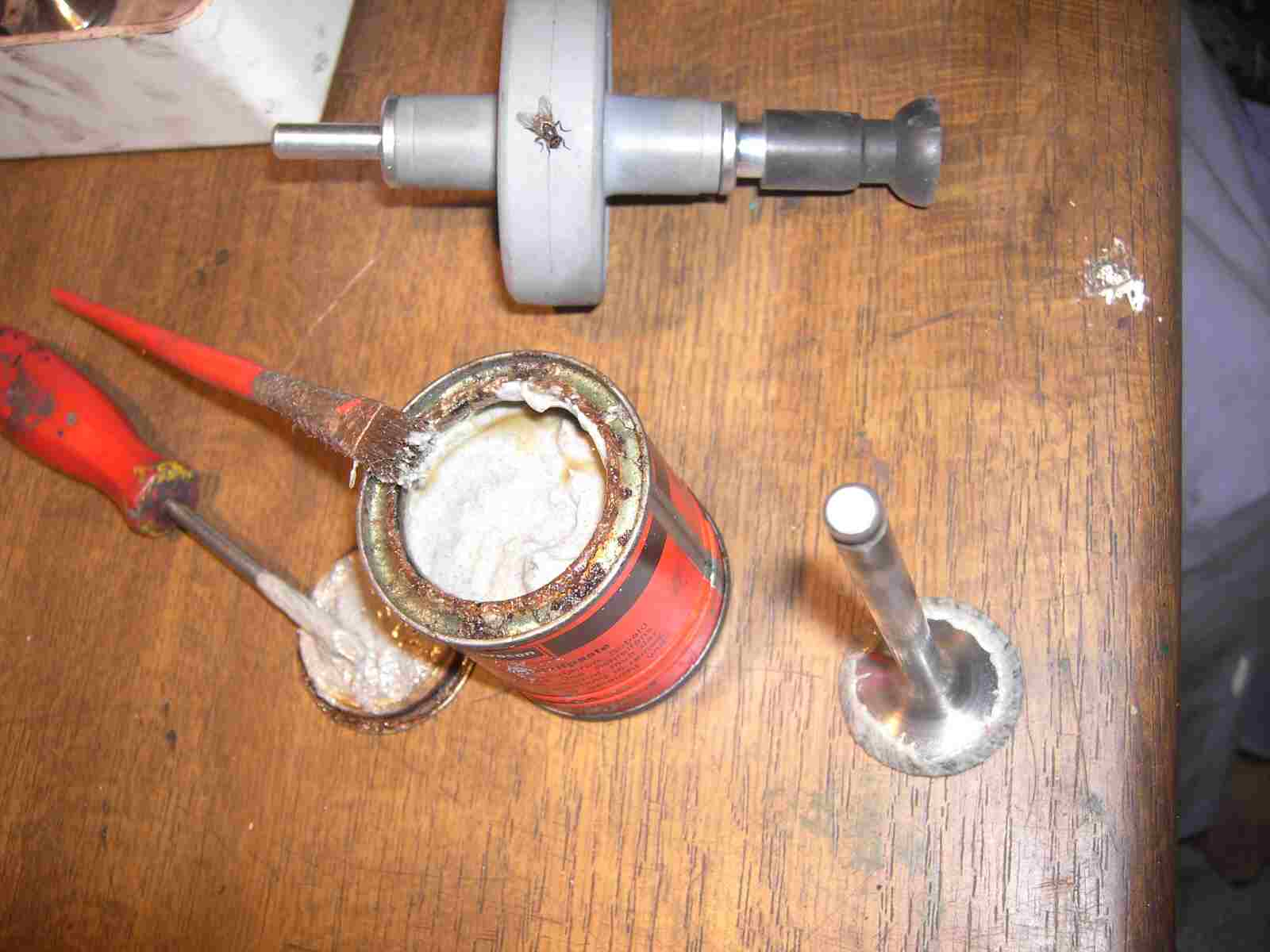 |
|
|
|
Mit einem Pinsel trage ich auf dem Dichtungsrand, vom Ventil, die Vorschleifpaste auf.
|
|
|
|
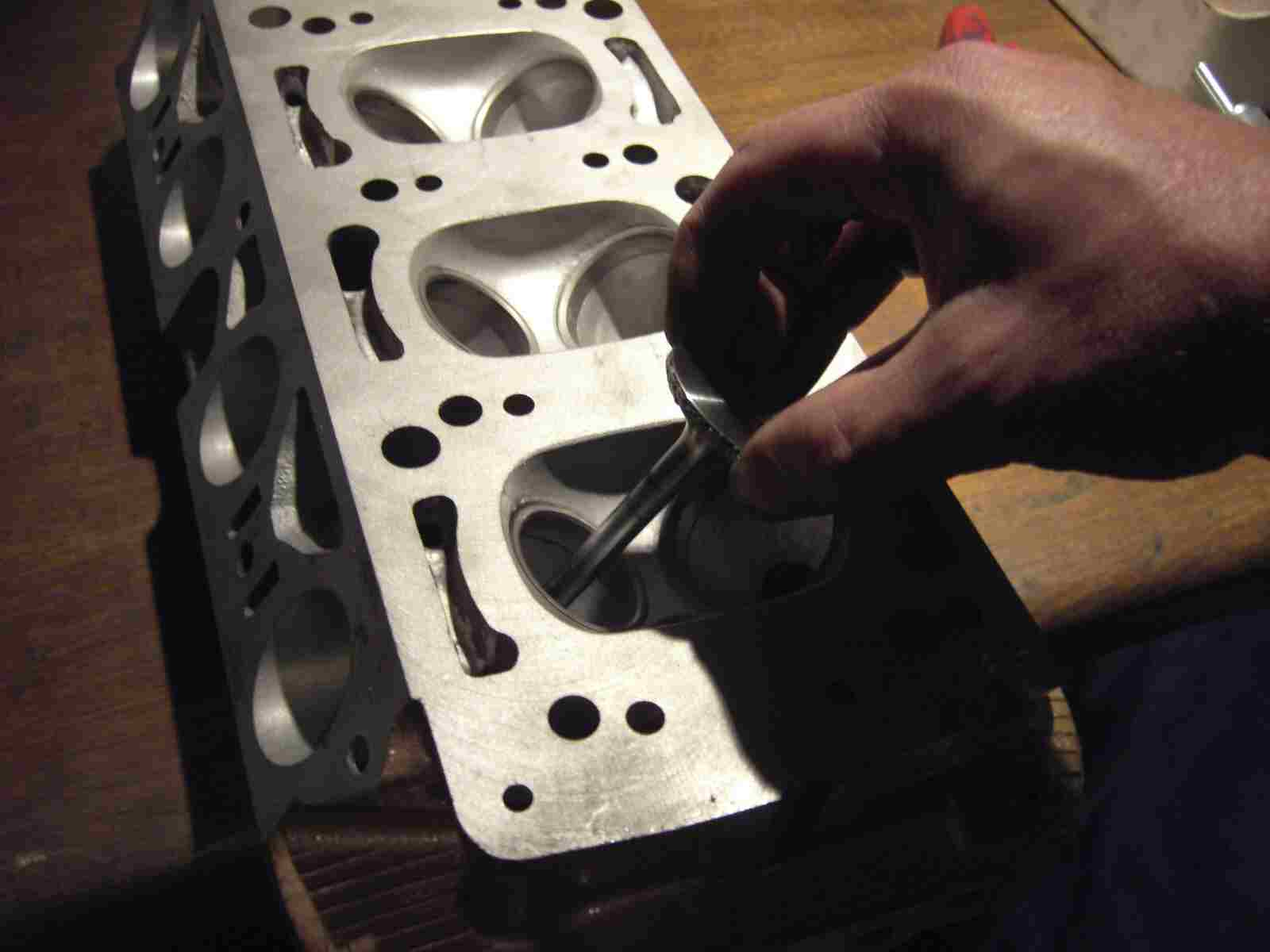 |
|
|
|
Ventil in den Zylinderkopf stecken!
|
|
|
|
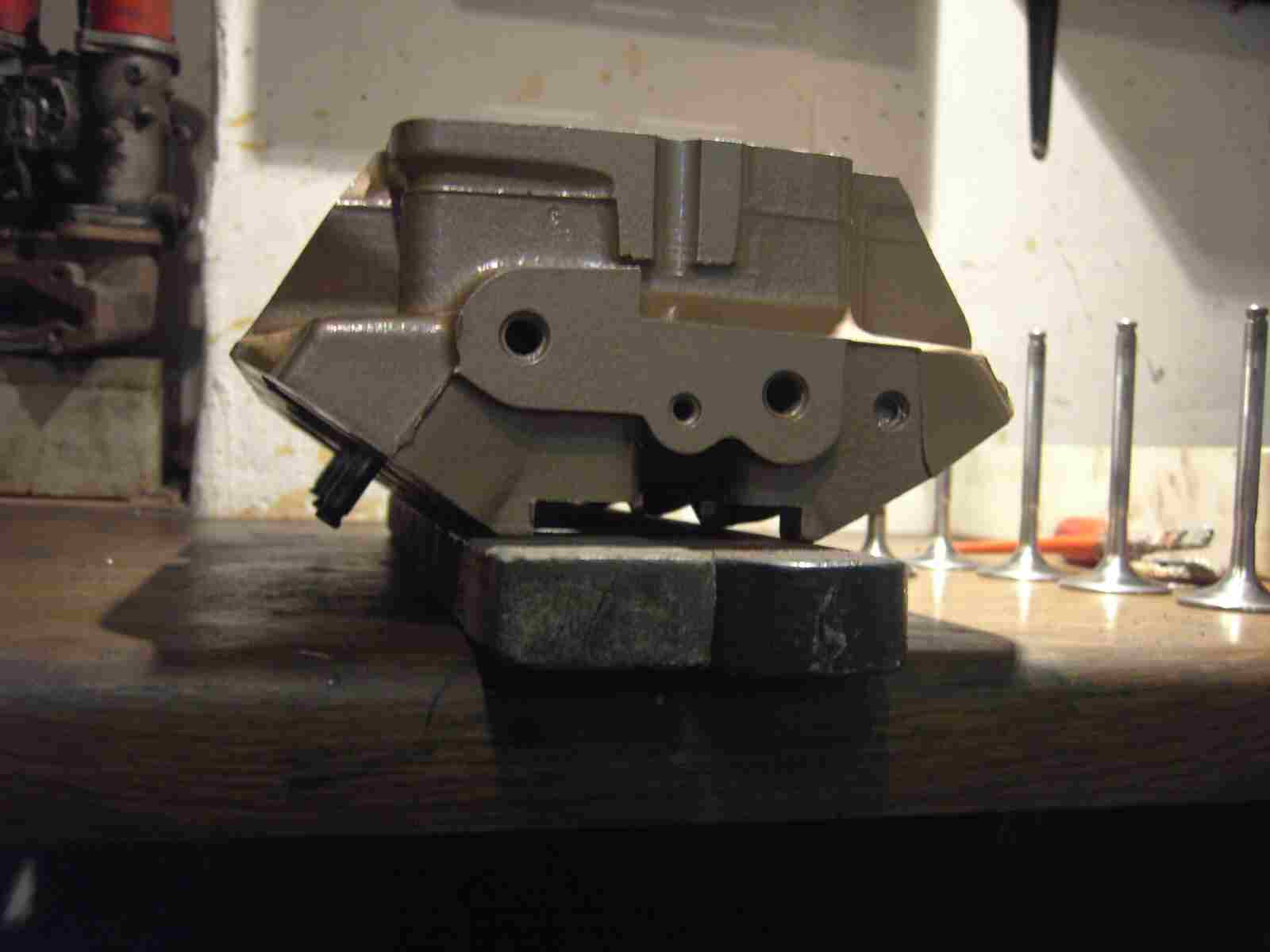 |
|
|
|
Den Zylinderkopf habe ich mit ein paar Holzlatten unterlegt, so steht der Ventilschaft schön im Freien.
|
|
|
|
 |
|
|
|
Ventil liegt schön im Ventilsitz!
|
|
|
|
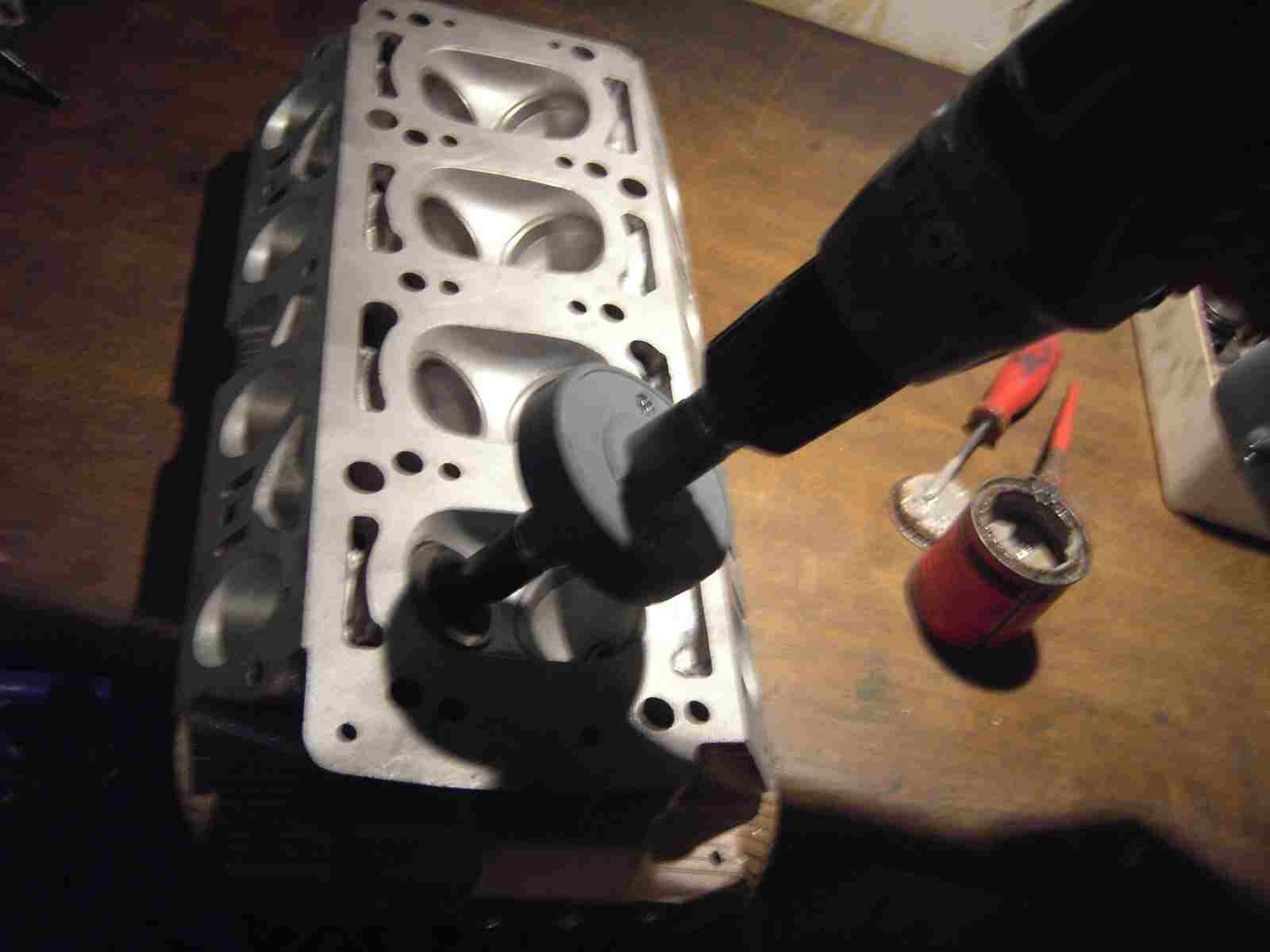 |
|
|
|
Jetzt kommt das Ventileinschleifgerät, mit der Akkubohrmaschine, zum Einsatz. So, wie ich es hier zeige, funktioniert es natürlich nicht. Man benötigt dazu beide Hände, aber eine benötige ich für die Kamera. Mit der einen Hand hält man die Bohrmaschine und mit der anderen das dicke Teil des Einschleifgerätes. Dadurch wird das Ventil mit dem Saugnapf nach rechts und links eingeschliffen. Dabei übt man fast keinen Druck aus und manchmal lasse ich kurz das Einschleifgerät los und dadurch dreht sich das Ventil einmal ganz um 360°. Die Einschleifposition wird dadurch verändert.
|
|
|
|
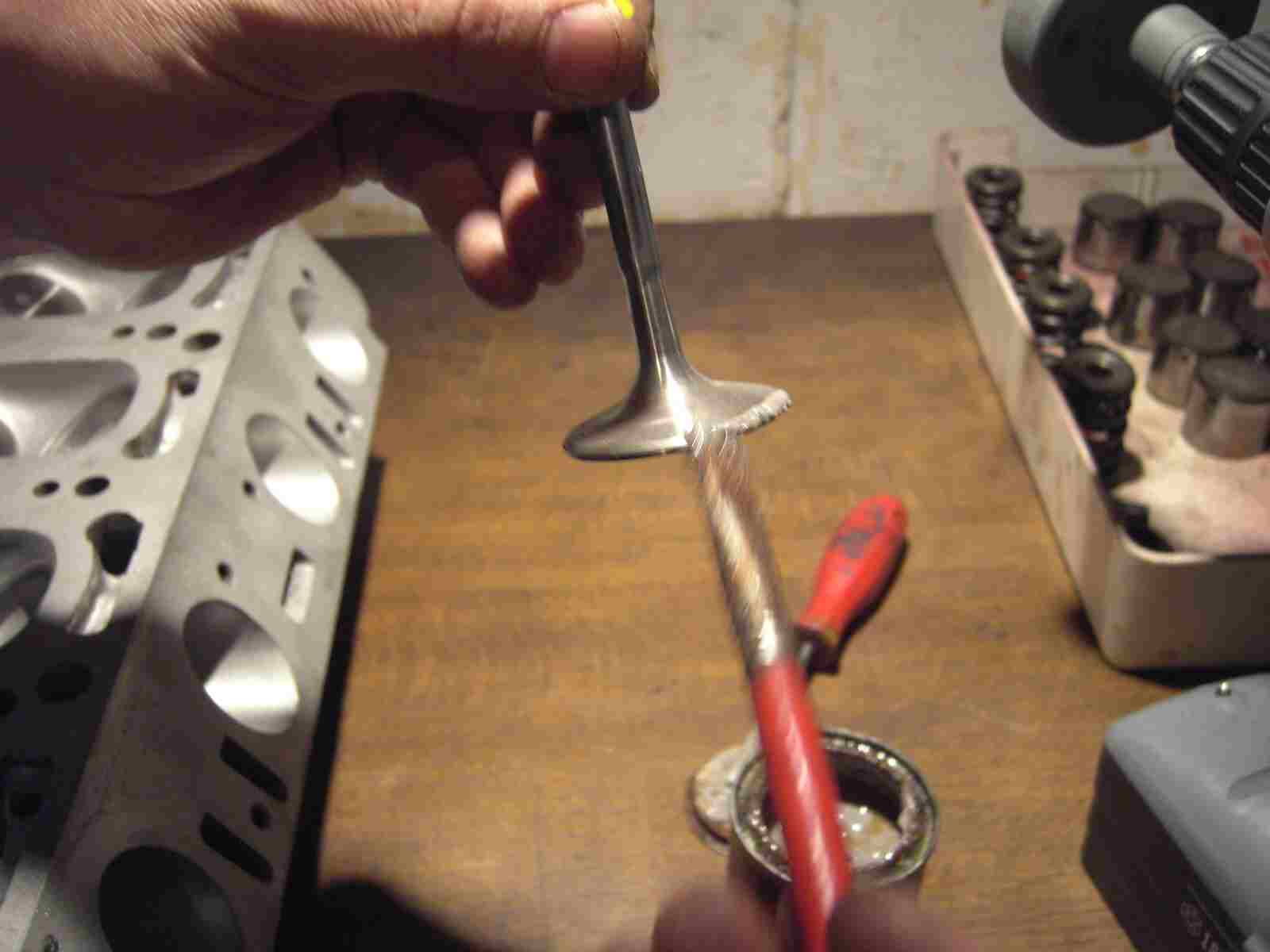 |
|
|
|
Um das Ganze zu beschleunigen, trage ich auf jedes Ventil die Vorschleifpaste auf!
|
|
|
|
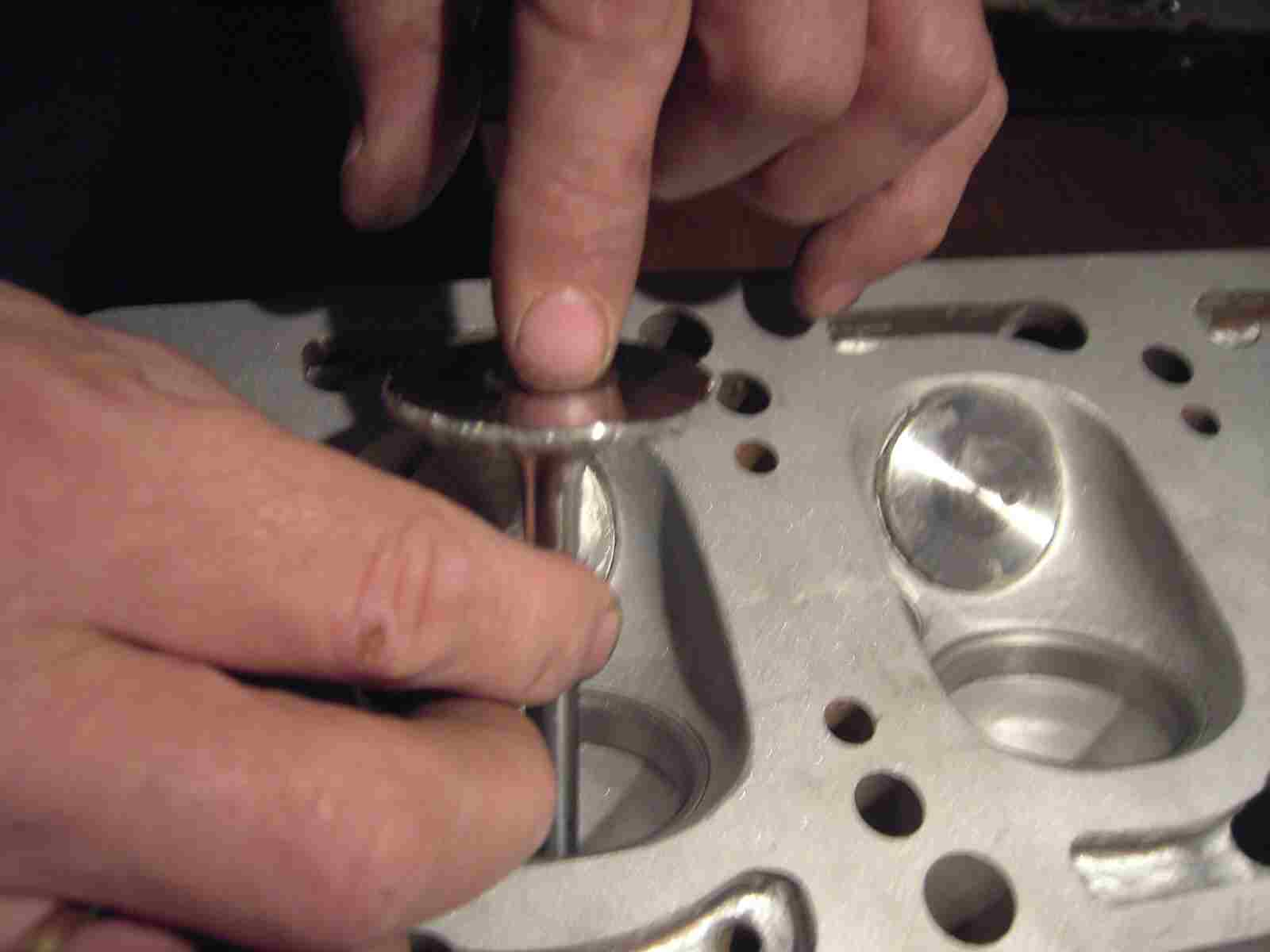 |
|
|
|
Ventile in den Zylinderkopf stecken!
|
|
|
|
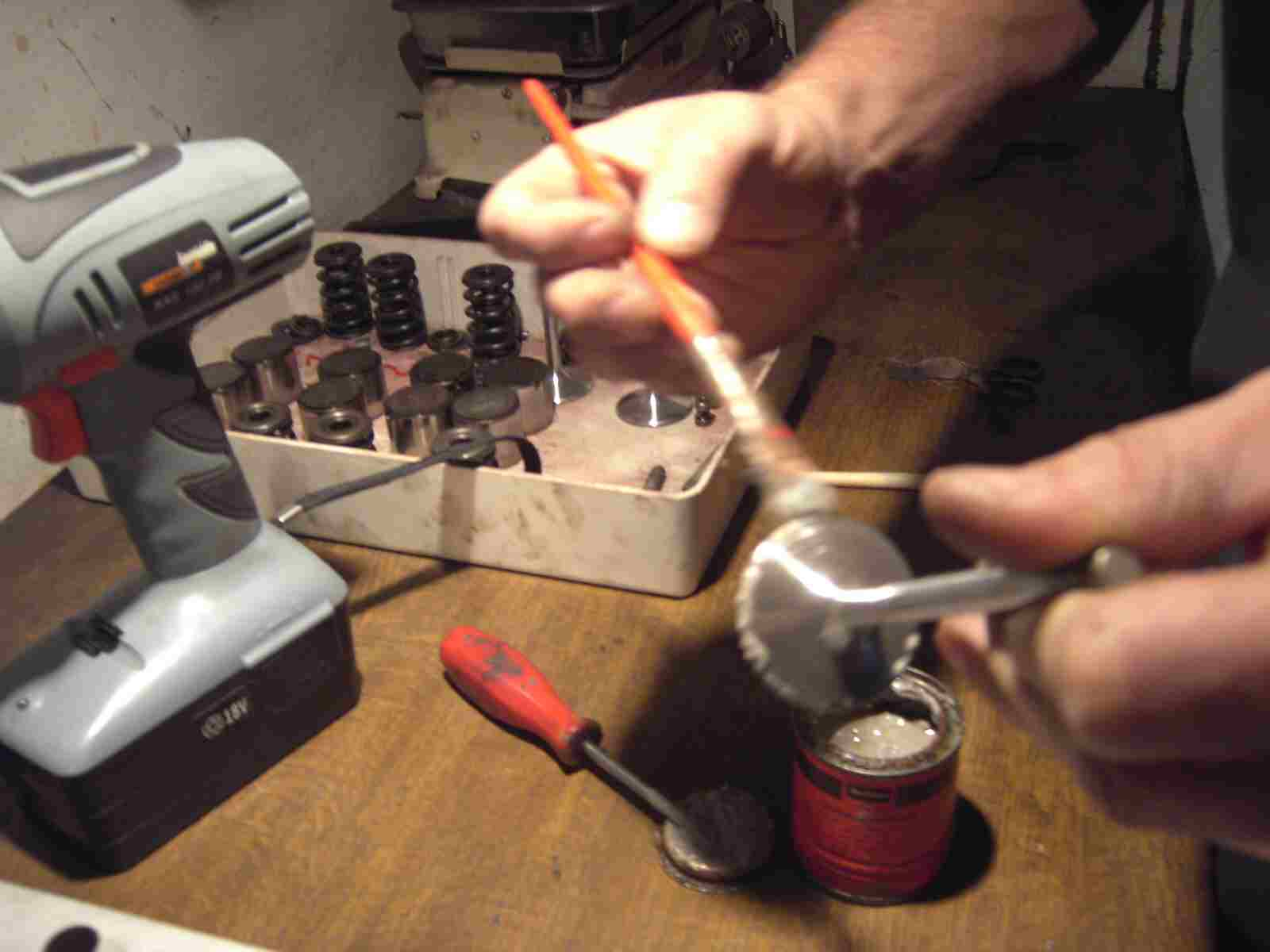 |
|
|
|
Und das nächste Ventil!
|
|
|
|
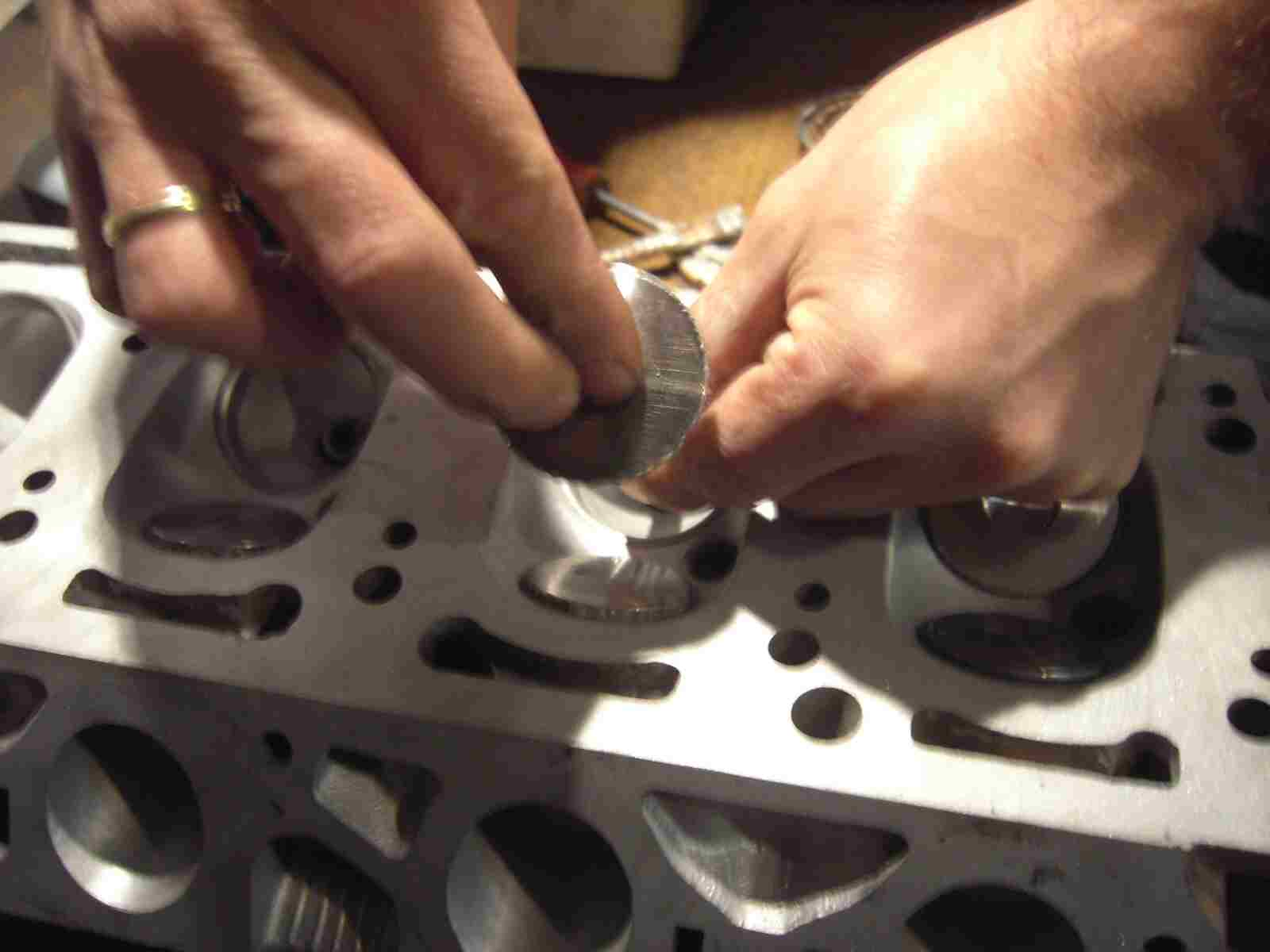 |
|
|
|
Auf alle Ventile wird Schleifpaste aufgetragen und in den Kopf plaziert. Dann kann ich mit dem Einschleifgerät alle Ventile durch gehend einschleifen.
|
|
|
|
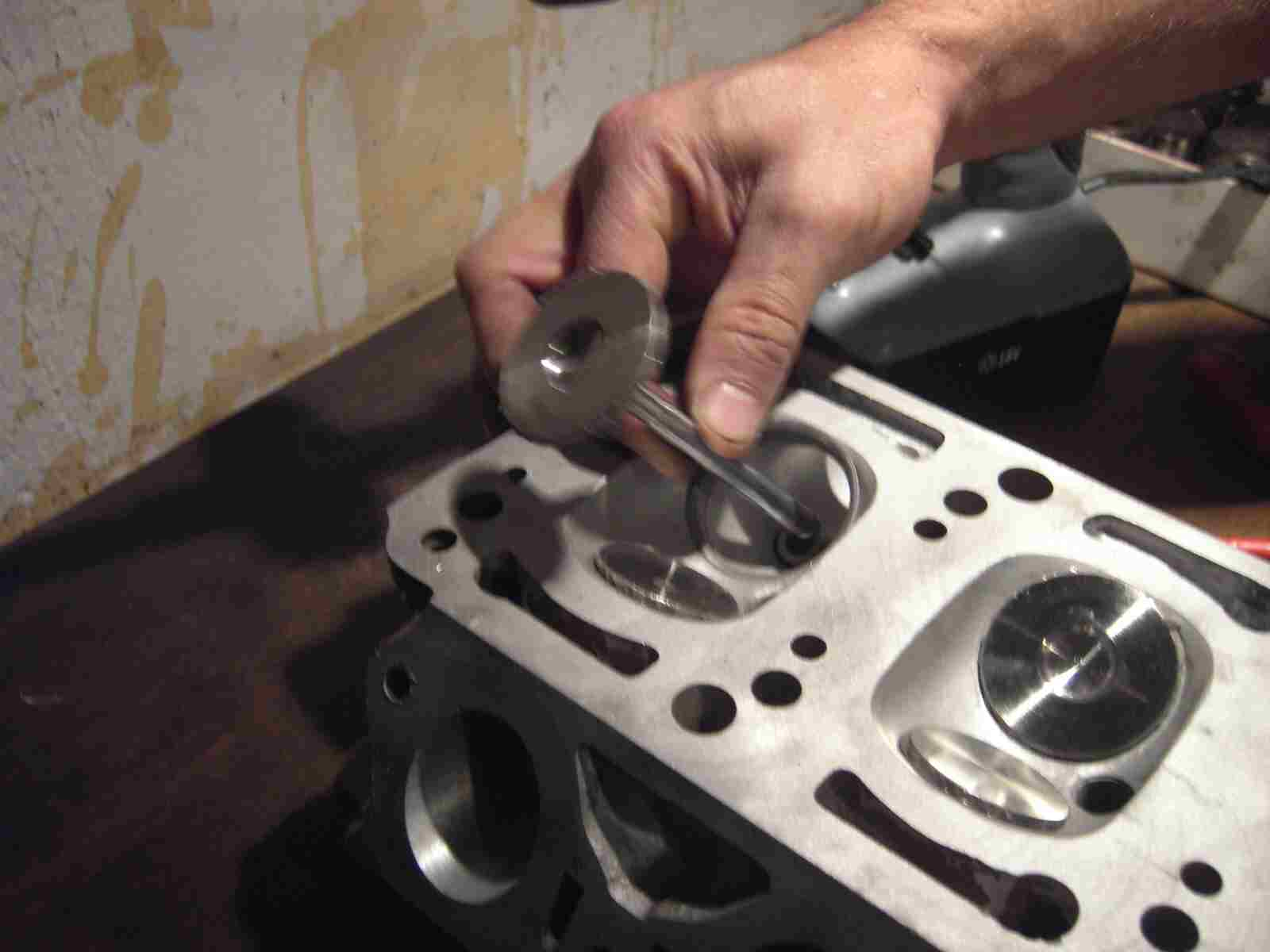 |
|
|
|
Ventil einsetzen!
|
|
|
|
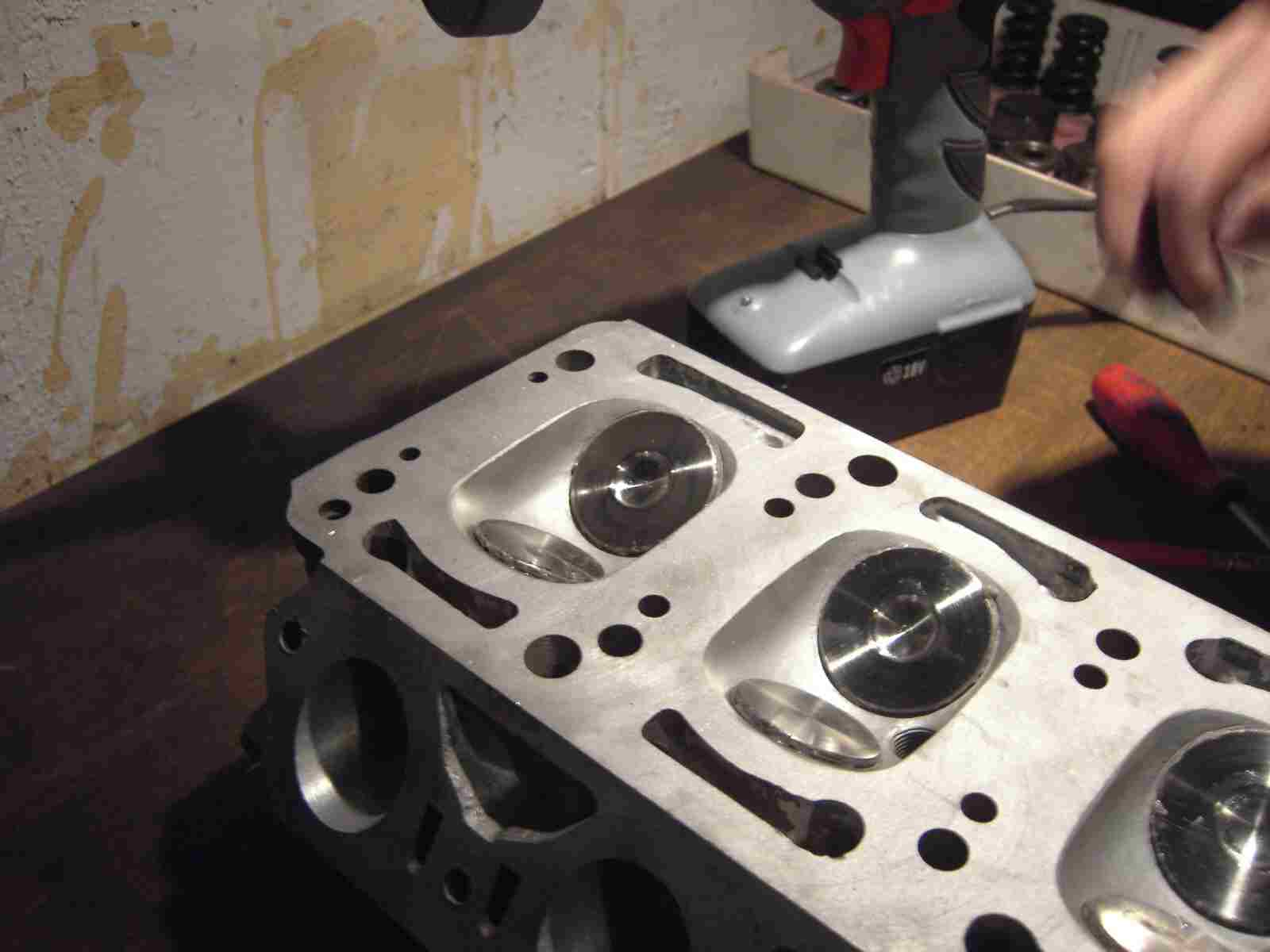 |
|
|
|
So fertig, alle Ventile sind jetzt zum Schleifen vorbereitet!
|
|
|
|
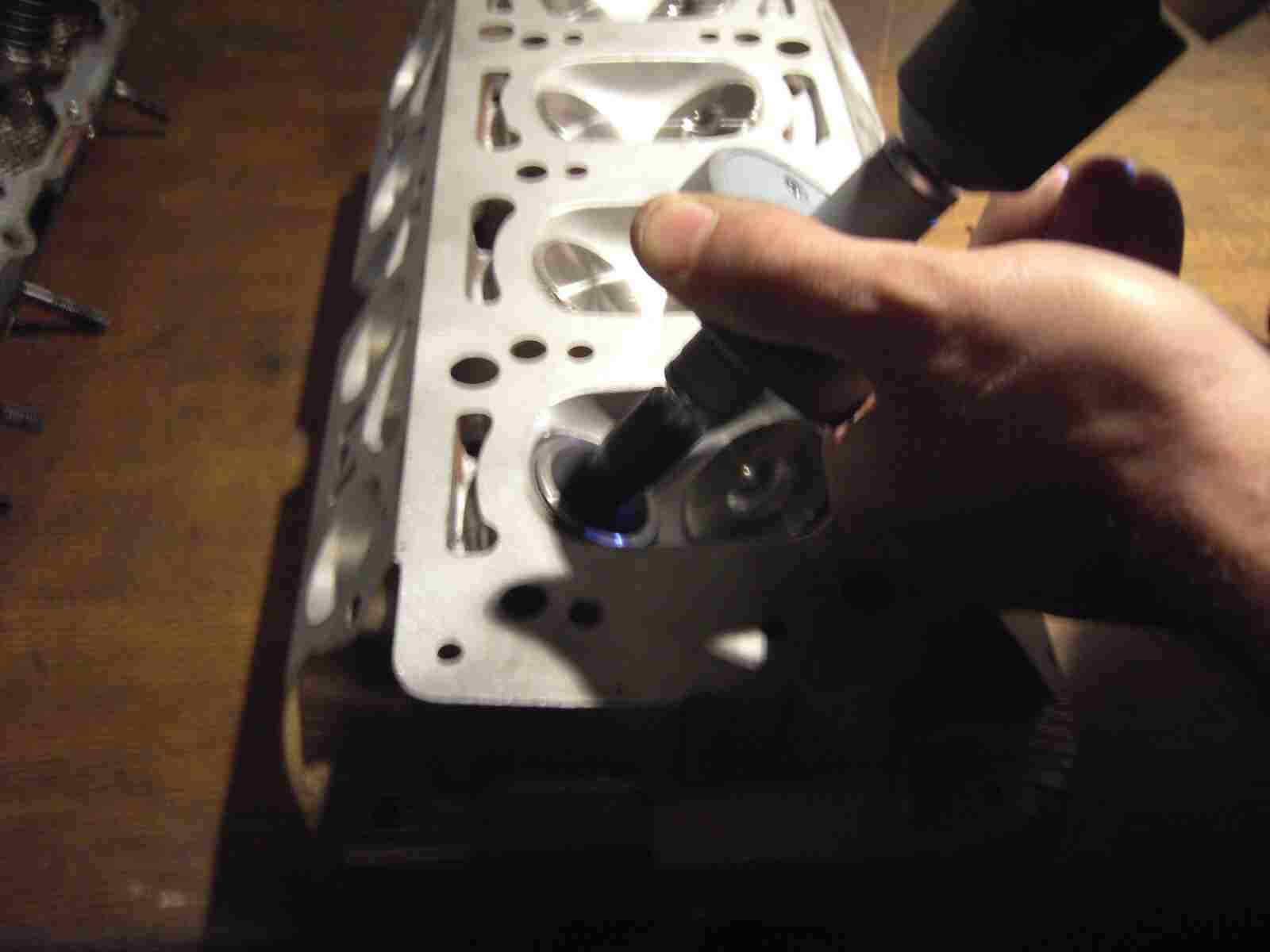 |
|
|
|
Und jetzt wird eingeschliffen und zwar diesmal mit beiden Händen.
|
|
|
|
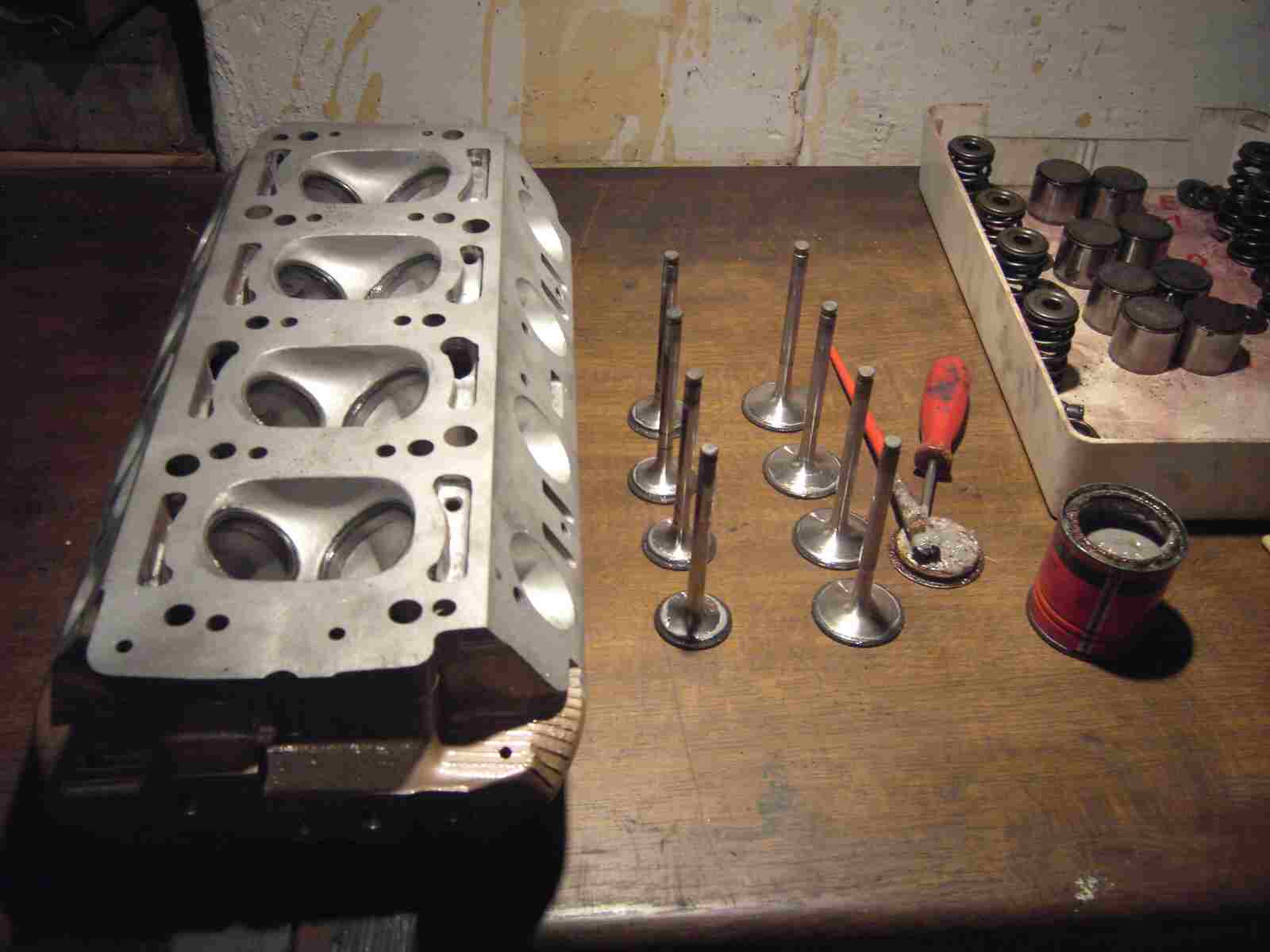 |
|
|
|
Die Ventile sind nun vorgeschliffen worden und aus dem Zylinderkopf entfernt. Achtung, die Ventile jetzt bloss nicht mehr verwechseln, ansonsten werden diese nie dicht!
|
|
|
|
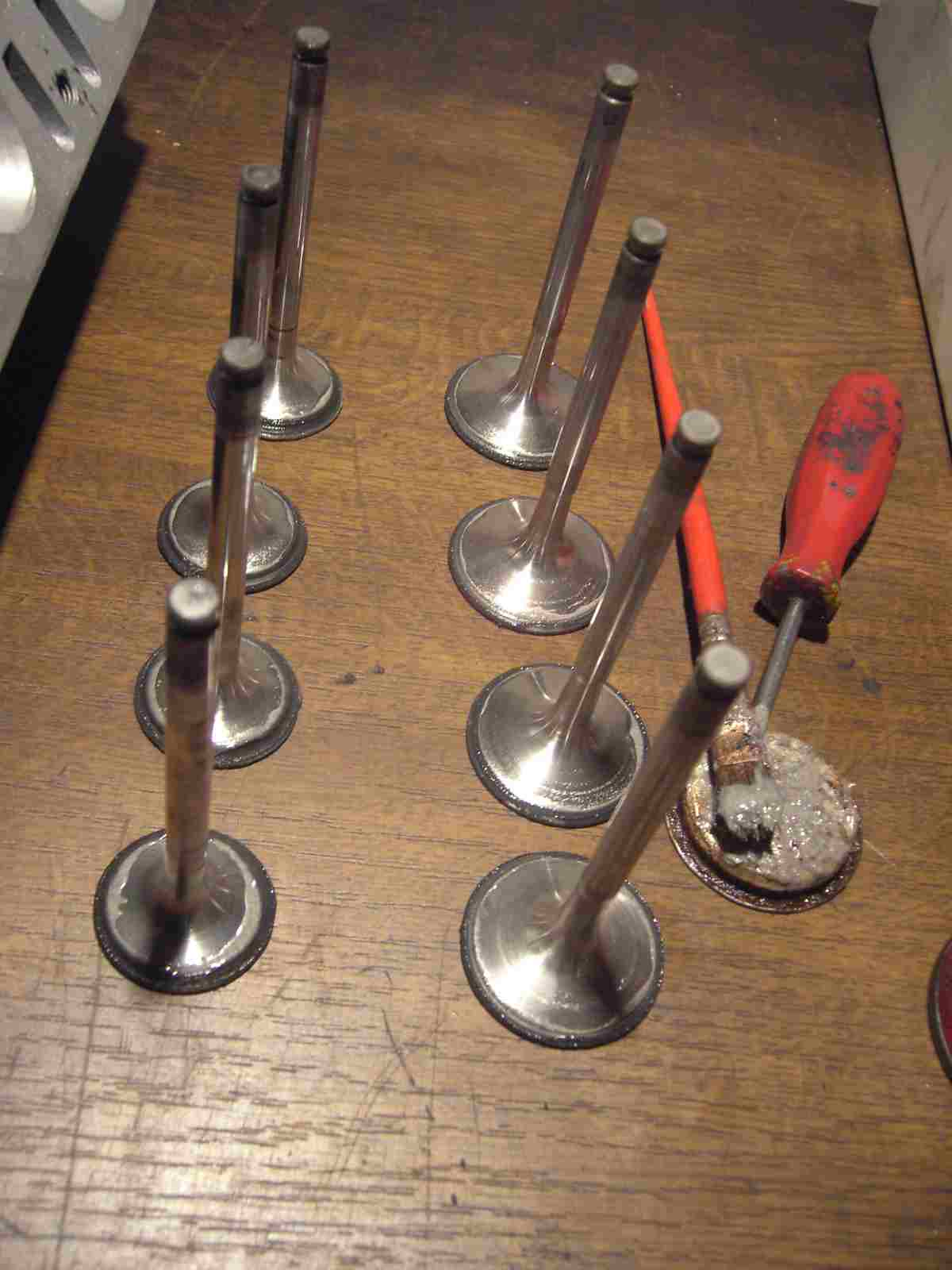 |
|
|
|
Und wie sind nun das Einschleifergebnis aus?
|
|
|
|
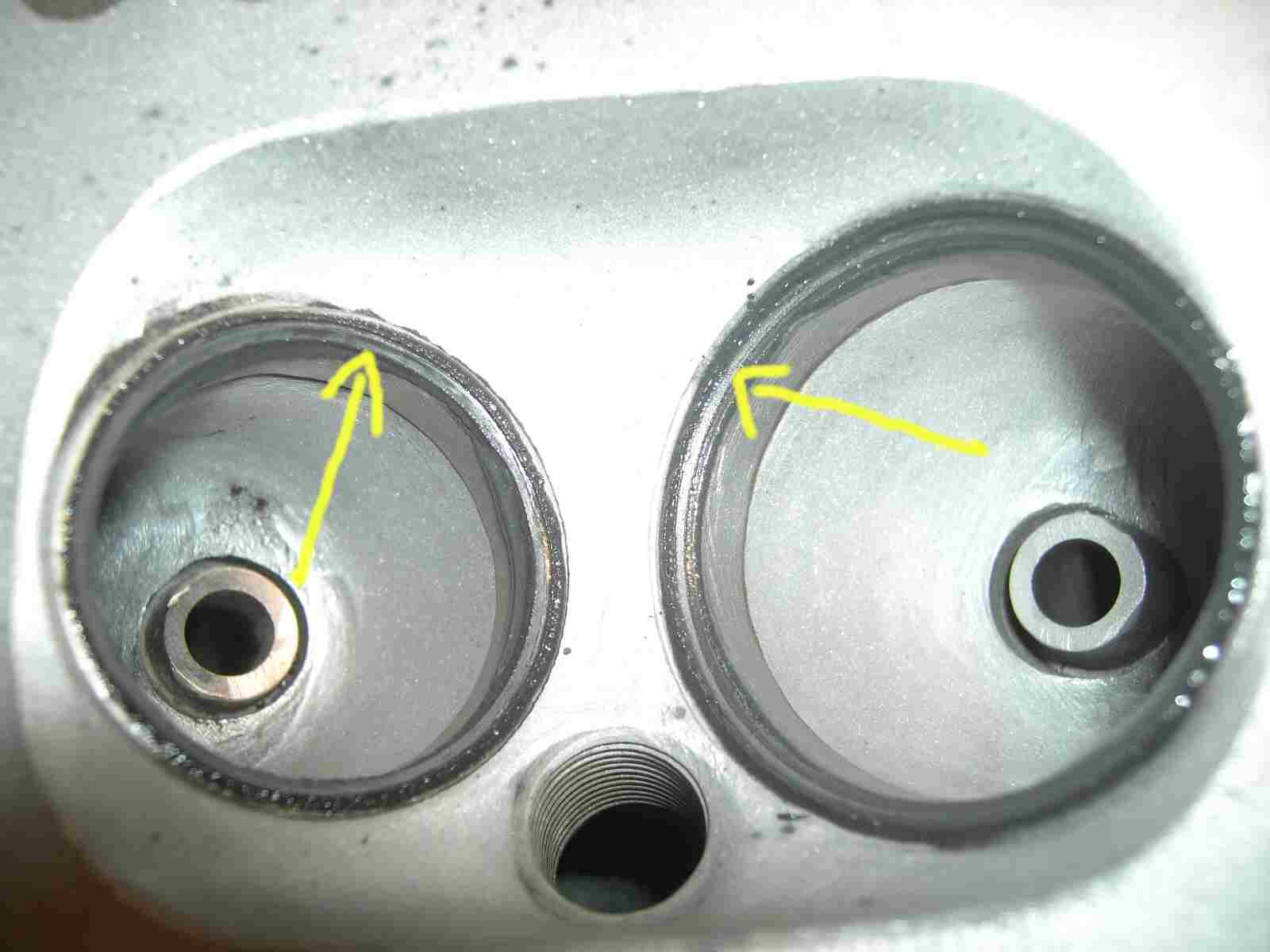 |
|
|
|
Am Ventilsitz muss ringsrum ein gleichmässiger, blanker Rand entstehen. Sollte eine Unterbrechung vorhanden sein, dann müßt Ihr dieses Ventil noch einmal einsetzen und mit der Vorschleifpaste einschleifen. Eine Dichtsheitsprobe würde bei einem unterbrochenen Rand nicht erfolgreich verlaufen.
|
|
|
|
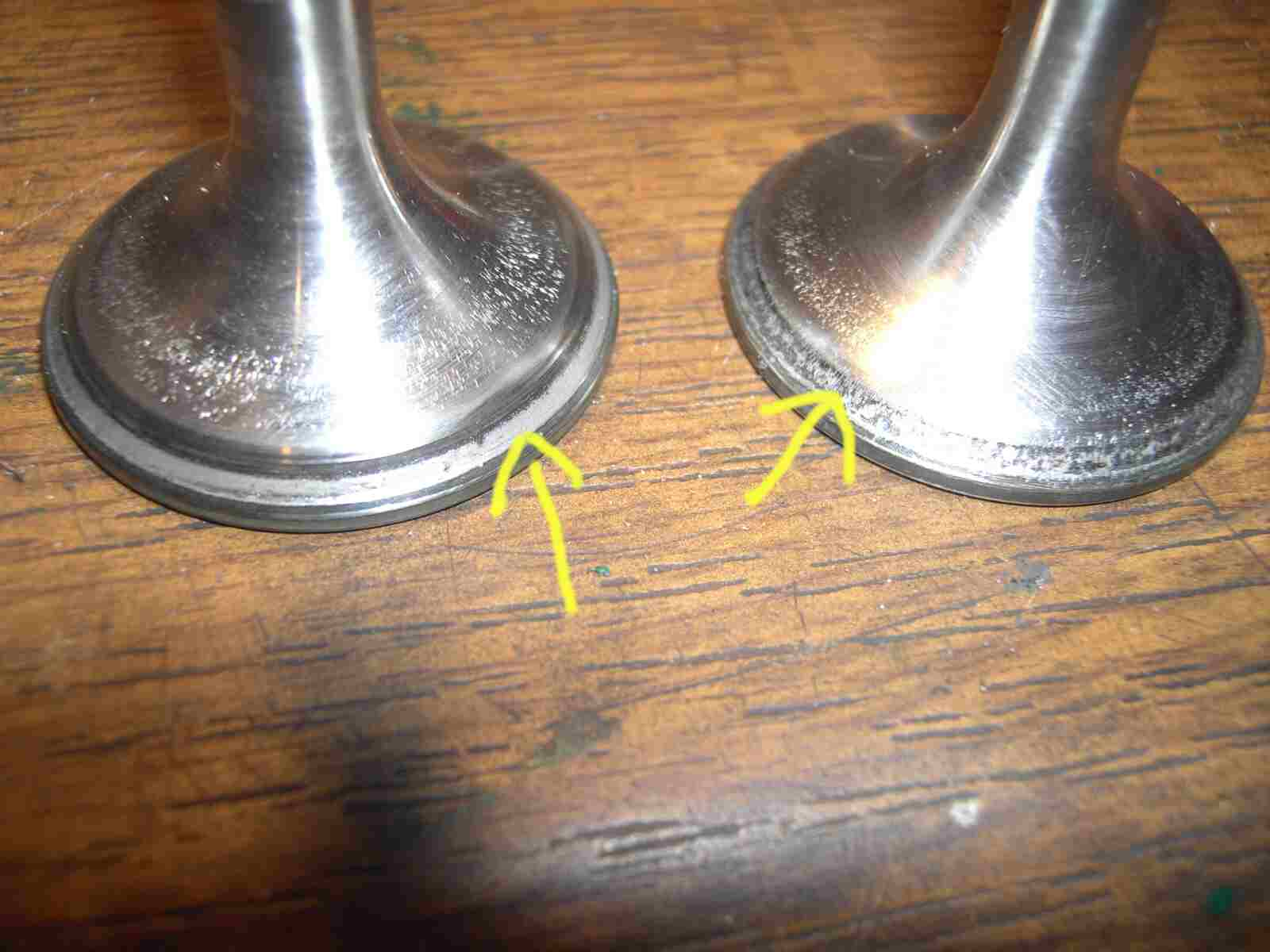 |
|
|
|
Und das Gleiche gilt auch für das Ventil. Es muss ein gleichmässiger, blanker Rand entstehen und nicht wie das Auslassventil rechts. Es hat noch viele unterbrochene Stellen und kann nicht dicht sein. Es ist beim Auslassventil aber normal, weil es höheren Temperaturen ausgesetzt ist. Gerade, wie hier beim Turbomotor!
|
|
|
|
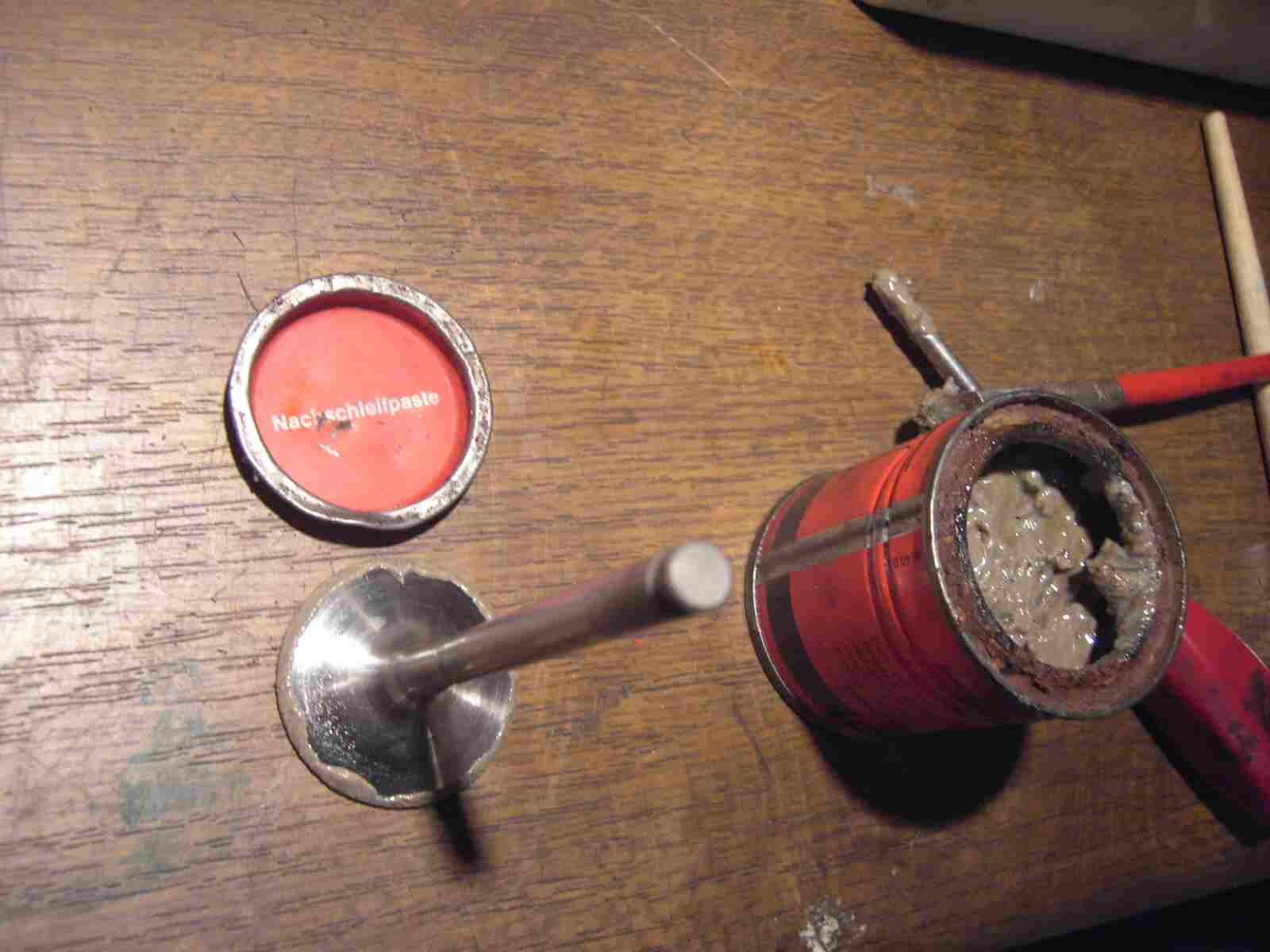 |
|
|
|
Ich verwende als nächstes die feine Nachschleifpaste. Diese wird, wie die Vorschleifpaste, auf das Ventil aufgetragen. Übrigens, meine Dose mit Ventilschleifpaste ist schon über 10 Jahre alt und reicht noch für einige Zylinderköpfe. Sollte die Schleifpaste mal ausgetrocknet sein, dann nehmt etwas Motoröl und rührt damit wieder einen schönen Brei auf.
|
|
|
|
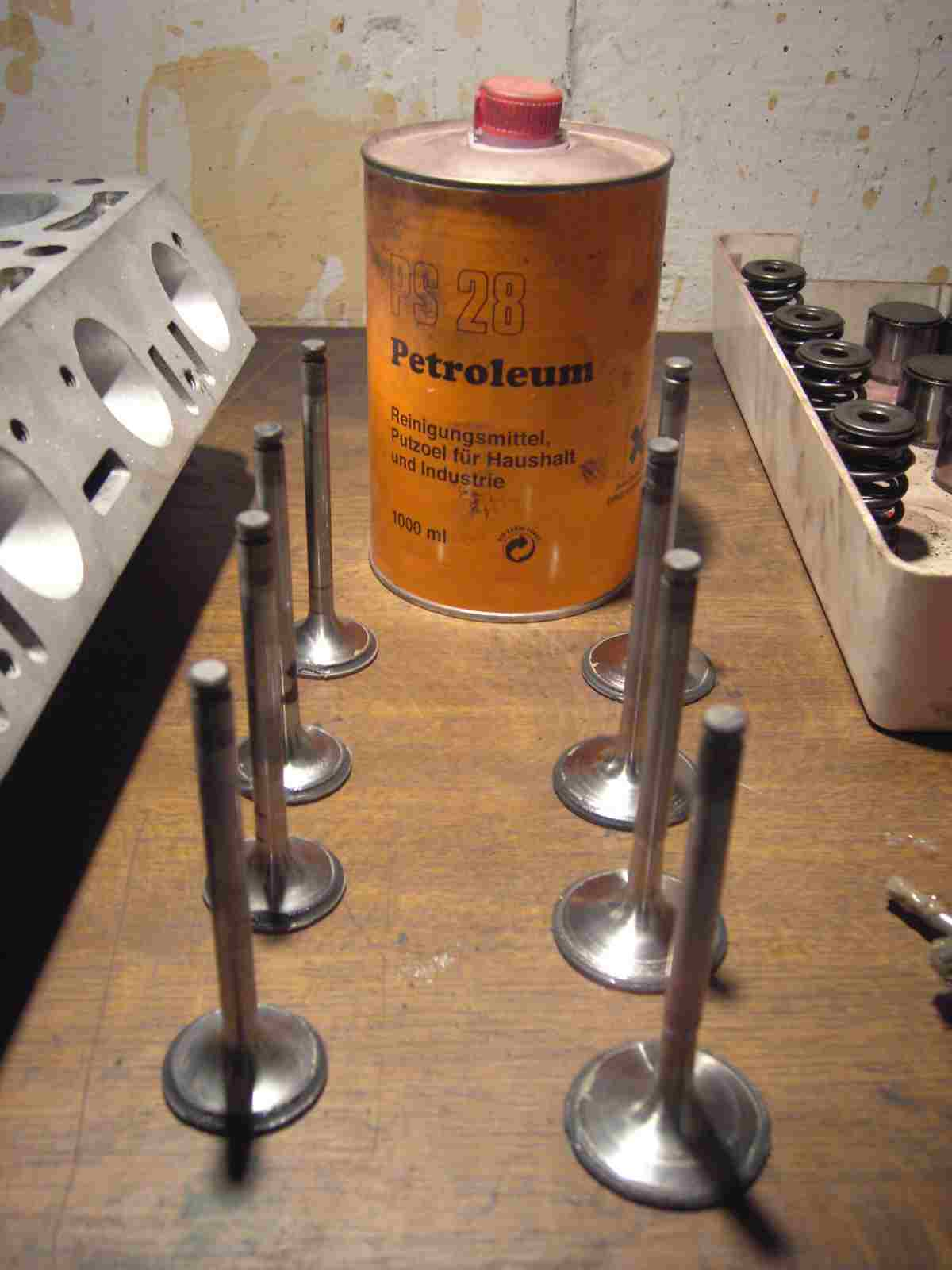 |
|
|
|
Die Ventile sind nun alle mit der Feinschleifpaste nachgeschliffen worden und sehen am Dichtrand ganz gut aus. Hinten könnt ihr eine DosePetroleum sehen. Mit Petroleum werden die Ventile von der Schleifpaste befreit.
|
|
|
|
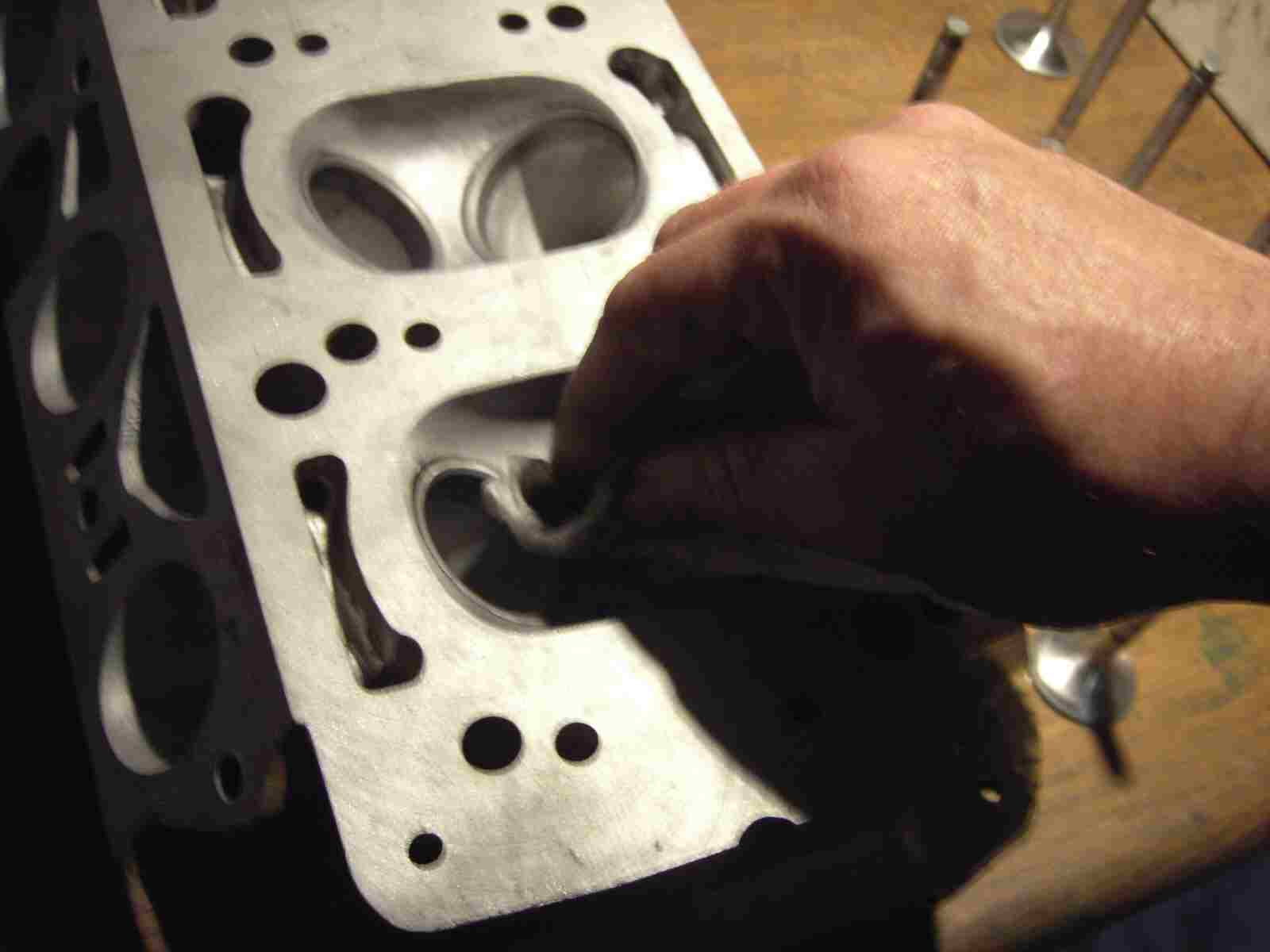 |
|
|
|
Der Ventilsitzring wird auch mit Petroleum gesäubert.
|
|
|
|
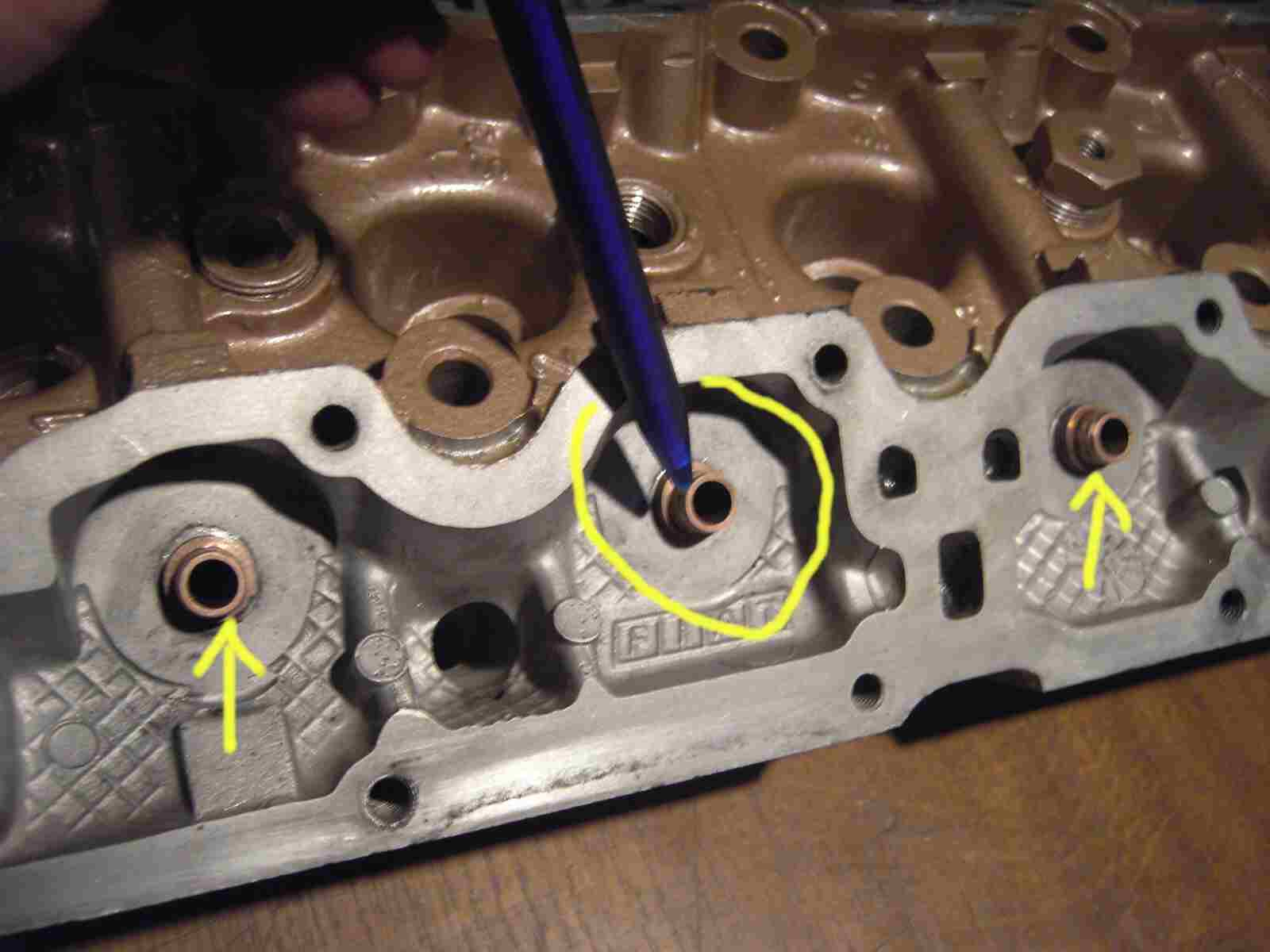 |
|
|
|
Das sind die Ventilführungen! Diese sind beim Turbomotor in Rotguss (Messing mit hohem Anteil an Kupfer) ausgeführt. Am Beta bestehen dies aus Grauguss.
|
|
|
|
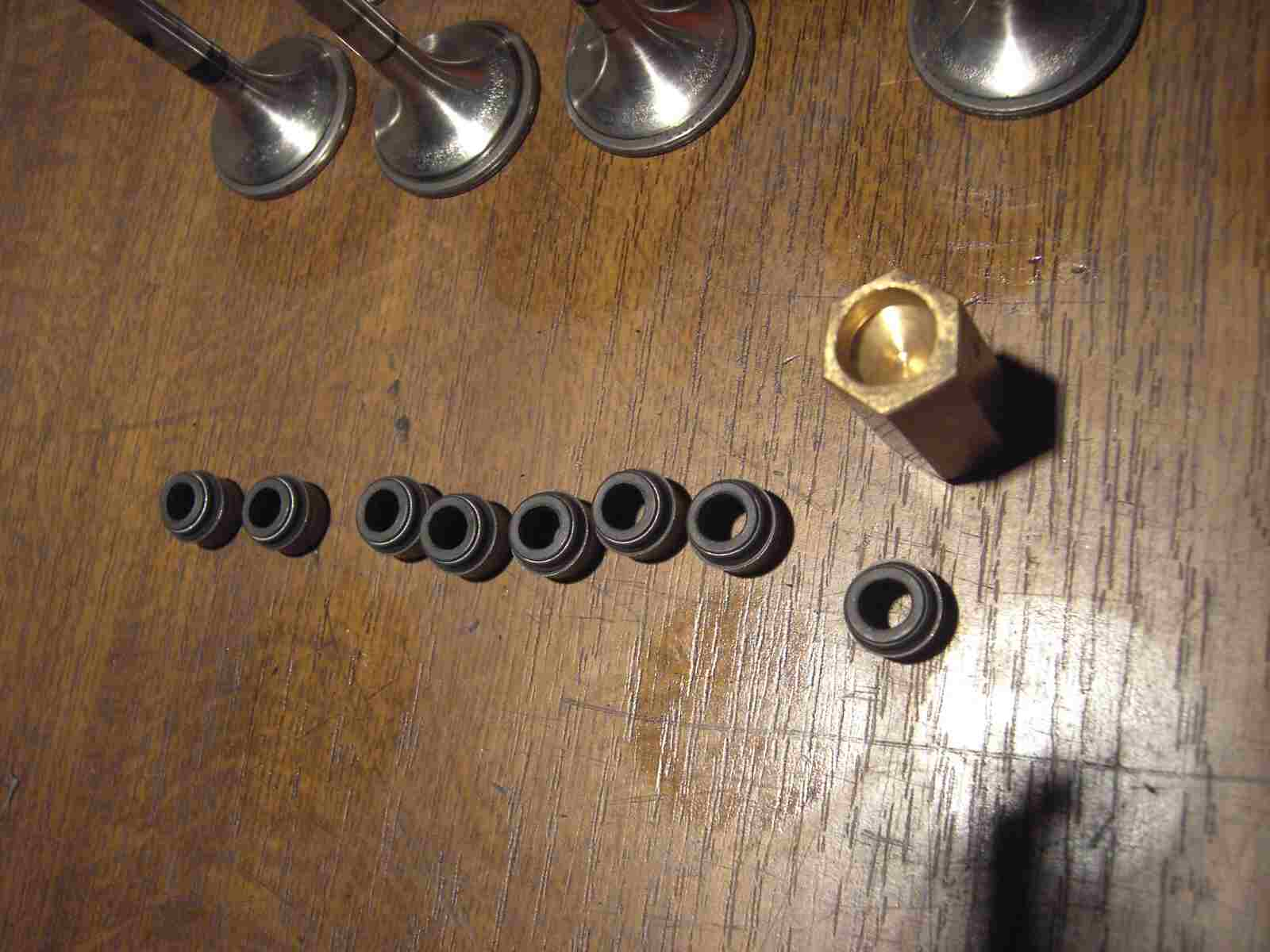 |
|
|
|
Bevor ich die Dichtheitsprüfung durchführe, müssen die Ventilschaftdichtungen montiert werden. Dafür habe ich in ein Messingsechskant ein Loch gebohrt, das größer als das Gummi ist und denoch auf den Blechring drückt. Wenn Ihr nicht so ein Teil anfertigen könnt, dann nehmt einfach eine passende Nuss aus Eurem Werkzeugbestand! Geht auch!
|
|
|
|
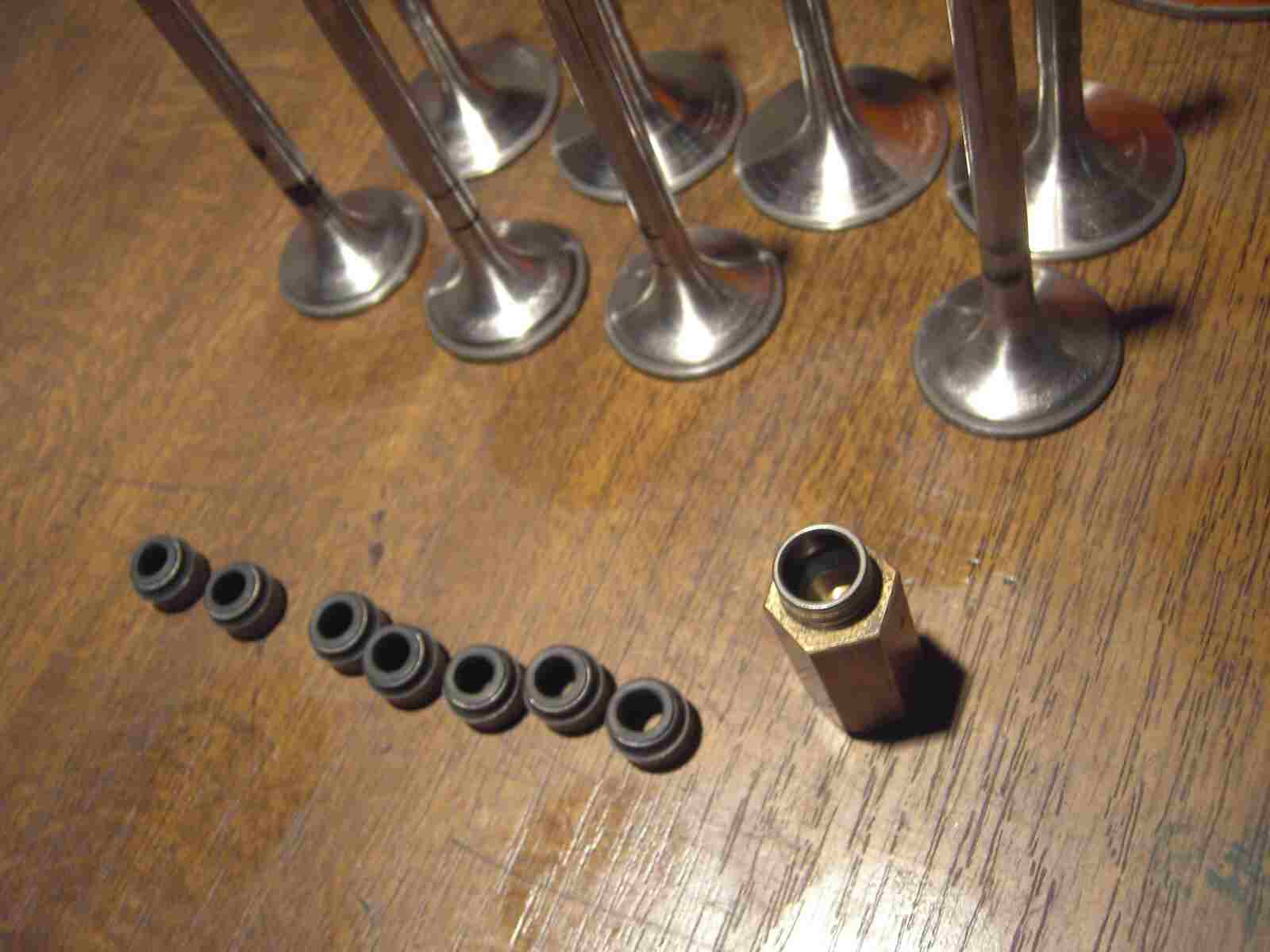 |
|
|
|
So sieht die Ventilschaftdichtung in meinem Messingteil aus.
|
|
|
|
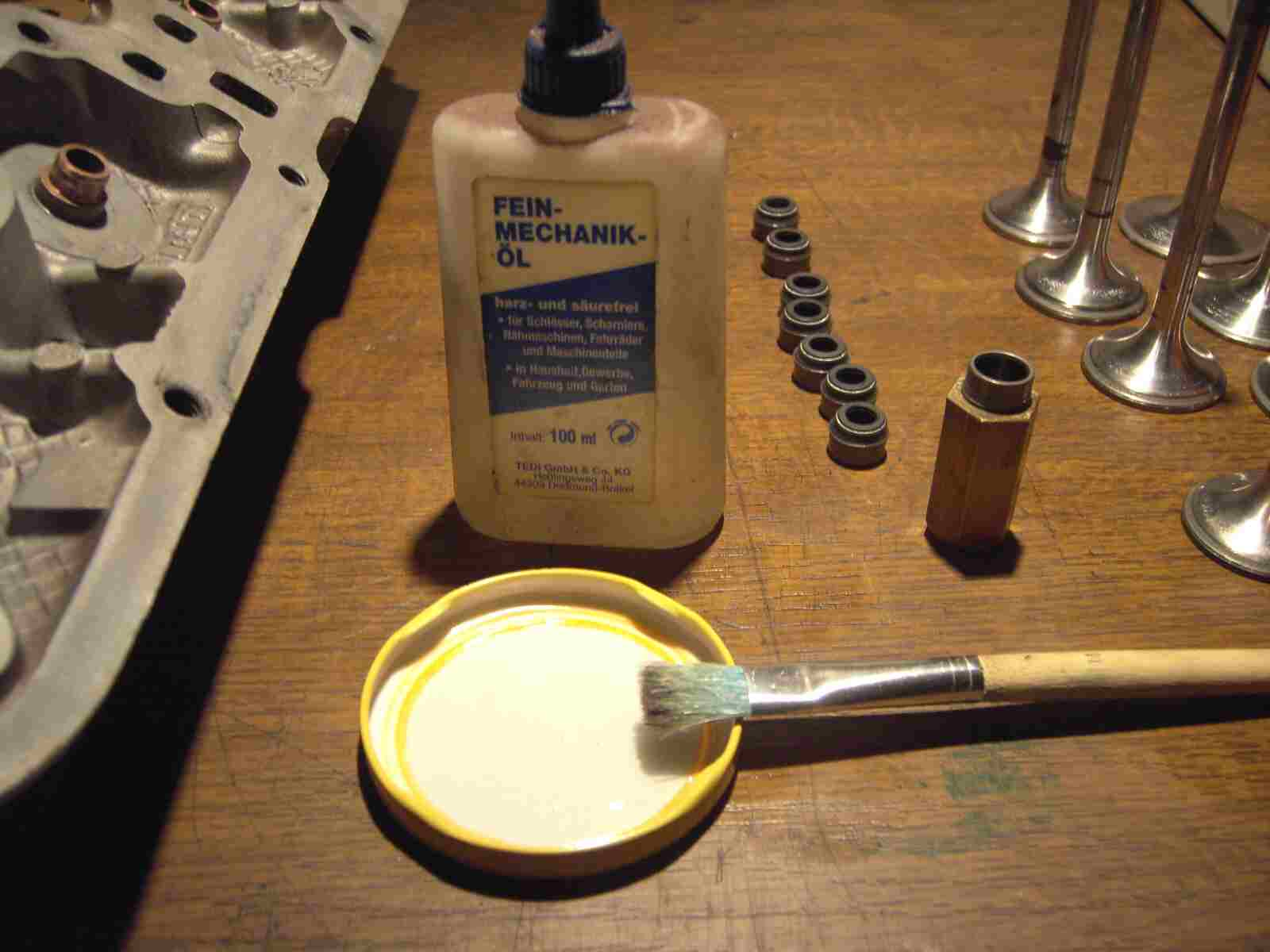 |
|
|
|
Als Profi benutze ich noch etwas Feinmechanikeröl und zwar für die Ventilschaftdichtung und für das Ventil.
|
|
|
|
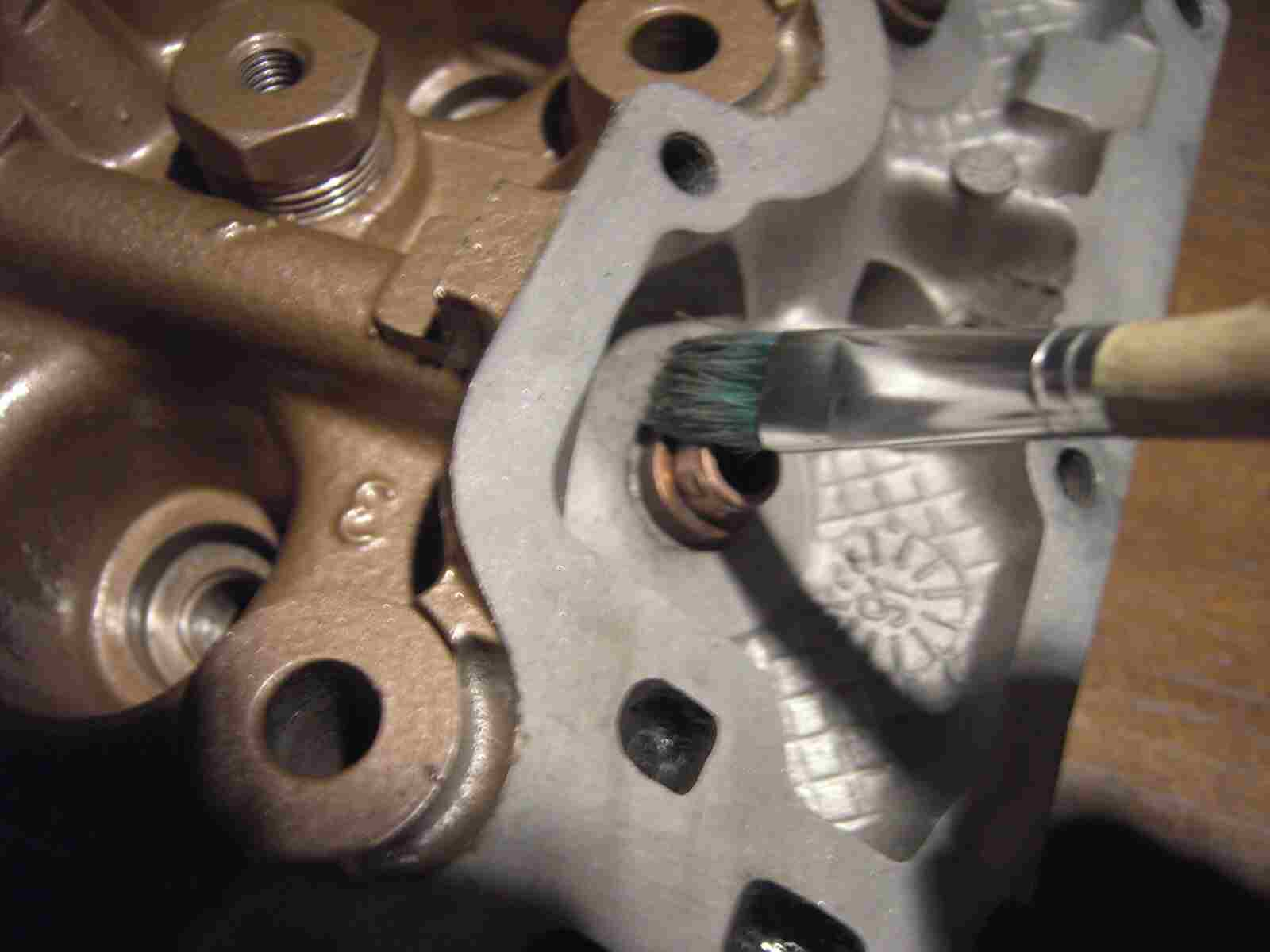 |
|
|
|
Als erstes streiche ich den Ventilführung mit dem Öl ein!
|
|
|
|
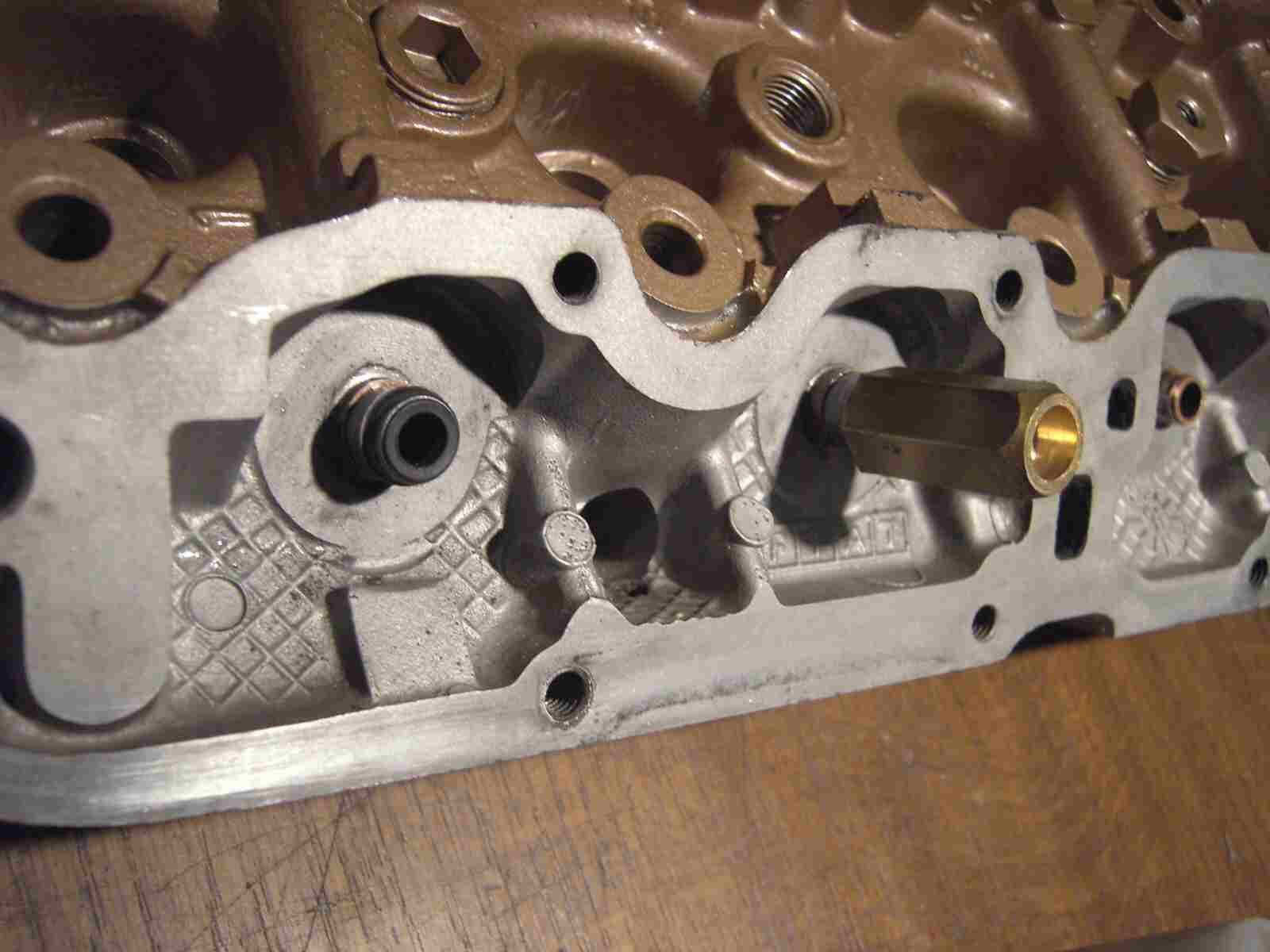 |
|
|
|
Und dann wird die Ventilschaftdichtung mit meinem Spezialwerkzeug (Nuss geht auch) auf die Ventilführung getrieben, mit leichten schlägen! Klopft nicht zu fest, sonst wird die Dichtung beschädigt! Ob diese richtig sitzt, könnt Ihr am Absatz der Ventilführung sehen. Ist dieser nicht mehr vorhanden, ist die Dichtung richtig eingesetzt!
|
|
|
|
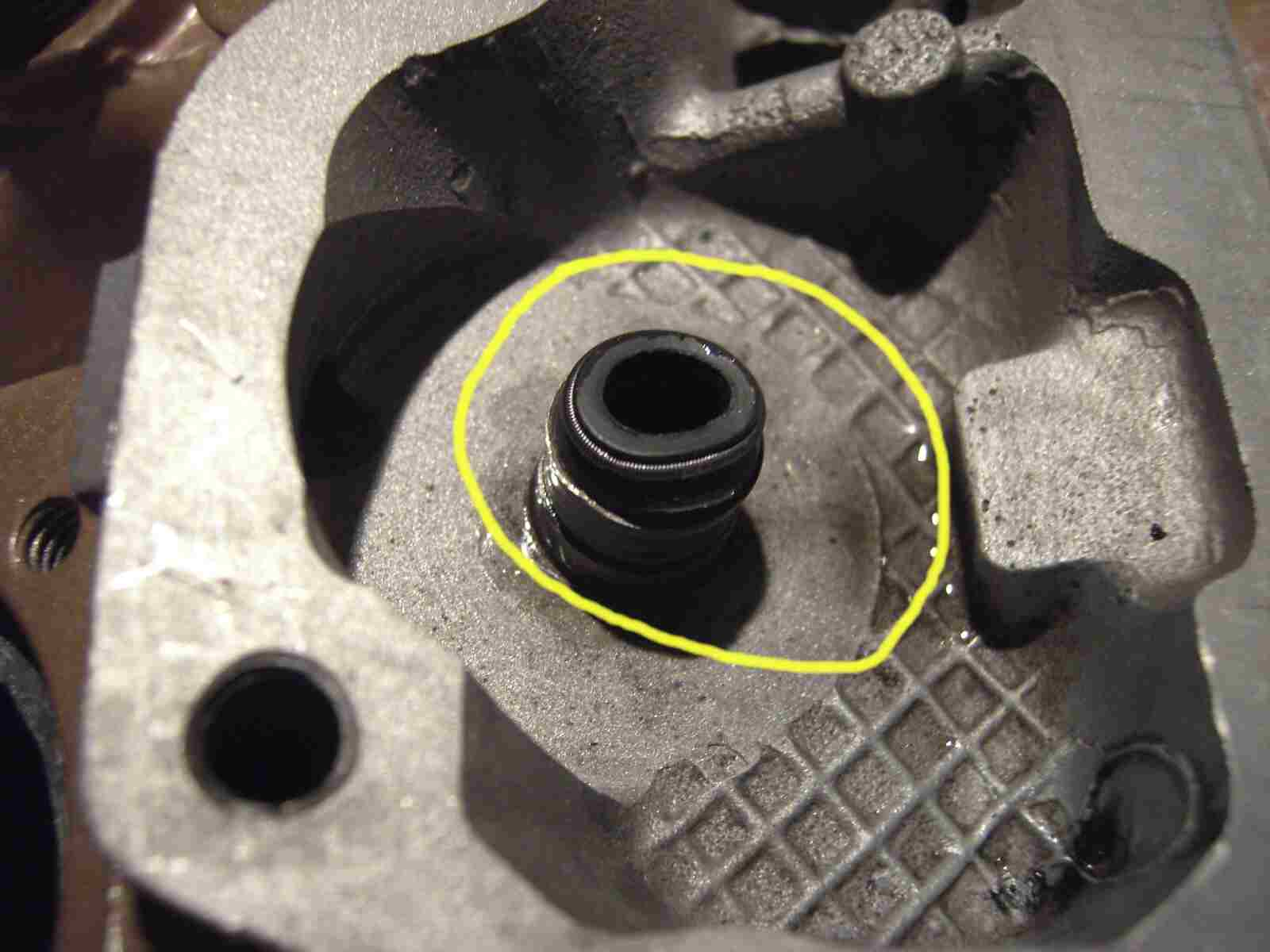 |
|
|
|
So soll es nicht aussehen! Diese Ventilschaftdichtung ist zu stark angeklopft worden und dazu krumm. Diese muss wieder entfernt werden!
|
|
|
|
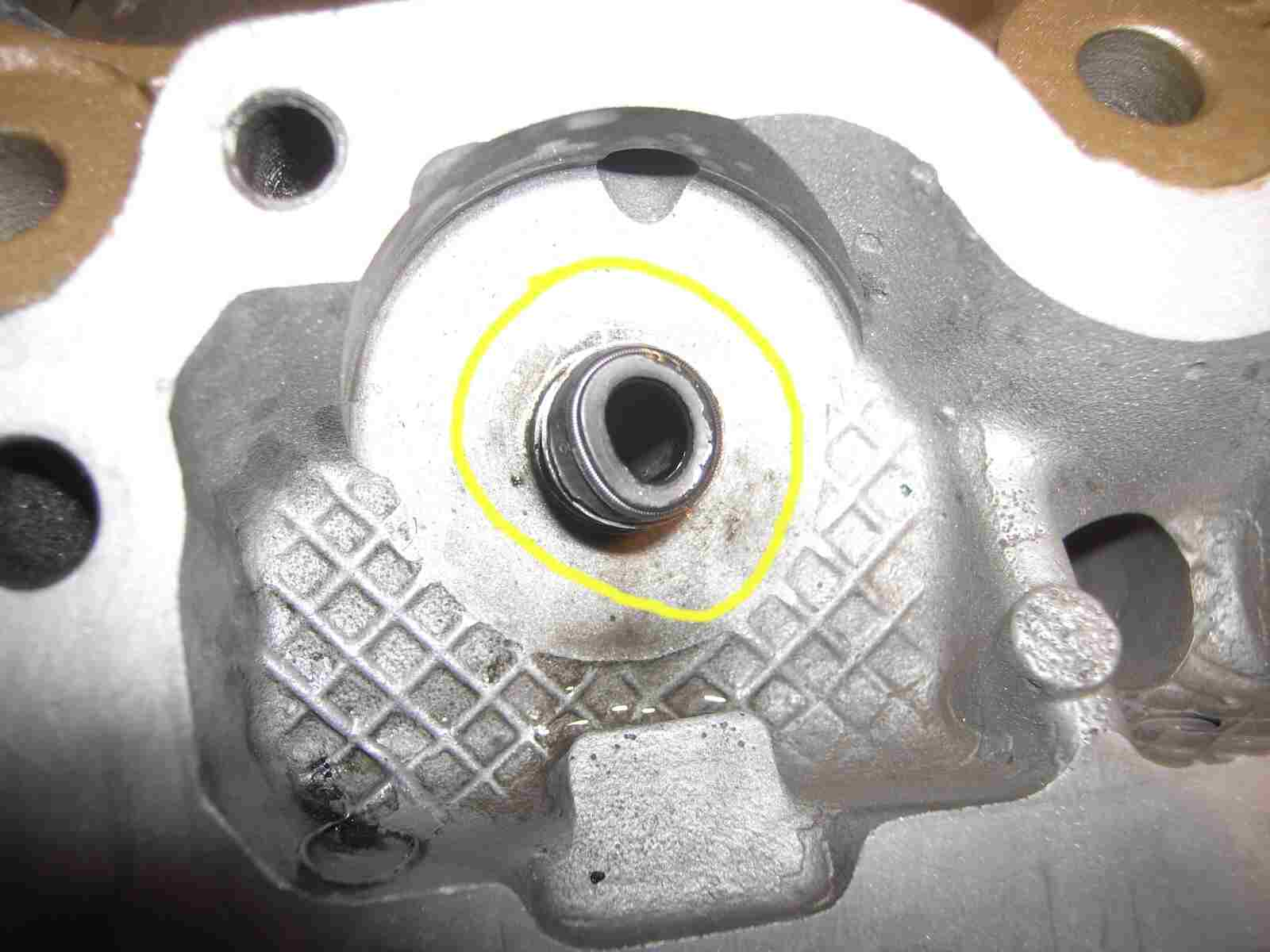 |
|
|
|
Raus damit!
|
|
|
|
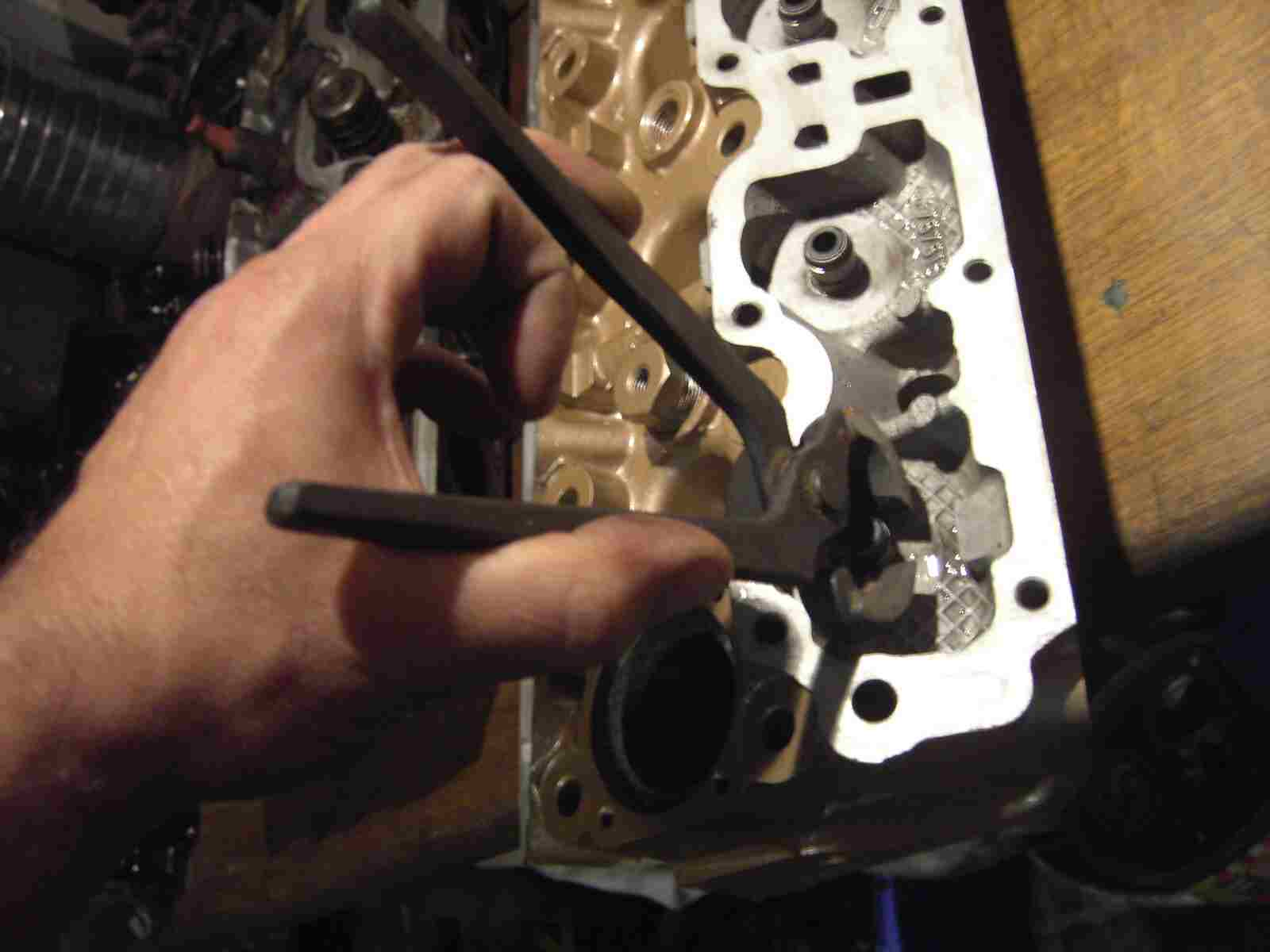 |
|
|
|
Mit einer Beisszange lassen sich alte und defekte Ventilschaftdichtungen leicht entfernen!
|
|
|
|
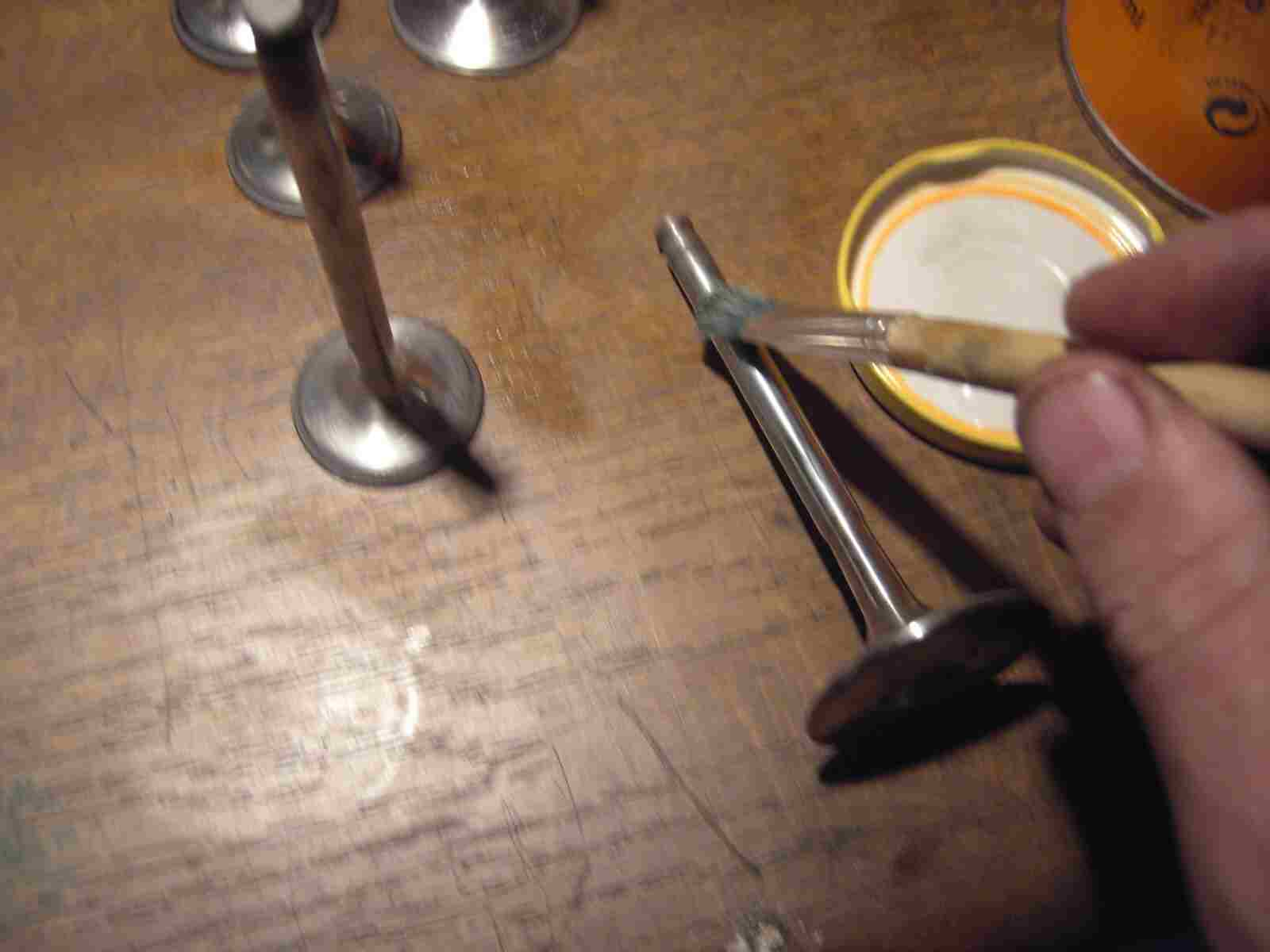 |
|
|
|
Jetzt streiche ich den Ventilschaft mit dem Feinmechanikeröl ein!
|
|
|
|
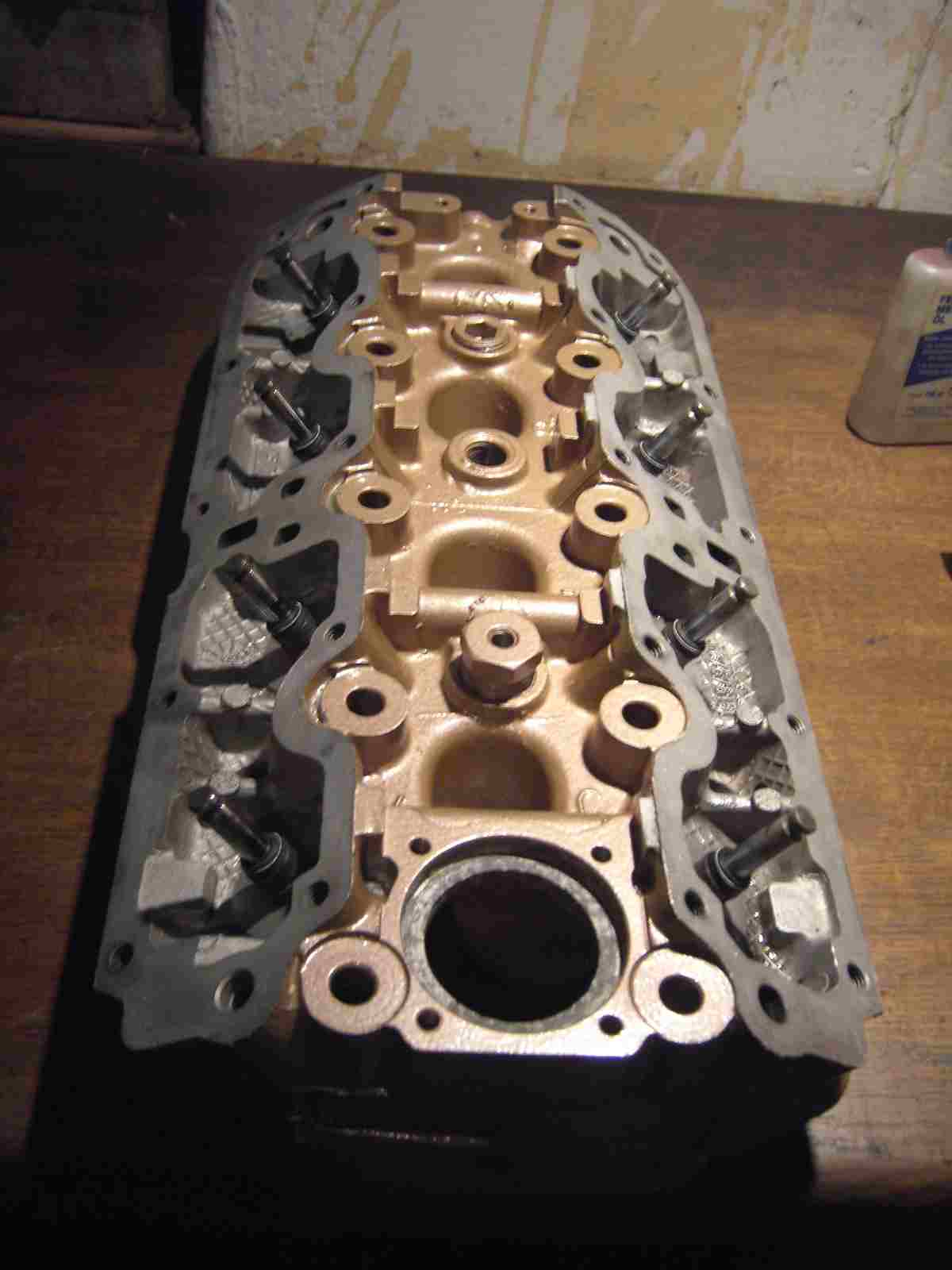 |
|
|
|
Gut, alle Ventilführungen montiert und alle Ventile in den Zylinderkopf eingefügt!
|
|
|
|
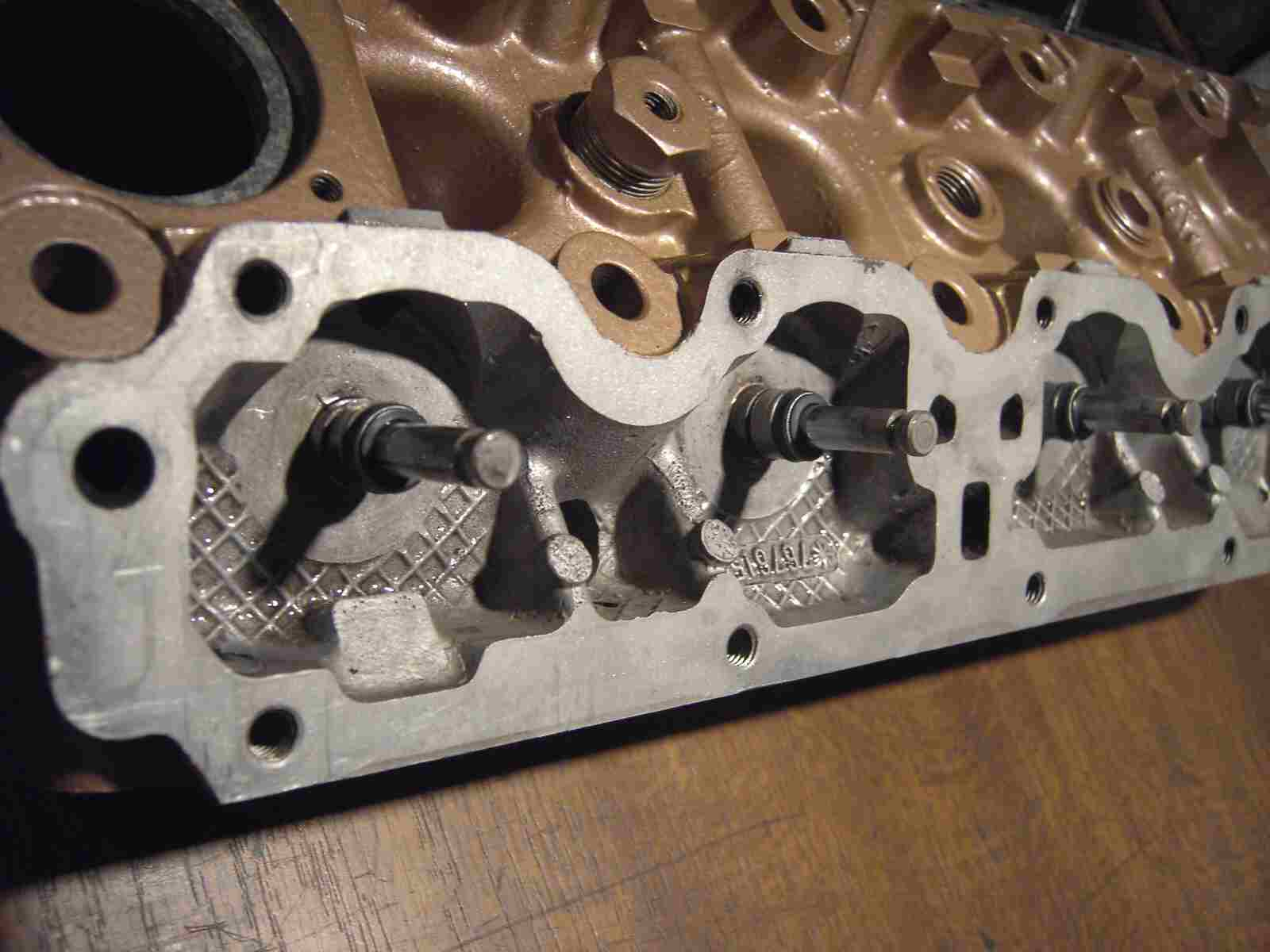 |
|
|
|
So sieht das ganz gut aus, zum Zusammenbau!
|
|
|
|
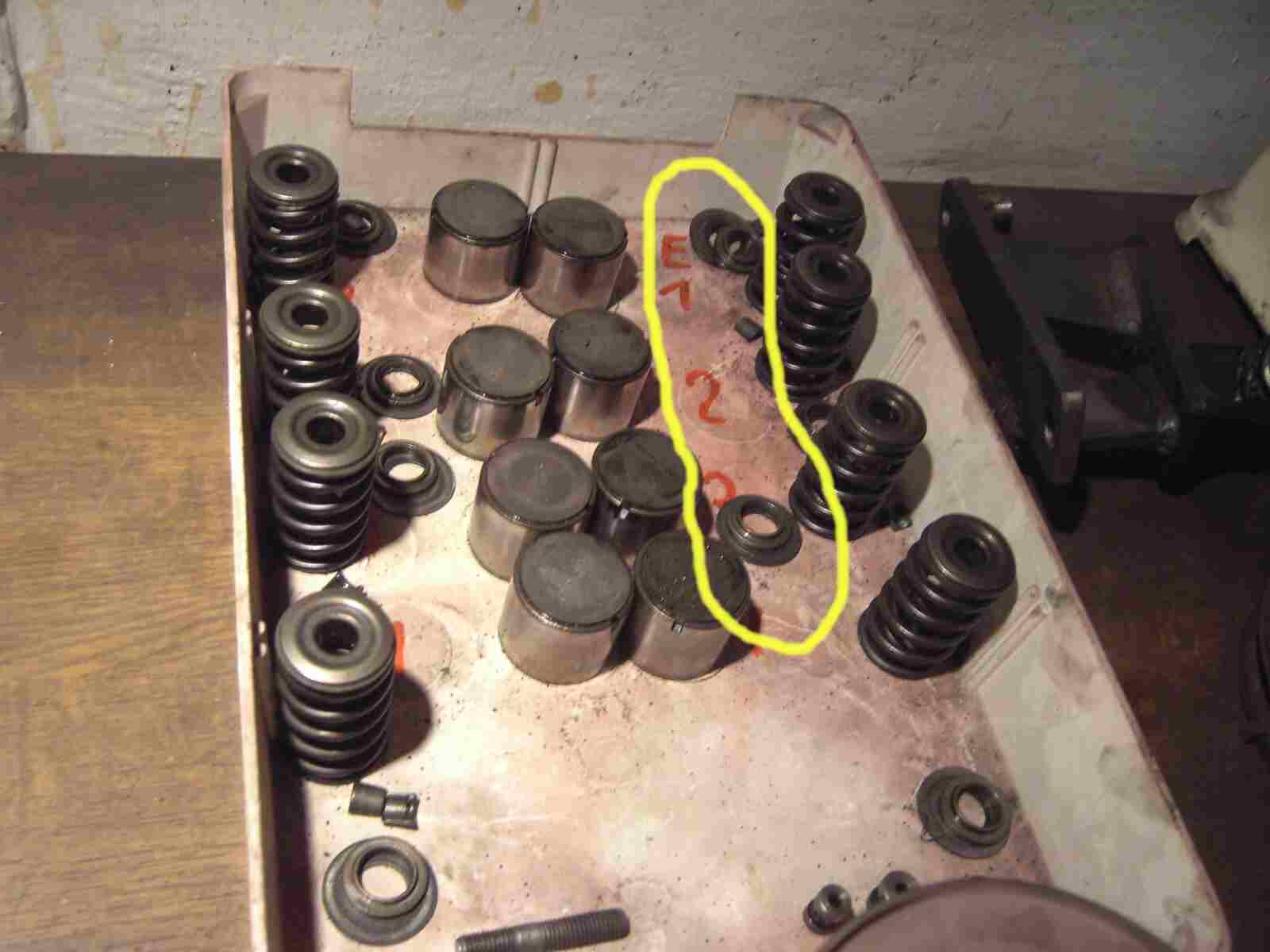 |
|
|
|
Bei der Demontage des Ventiltriebes habe ich mir, in meinen Kasten, die Position der Federn, Tellern und Tassenstössel markiert und so baue ich diese auch wieder zusammen.
|
|
|
|
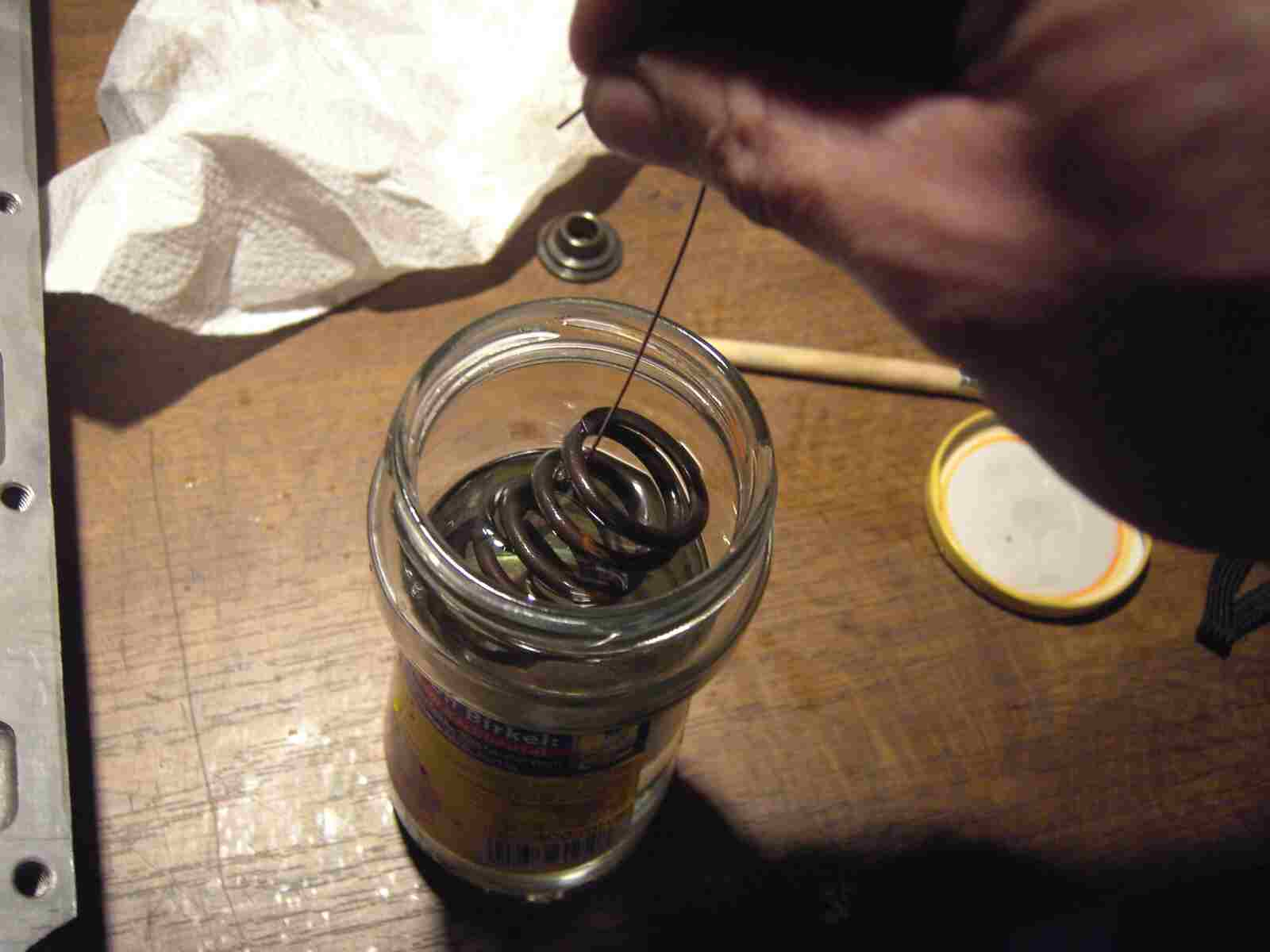 |
|
|
|
Bevor ich den Ventiltrieb montiere, tauche ich die Federn noch in Petroleum ein. Somit werde diese nochmals gereinigt und mit einem Schmierfilm versehen.
|
|
|
|
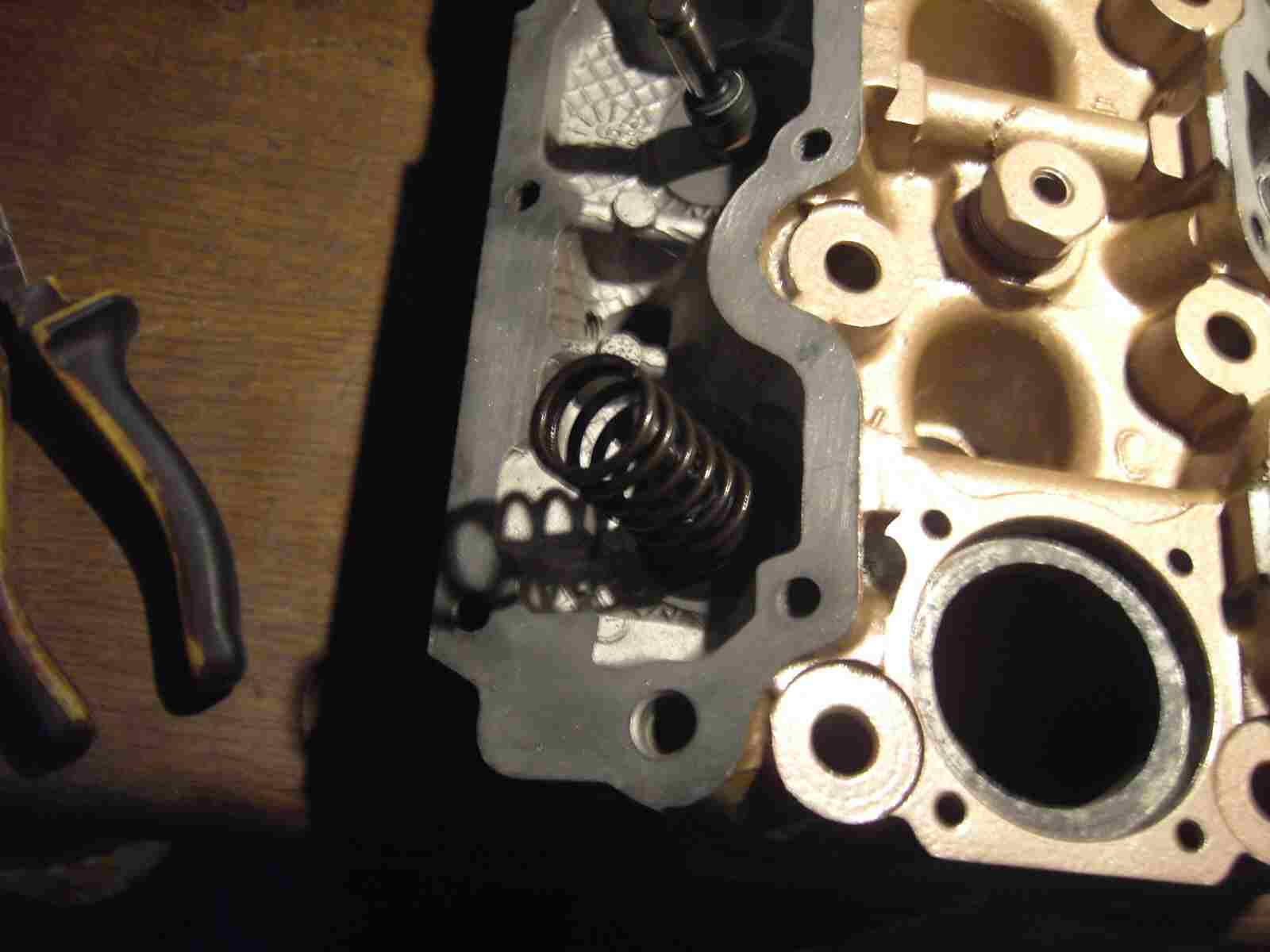 |
|
|
|
Egal, ob es ein Turbomotor oder ein Betamotor ist! Als erstes werden zwei Unterlegscheiben um das Ventil gelegt (Auflage für die kleine und große Feder) und dann die beiden Ventilfedern!
|
|
|
|
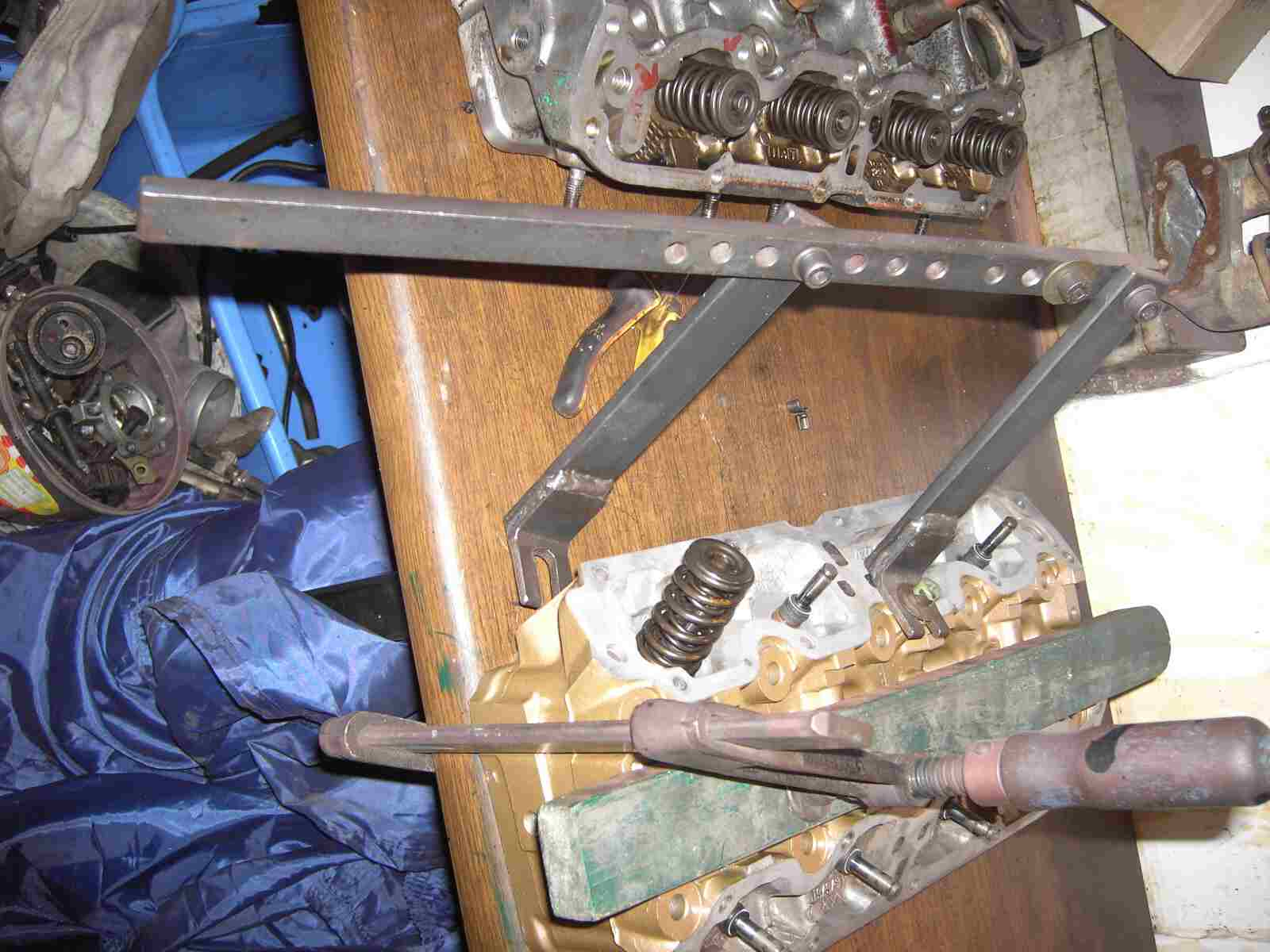 |
|
|
|
Nun müßt Ihr etwas basteln können! Ihr benötigt ein Ventildrückwerkzeug! Ich habe eins selbst gebaut, wie Ihr sehen könnt! Ein Stück Flacheisen mit mehreren Löchern zum Verstellen und zwei Armen mit angeschweißten Winkeleisen. In diese Winkeleisen habe ich Langlöcher eingefeilt.
|
|
|
|
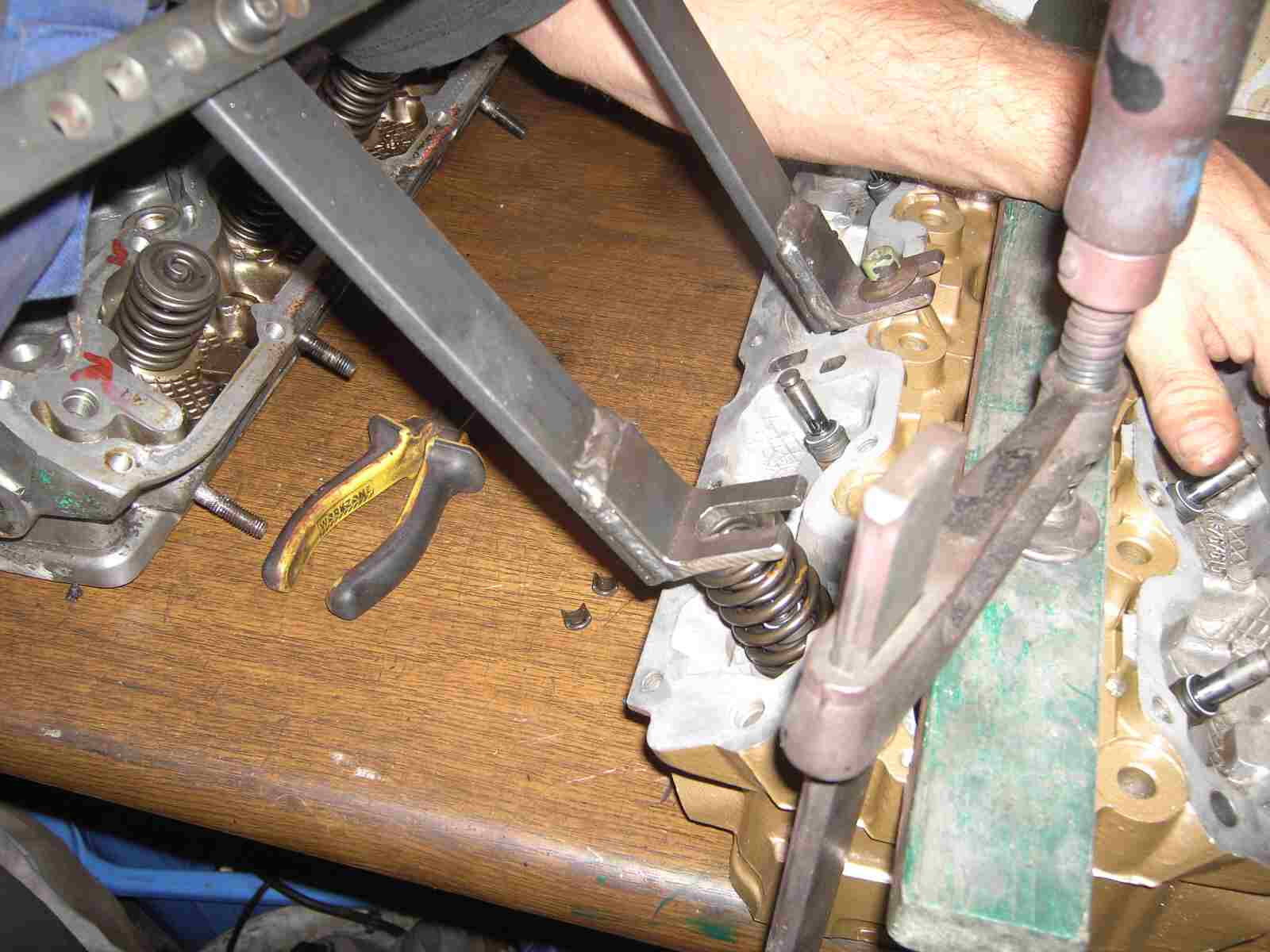 |
|
|
|
Das Spezialwerkzeug wird mit dem hinteren Arm an den Zylinderkopf geschraubt und zwar an dem M8 Gewinde des Nockenwellenkastens. Der zweite Arm wird mit den vielen Löchern des oberen Tragarmes so weit verstellt, bis dieser in etwa über dem Ventil steht.
|
|
|
|
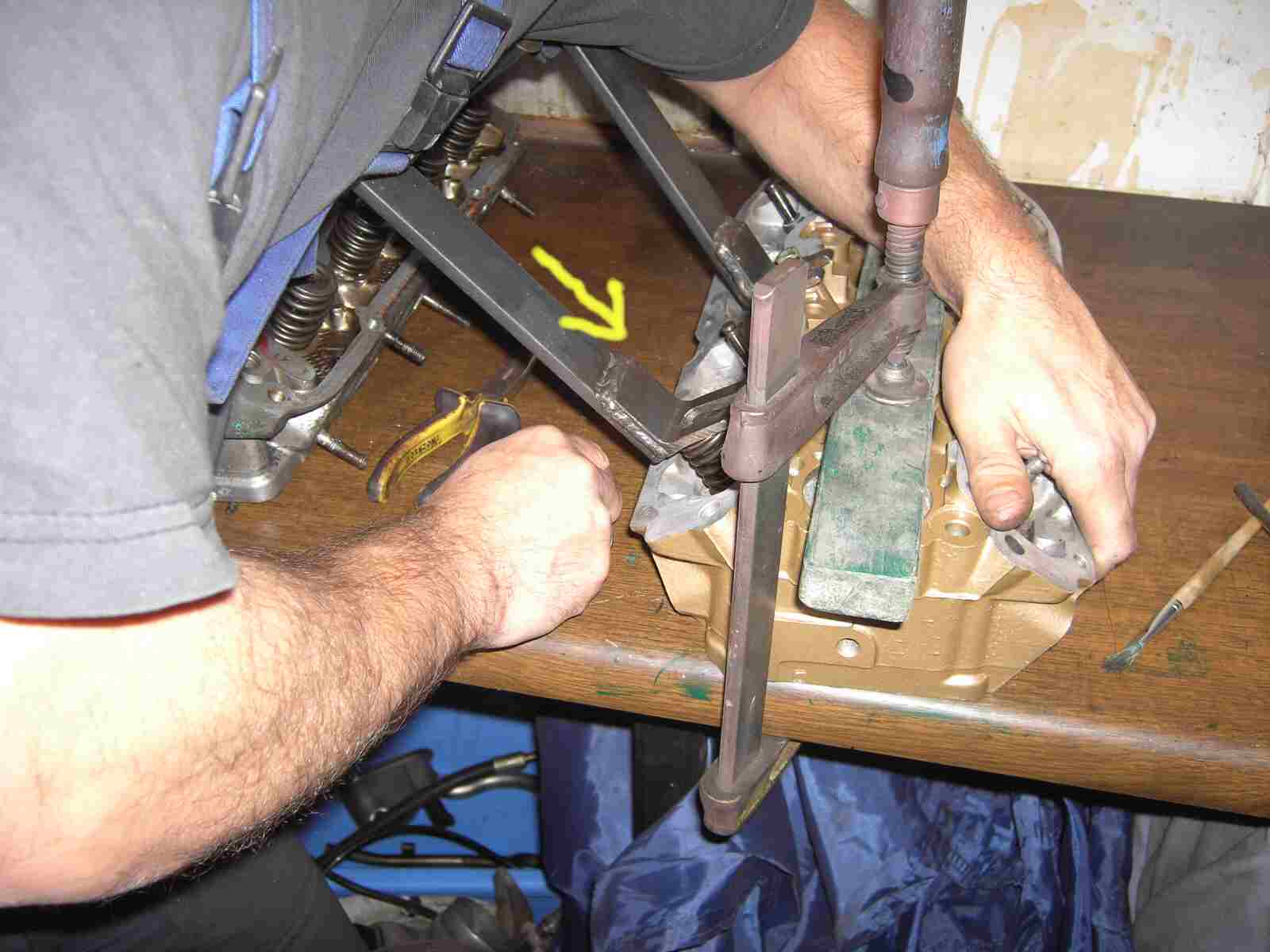 |
|
|
|
Mit meinem Oberkörper kann ich das Ventil mit dem Werkzeug nach unten drücken und mit einer Hand halte ich den Zylinderkopf fest. Mit der anderen Hand fädle ich die beiden Sicherungskeile ein.
|
|
|
|
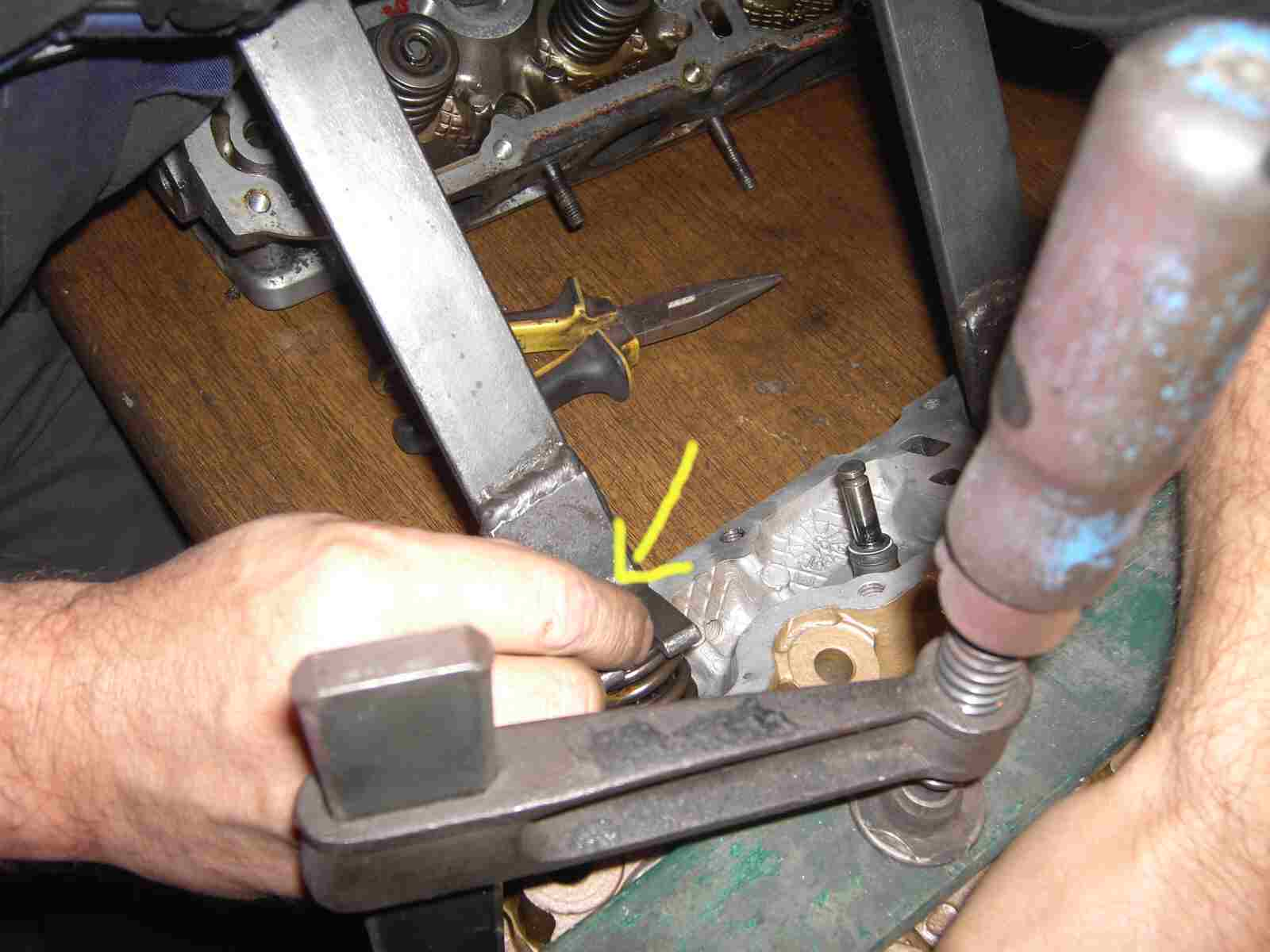 |
|
|
|
Durch das Langloch im Winkel meine Werkzeuges kann ich die Ventilfeder drücken und habe gleichzeitig genügend Platz um die Sicherungskeile einfügen zu können. Ist schon etwas Geschick notwendig, aber es funktioniert!
|
|
|
|
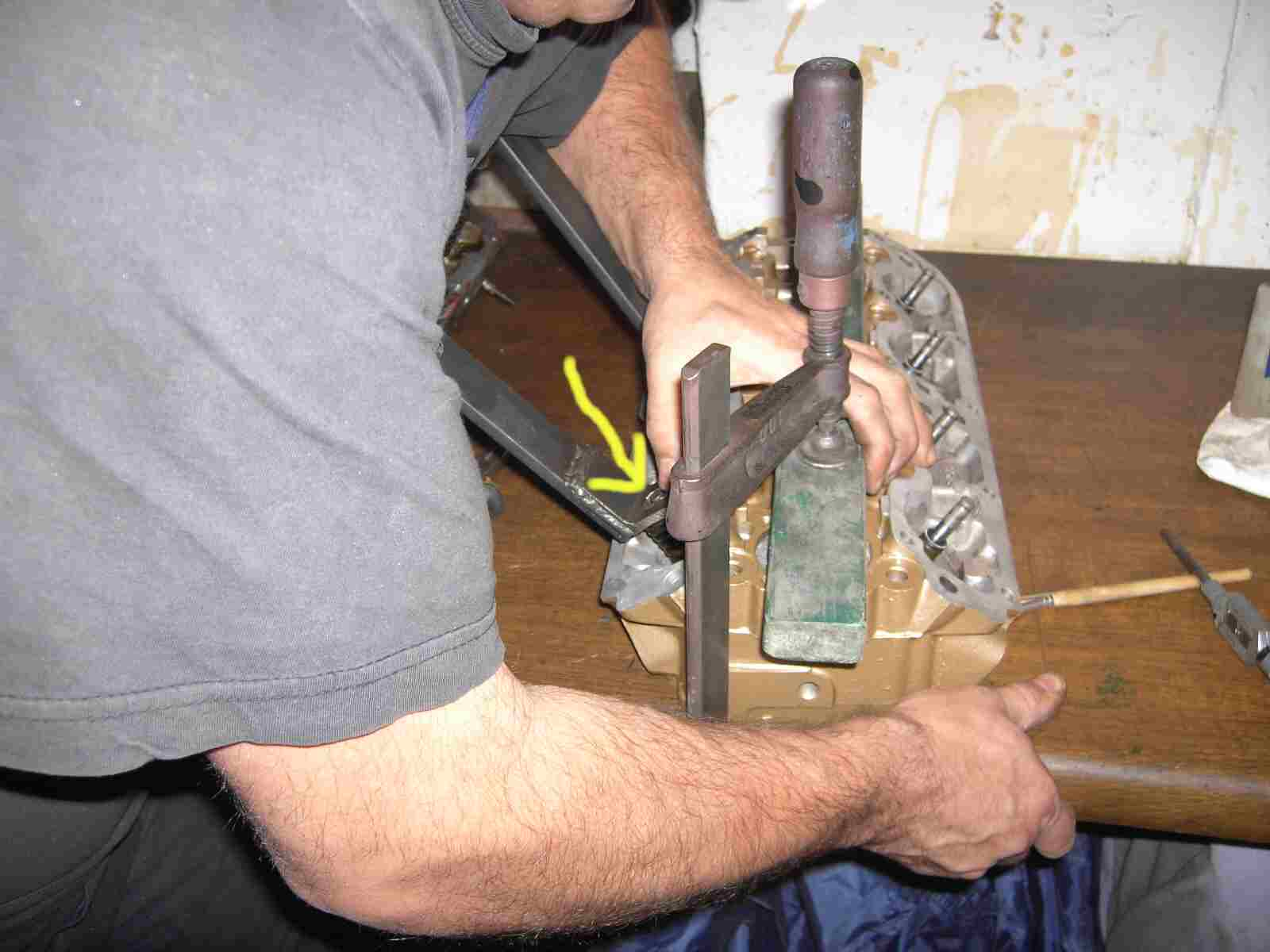 |
|
|
|
Wenn Ihr noch eine Stück Holz über den Zylinderkopf legt, könnt Ihr diesen mit einer Schraubzwinge zusätzlich fixieren.
|
|
|
|
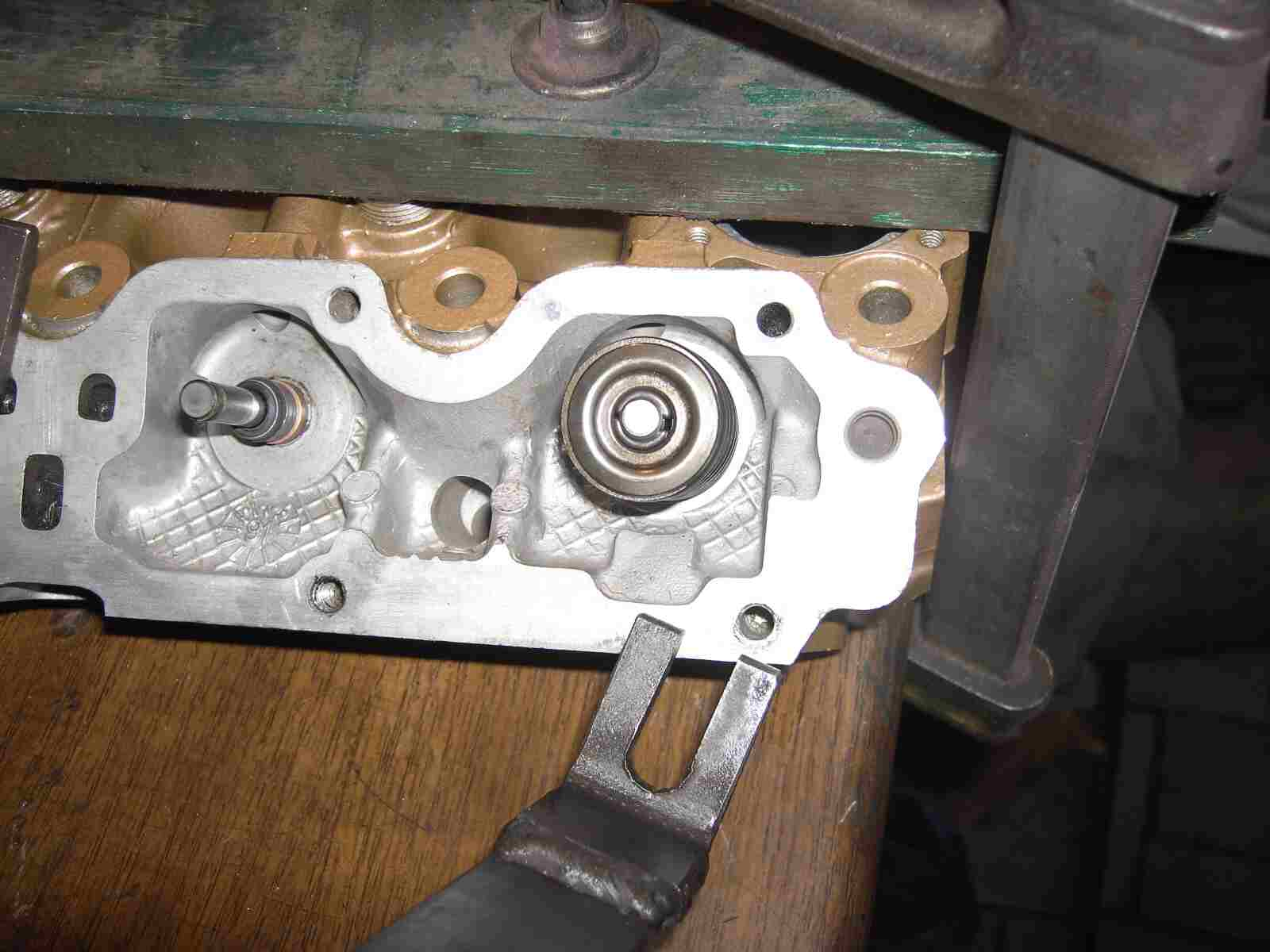 |
|
|
|
Und so sind die Sicherungskeile richtig montiert!
|
|
|
|
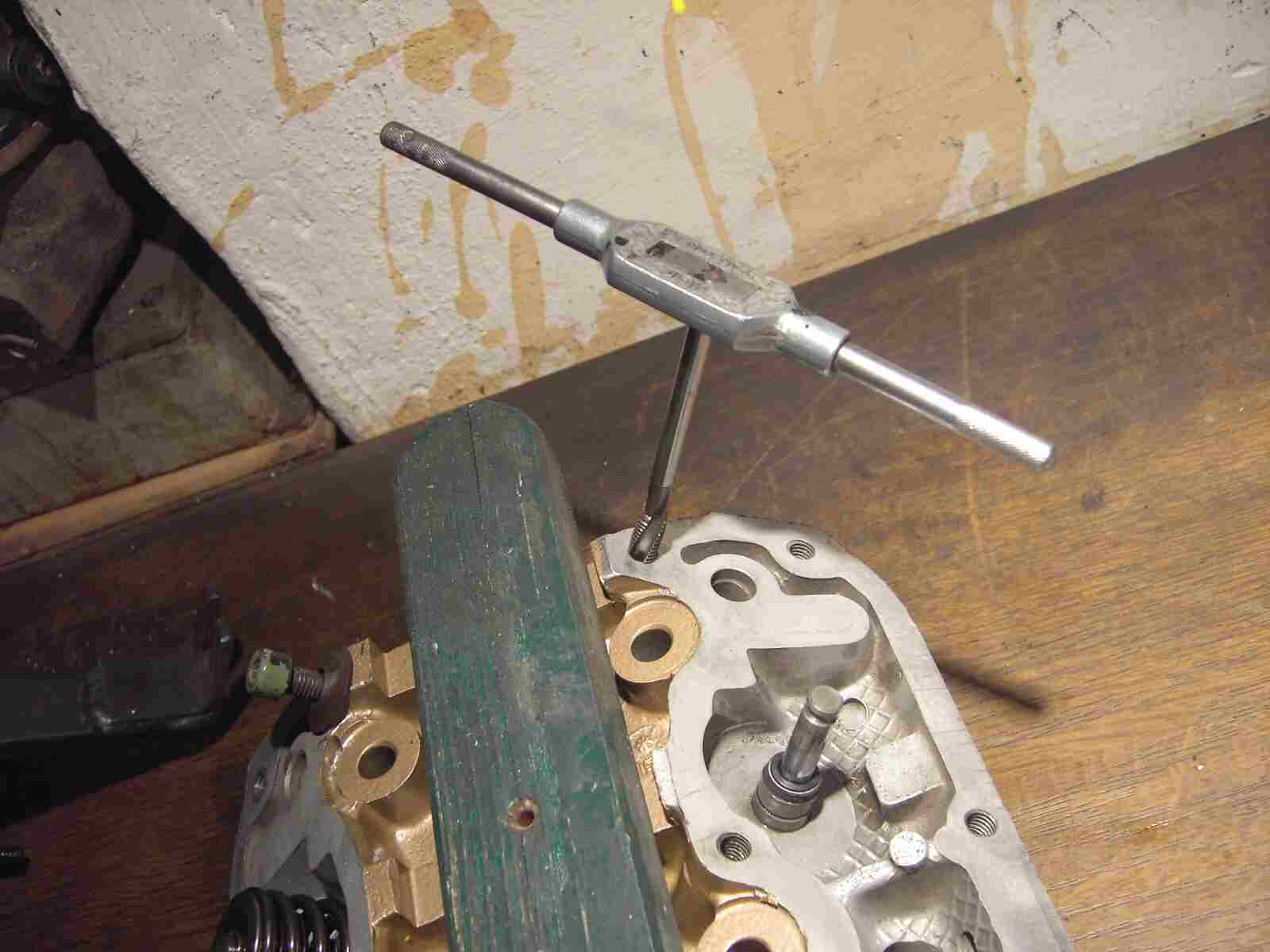 |
|
|
|
Und so montiert Ihr den Ventiltrieb nach und nach zusammen! Wenn Ihr schon dabei seit, ist es auch ein Vorteil, wenn Ihr alle M8 Gewinde von Eurem Zylinderkopf mit dem Gewindebohrer nachschneidet und nicht nur die vom Nockenwellenkasten, sondern auch vom Auspuffkrümmer und von der Ansaugbrücke! Das kann Euch später beim Einbau so manche Nerverei ersparen. Sollte ein Gewinde sogar defekt sein, könnt Ihr dies gleich mit HELICOIL reparieren. Später im Zusammenbau nur sehr schlecht!
|
|
|
|
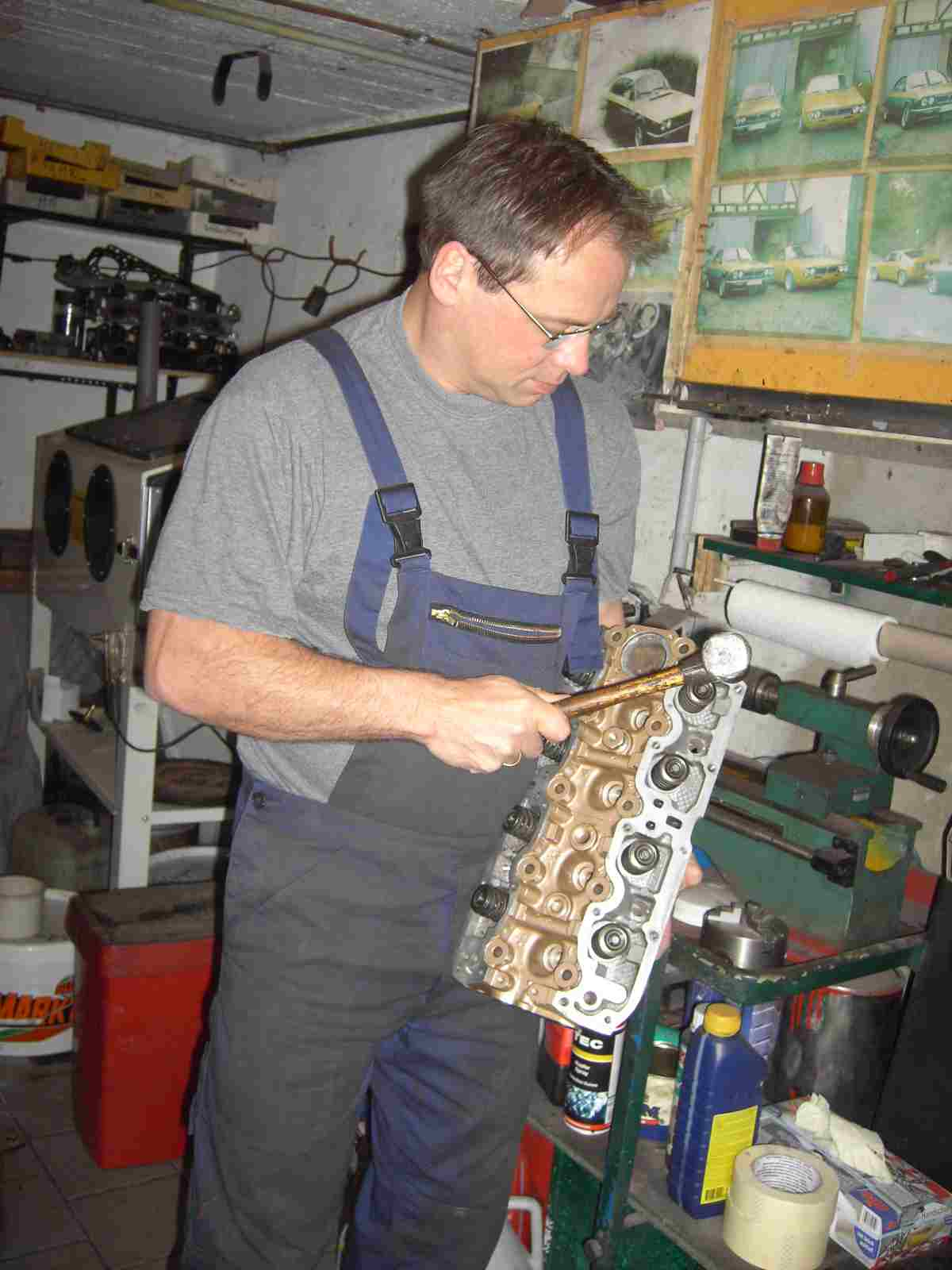 |
|
|
|
Wenn der Ventiltrieb montiert ist, dann wird ein Test durchgeführt. Mit einem Kunststoffhammer klopft Ihr alle Ventile nacheinander ab. Dadurch werden diese kurz bewegt und Ihr könnt sicher sein, das die Sicherungskeile richtig eingelegt sind. Sind diese nicht richtig eingelegt, fliegt Euch, in diesem Test, die Federn und das Ventil um die Ohren. Passiert dies im eingebauten Zustand, dann habt Ihr einen kapitalen Motorschaden!
|
|
|
|
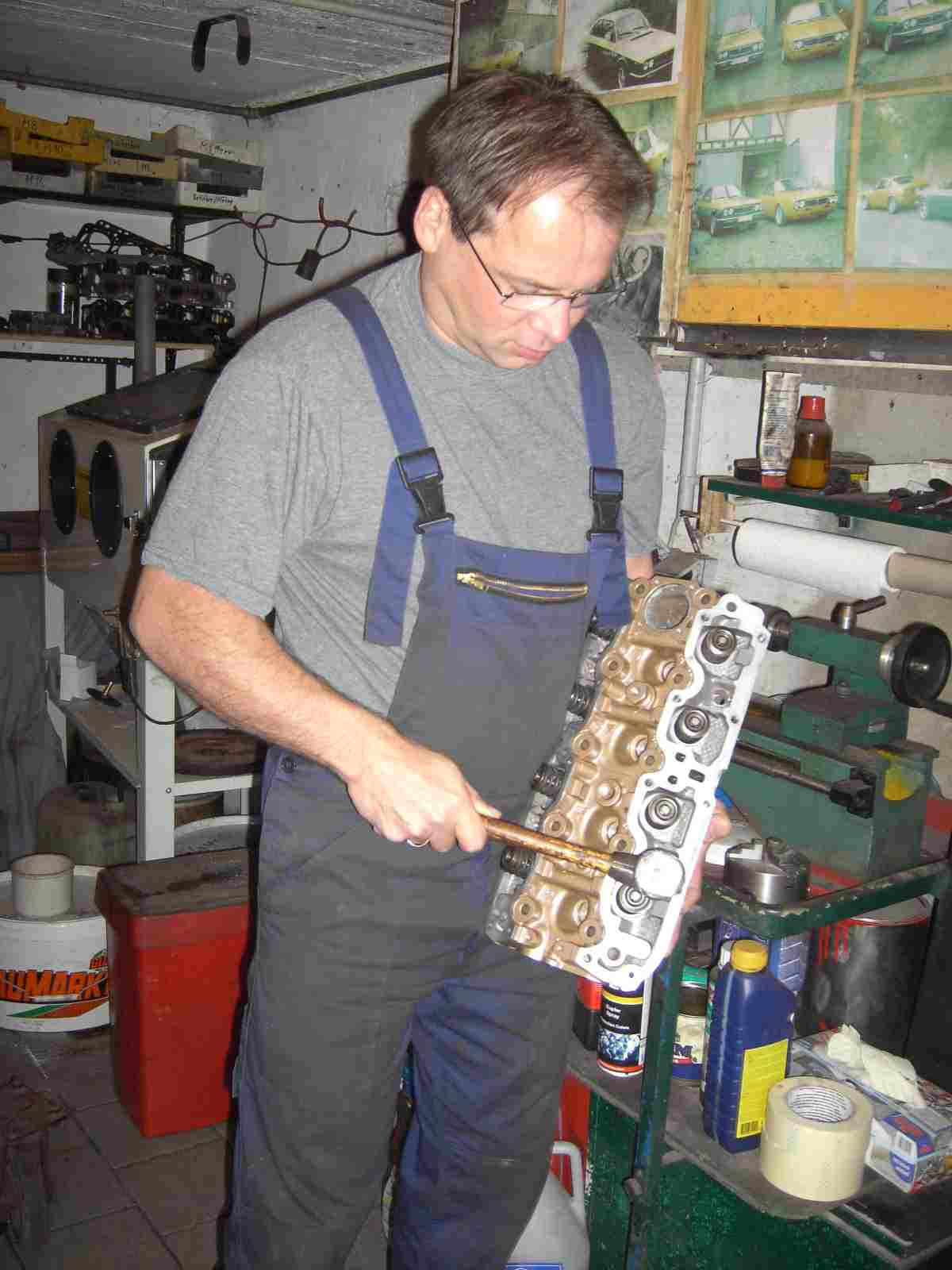 |
|
|
|
Also klopft alle Ventile richtig durch, aber nur mit leichten Schlägen!
|
|
|
|
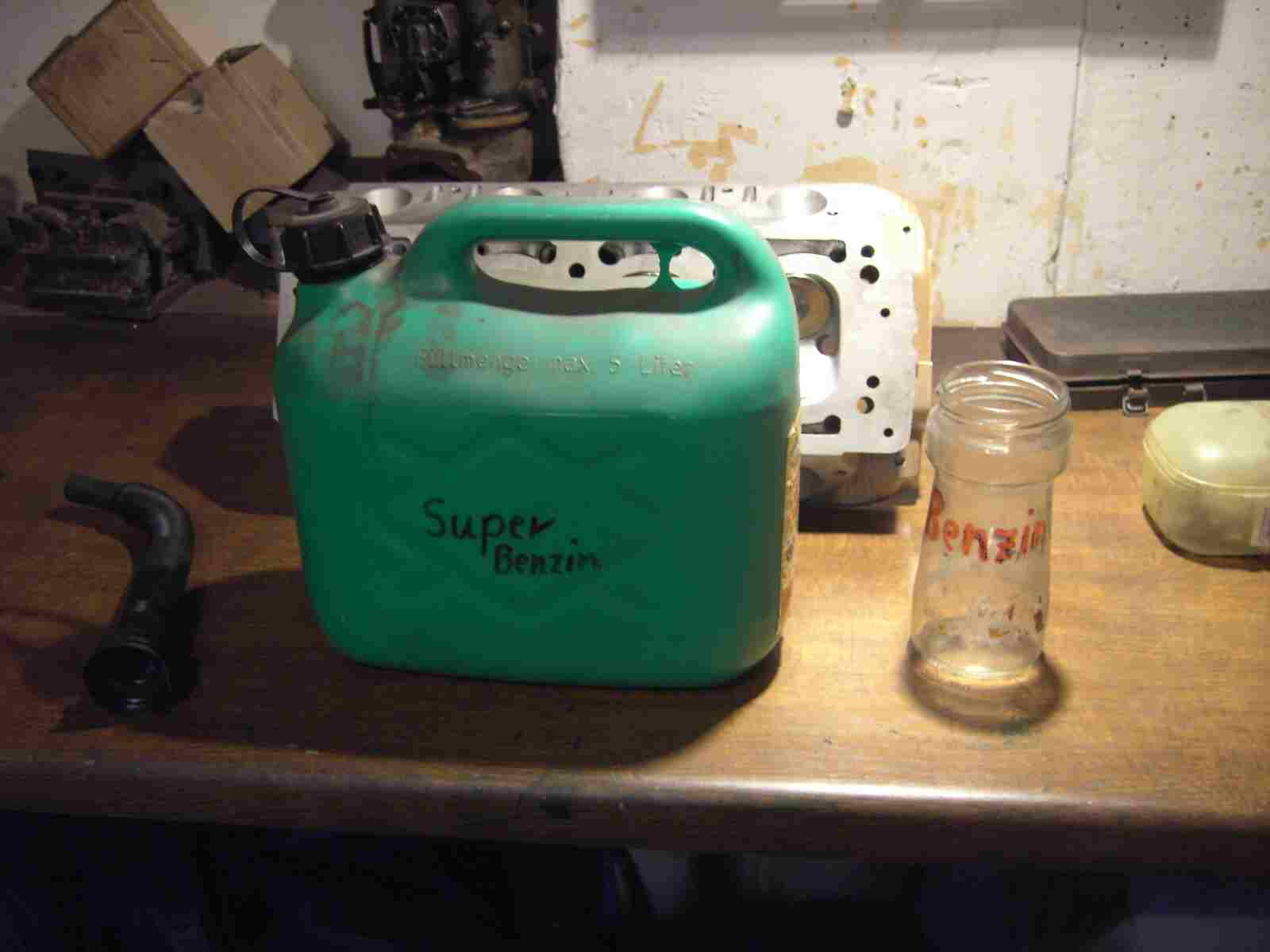 |
|
|
|
Für die Dichtheitsprüfung benötigt Ihr SUPER Benzin! Nein, natürlich nicht unbedingt Super Benzin, normales Benzin reicht.
|
|
|
|
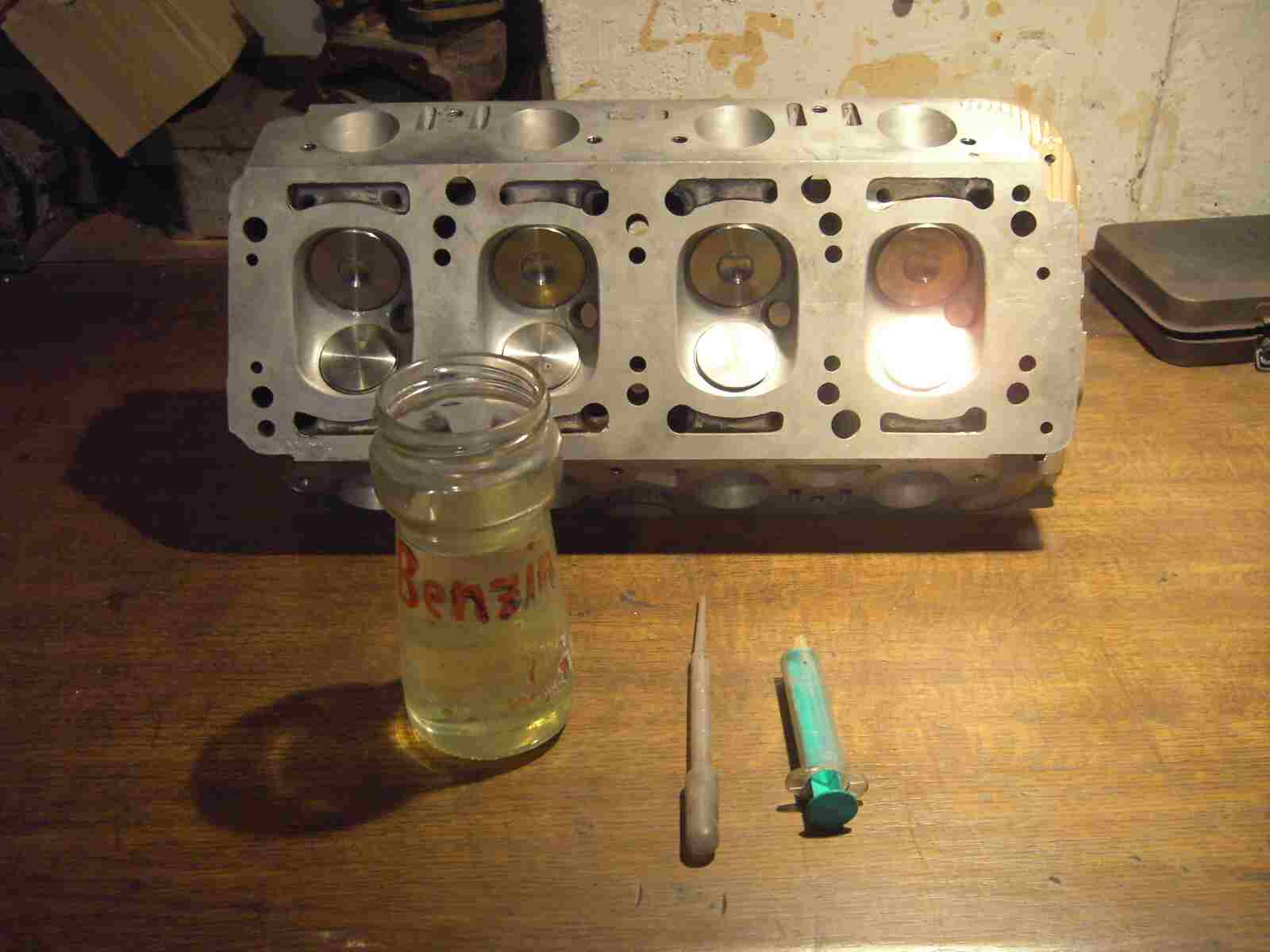 |
|
|
|
Zum Dosieren wäre eine Spritze oder Pipette auch nicht schlecht!
|
|
|
|
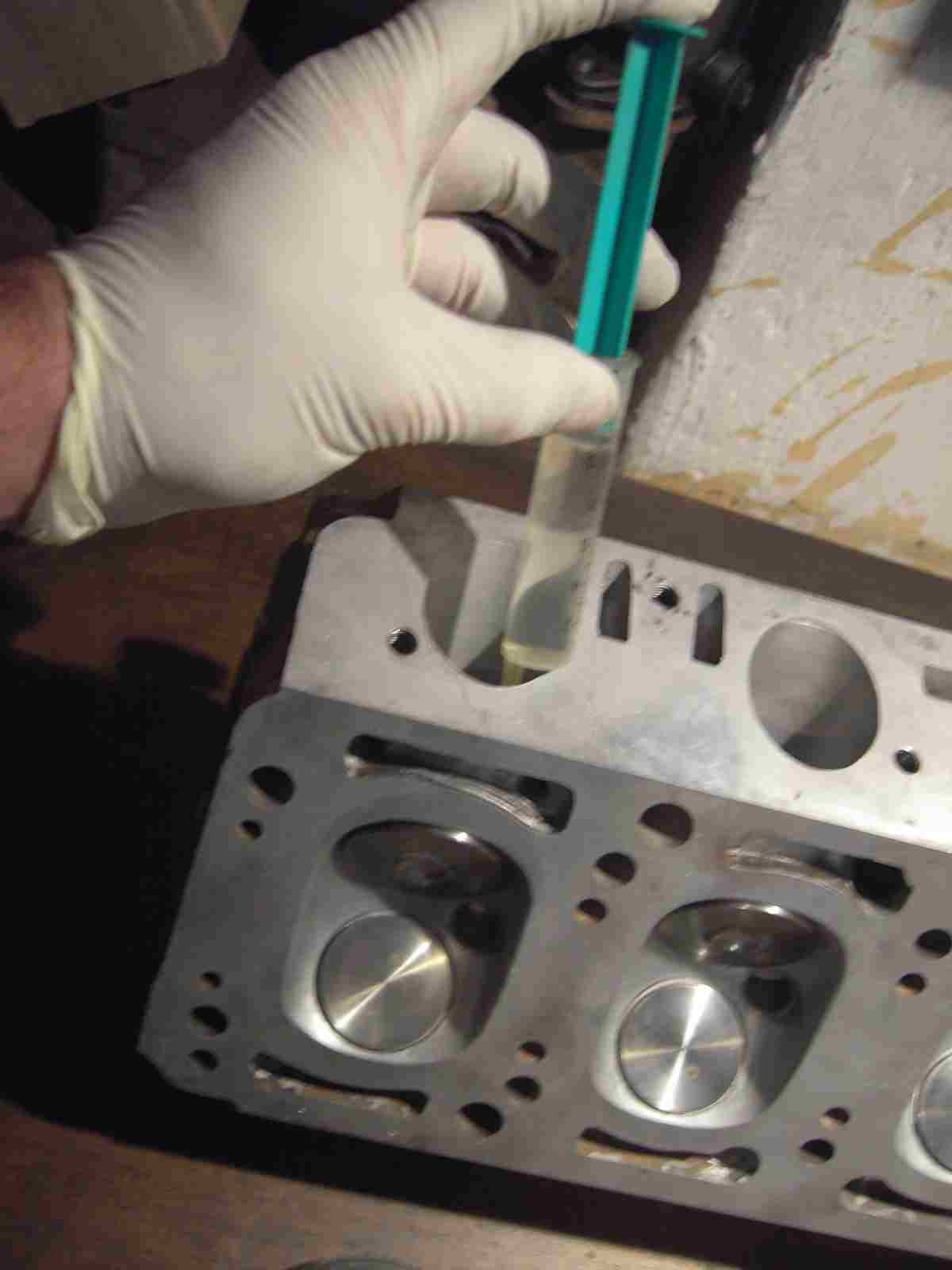 |
|
|
|
Ich überprüfe als erstes die Einlassventile und dafür fülle ich den Einlass mit Benzin auf!
|
|
|
|
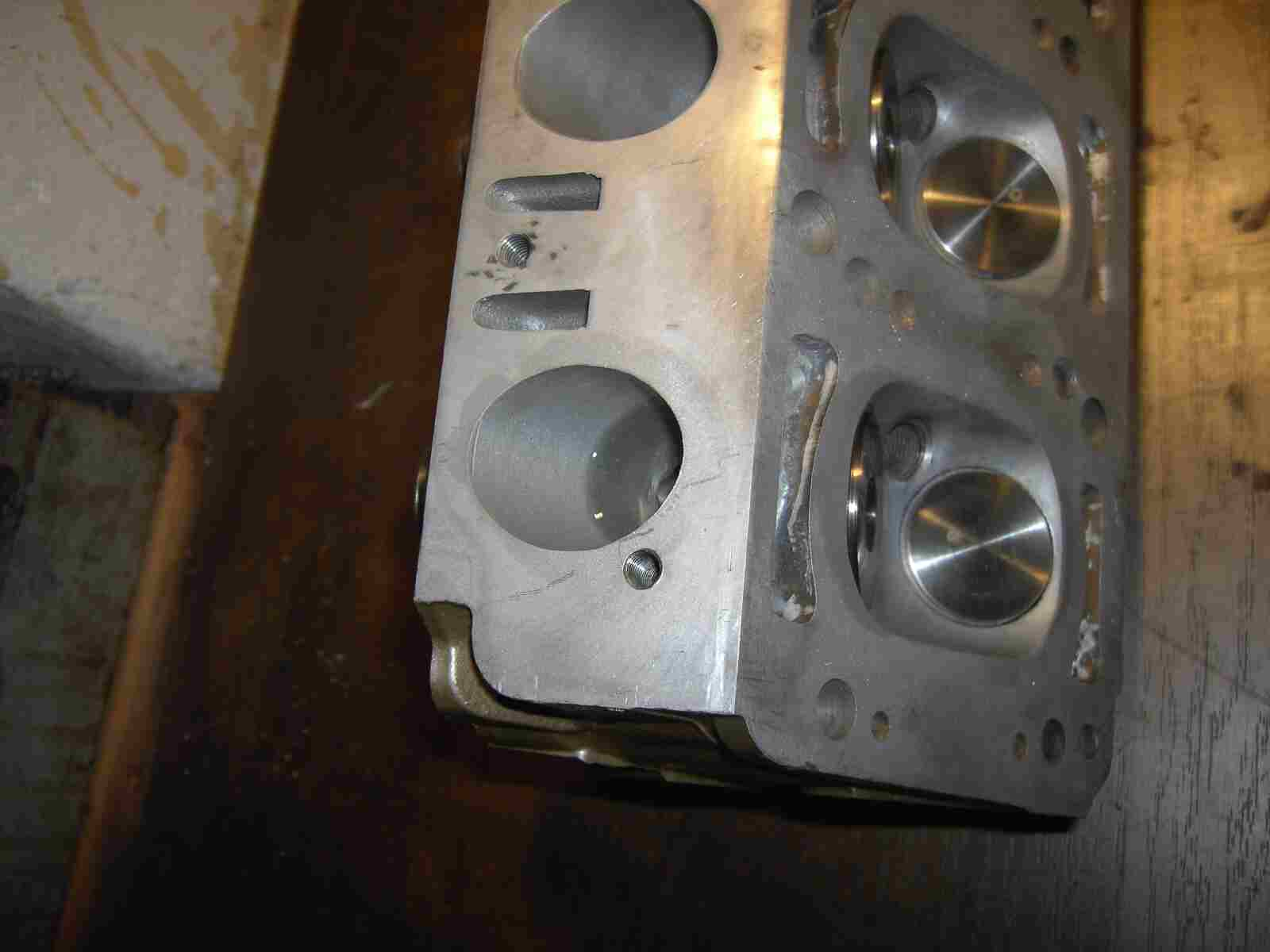 |
|
|
|
So voll reicht!
|
|
|
|
 |
|
|
|
Alle Einlässe sind gefüllt und jetzt?
|
|
|
|
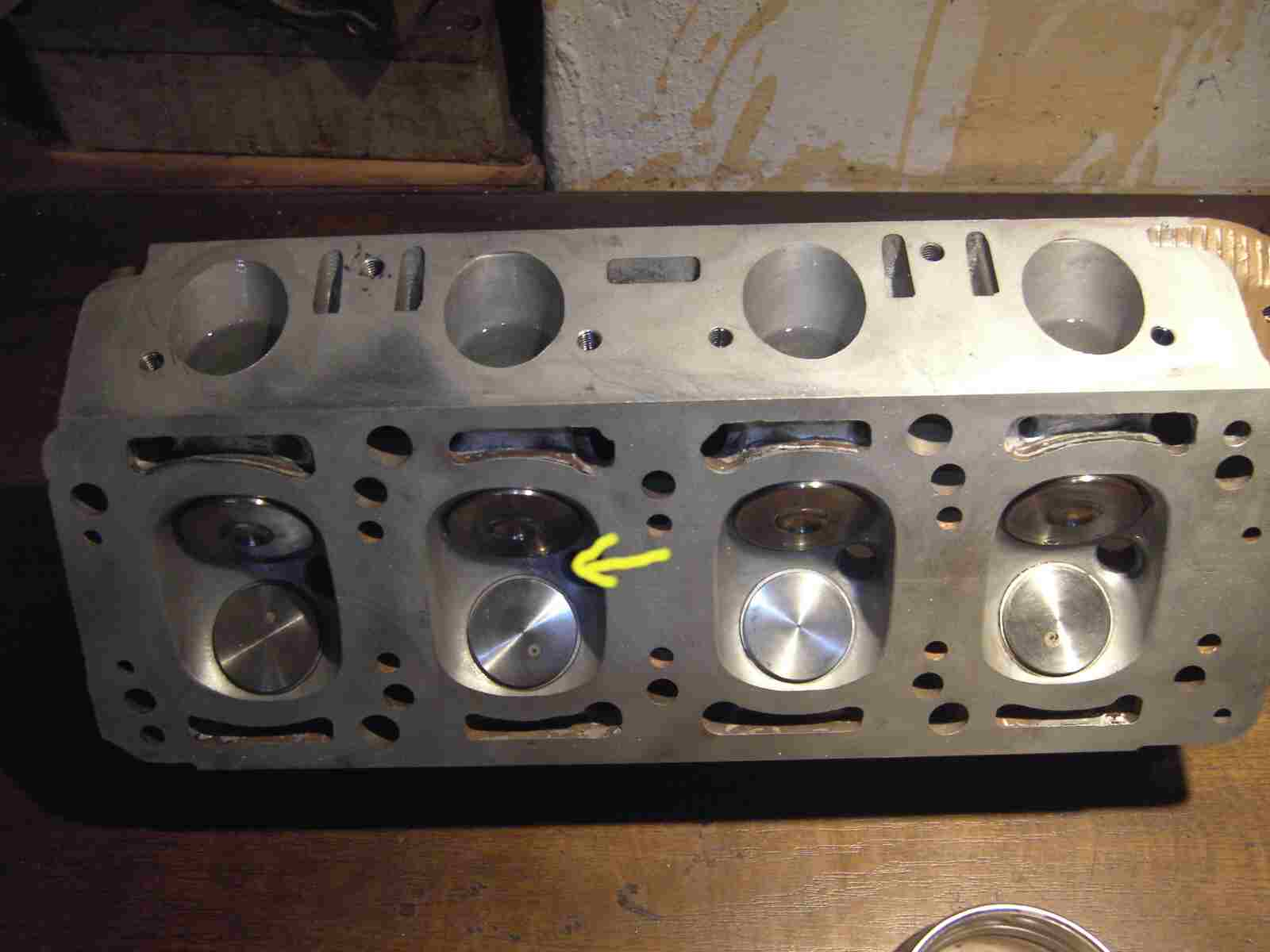 |
|
|
|
Benzin hat einen hohen Dampfdruck, d.h. es bildet Gase an der Luft. Diese gelangen bei undichten Ventilen in den Brennraum und zeigen sich als Niederschlag wieder.
|
|
|
|
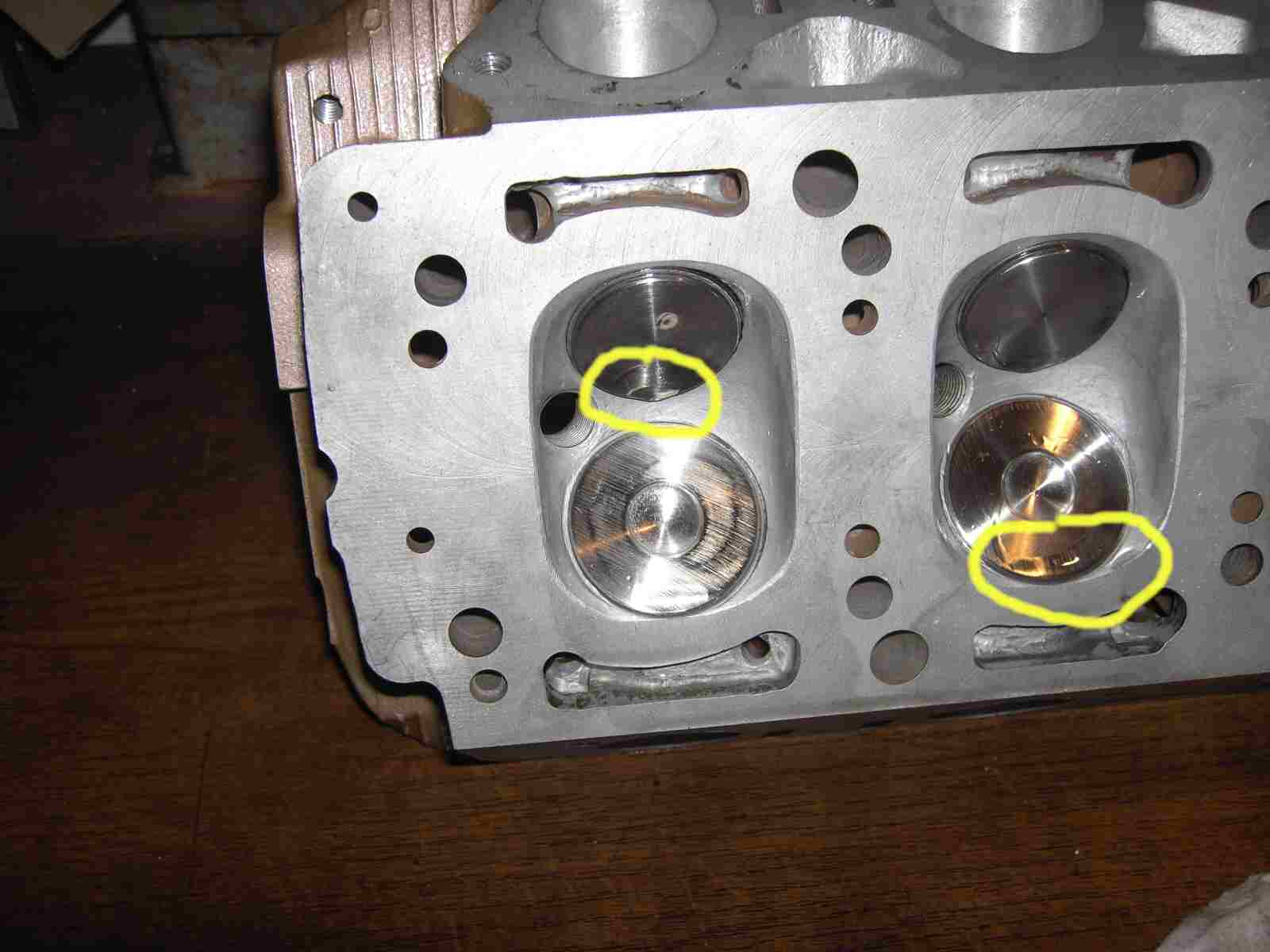 |
|
|
|
Und das könnt Ihr hier genauer sehen! Es bilden sich Tropfen und zwar an den Auslassventilen!
|
|
|
|
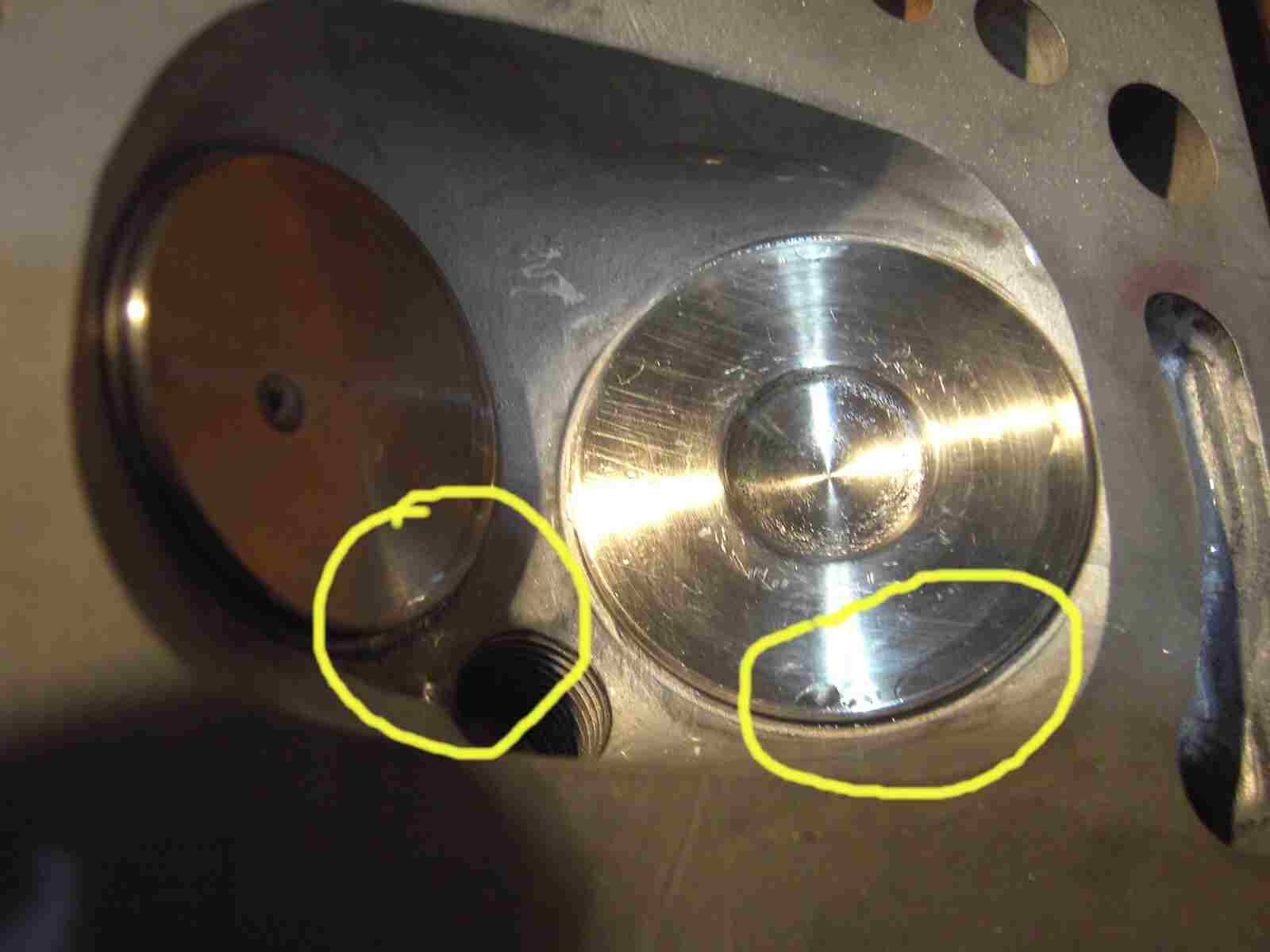 |
|
|
|
Vom Auslassventil lief das Benzin sogar auf das Einlassventil und das ist schlecht, sehr schlecht!
|
|
|
|
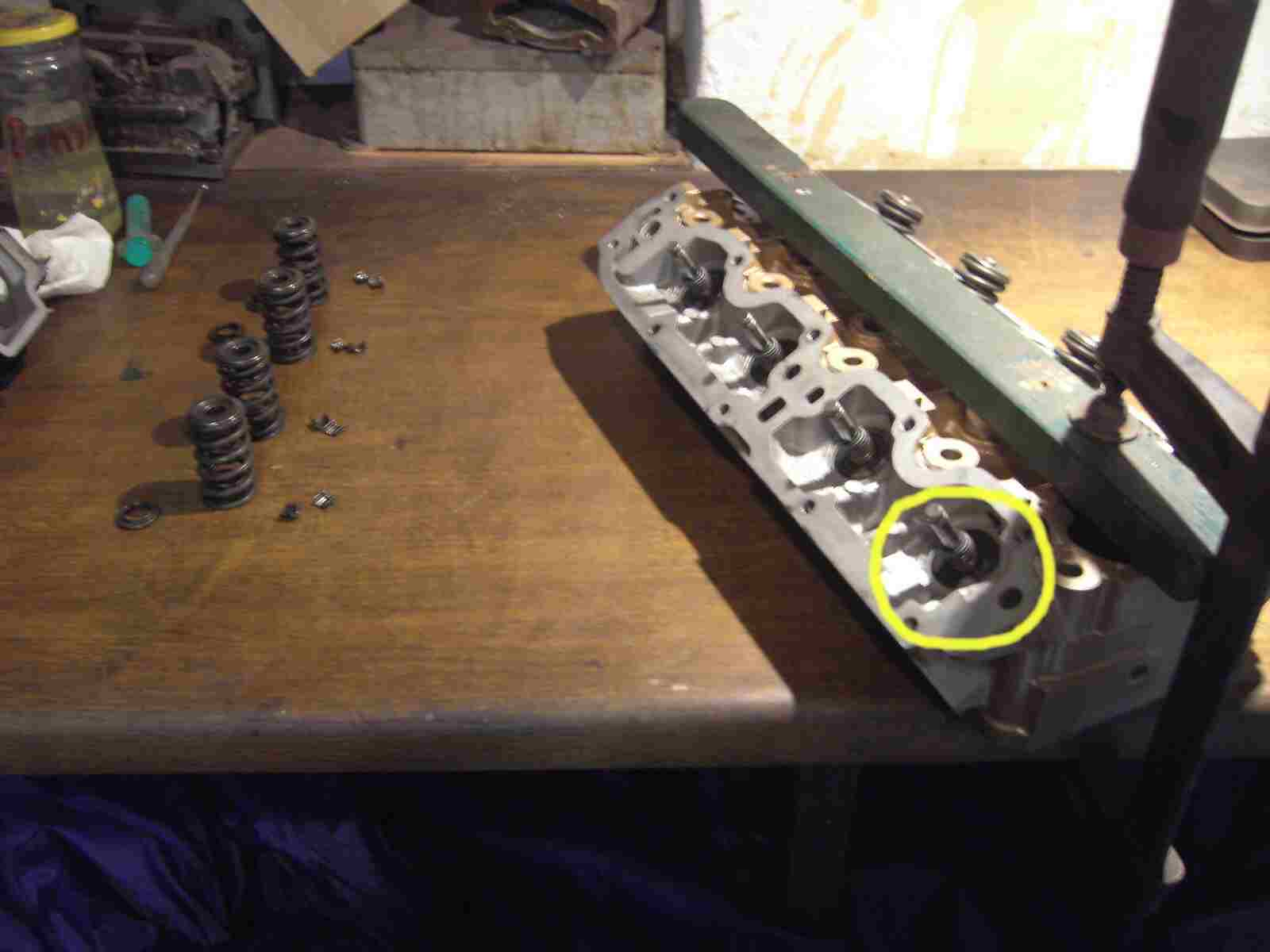 |
|
|
|
Das heißt: Den Ventiltrieb wieder demontieren!
|
|
|
|
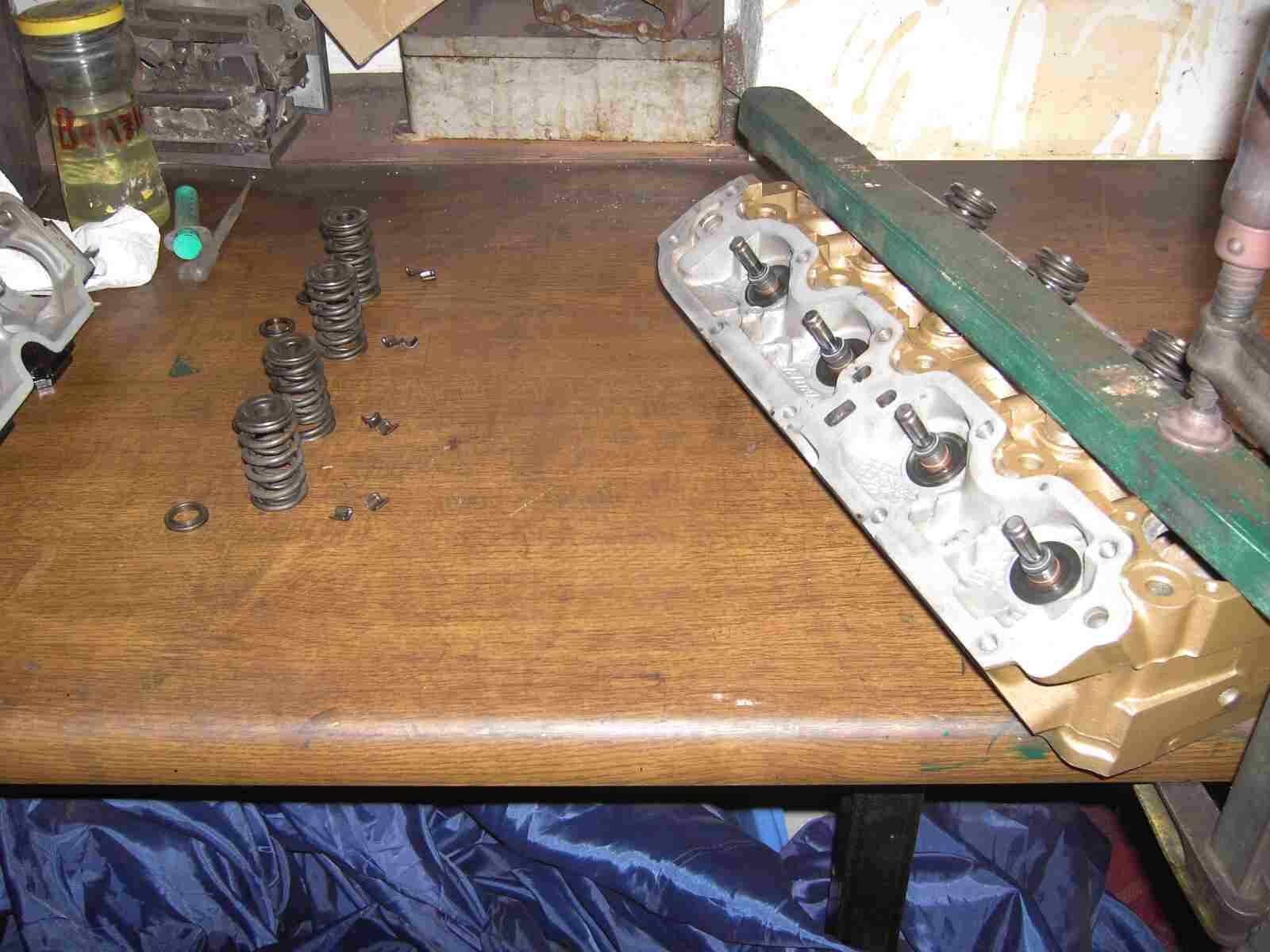 |
|
|
|
Und die Ventile nochmals mit Vorschleifpaste und Nachschleifpaste bearbeiten!
|
|
|
|
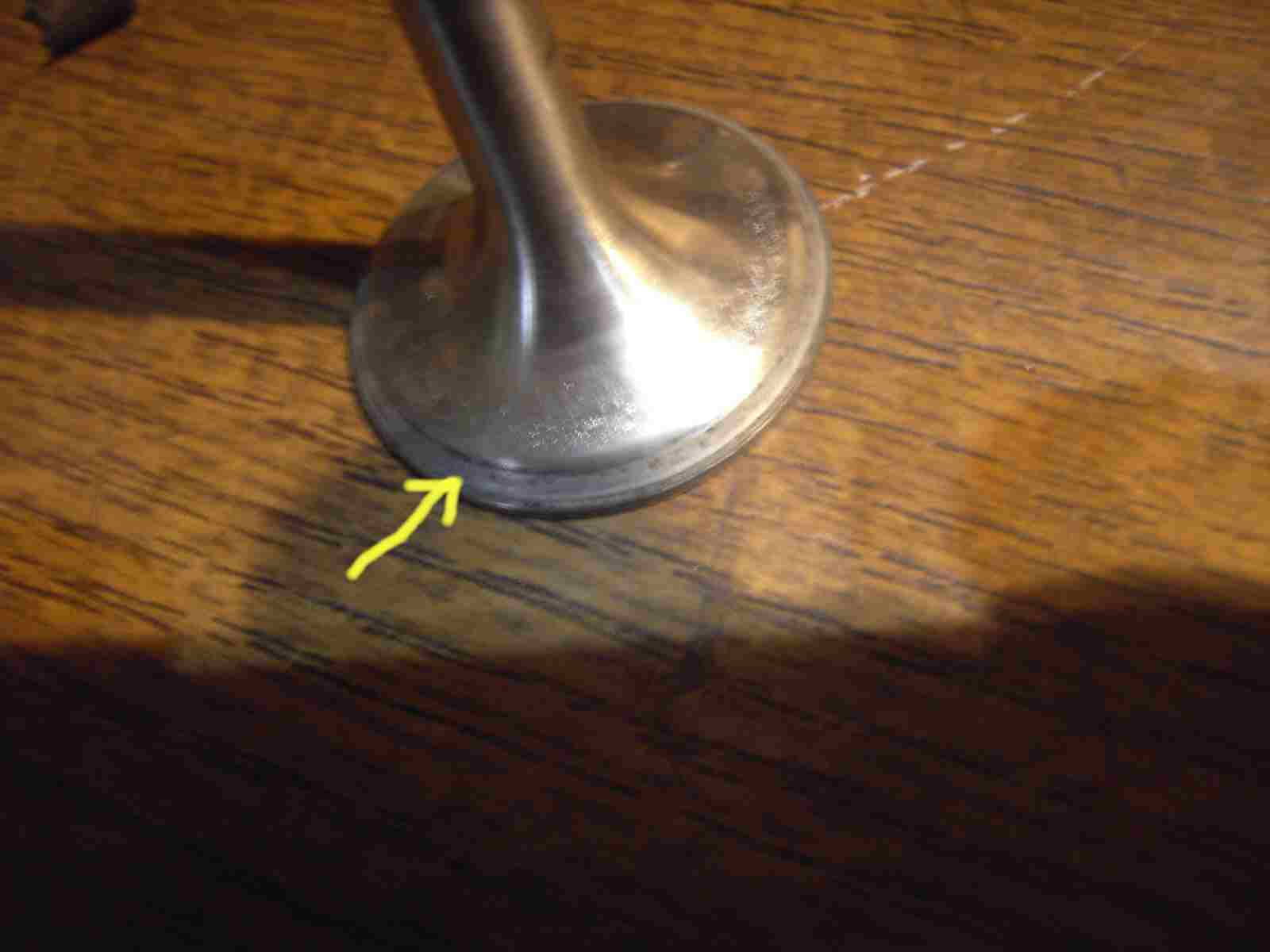 |
|
|
|
Trotz mehrfacher Nachschleiferei, wurden das Auslassventil nicht dicht. Beim Beta Motor würde ich den Ventilsitz etwas nachfräsen. Dieser ist aus Grauguss und ist mit einem HSS Ventilsitzfräser möglich, den ich besitze. Beim Turbomotor sind aber die Ventilsitze gehärtet und können nur mit einem Hartmetall Ventilsitzfräser bearbeitet werden und dieser kostet mit Zubehör 300€ - 500€. Das ist mir doch etwas zu teuer! Am Auslassventil sieht man am Dichtsitz lauter eingebrannte, schwarze Stellen. Diese verursachen die Undichtigkeit!
|
|
|
|
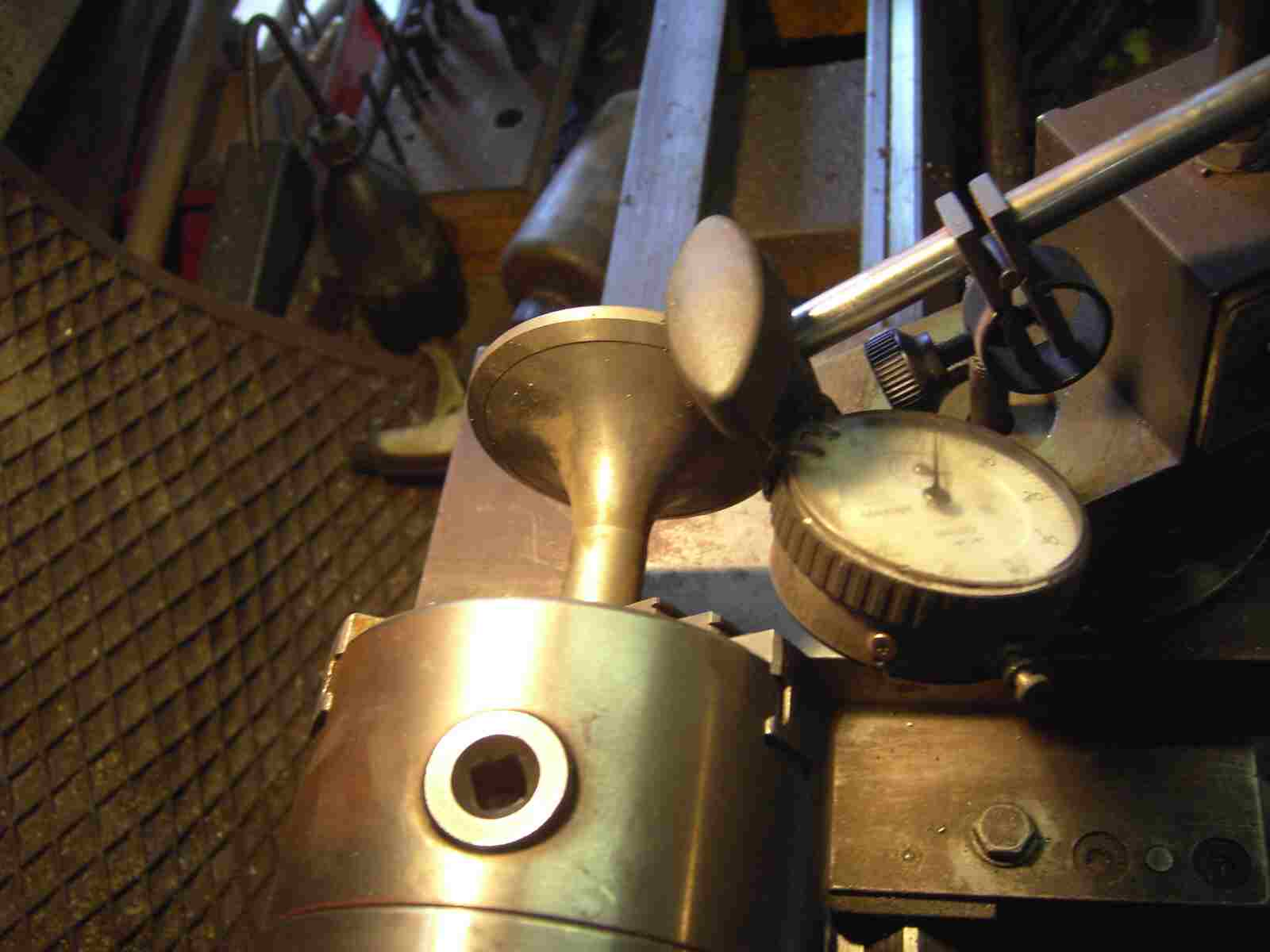 |
|
|
|
Ich versuche, auf meiner Drehbank, den Dichtrand etwas nach zu drehen. Dafür benötige ich aber den richtigen Winkel. Da ich noch ein großes Ventil von einem LKW, mit dem gleichen Winkel besitze, kann ich den Einstellwinkel kopieren und zwar mit der Messuhr.
|
|
|
|
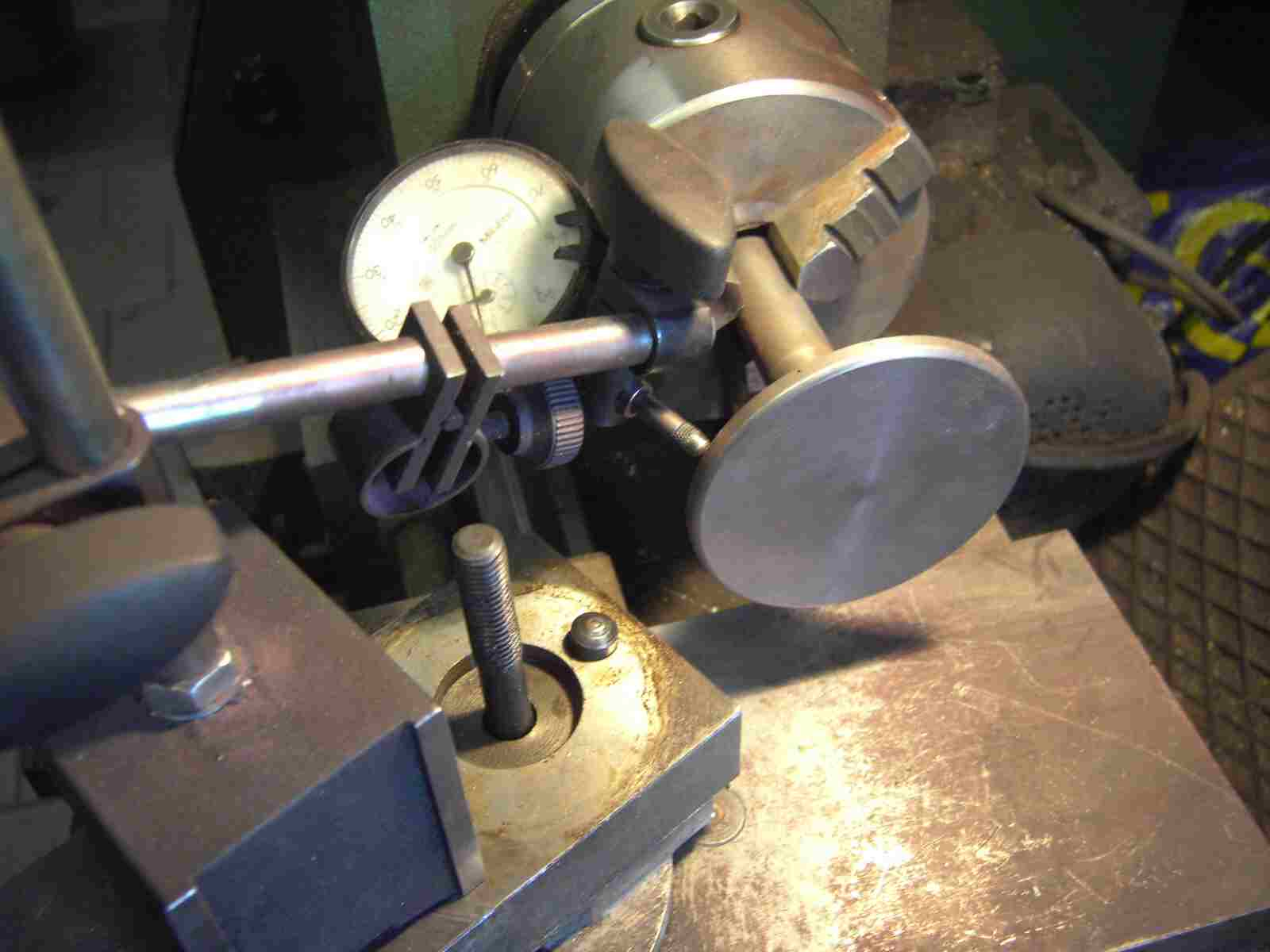 |
|
|
|
Das Ventil wird mit der Messuhr abgefahren und der Oberschlitten, der Drehbank, wird dem Winkel angepaßt, bis die Messuhr Null Abweichung anzeigt!
|
|
|
|
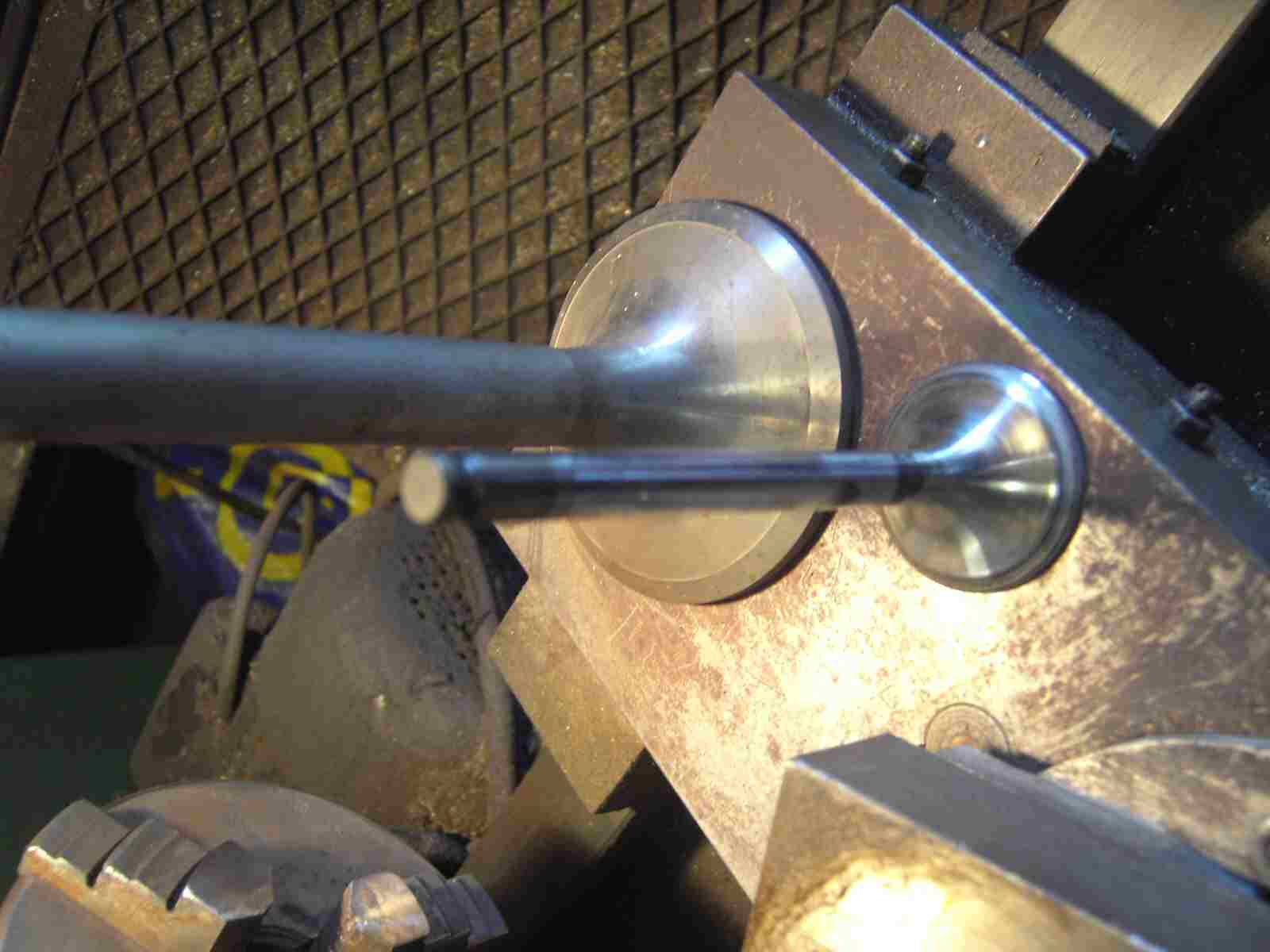 |
|
|
|
Nur mal so als Vergleich! Das LKW Ventil gegenüber dem Auslassventil 36 mm vom Lancia Turbo.
|
|
|
|
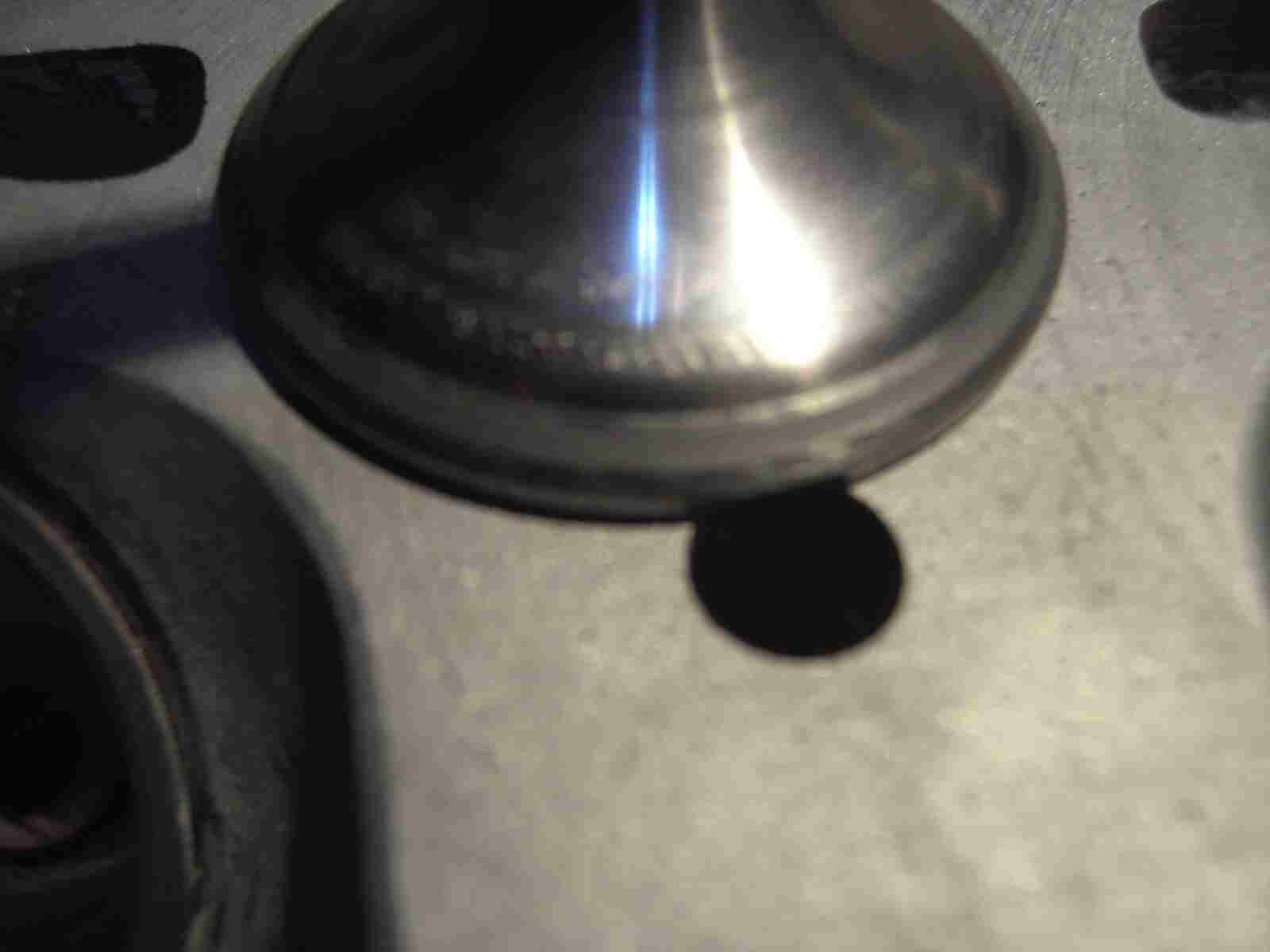 |
|
|
|
Der Dichtungsrand vom Auslassventil wurde nachgedreht und nochmals eingeschliffen!
|
|
|
|
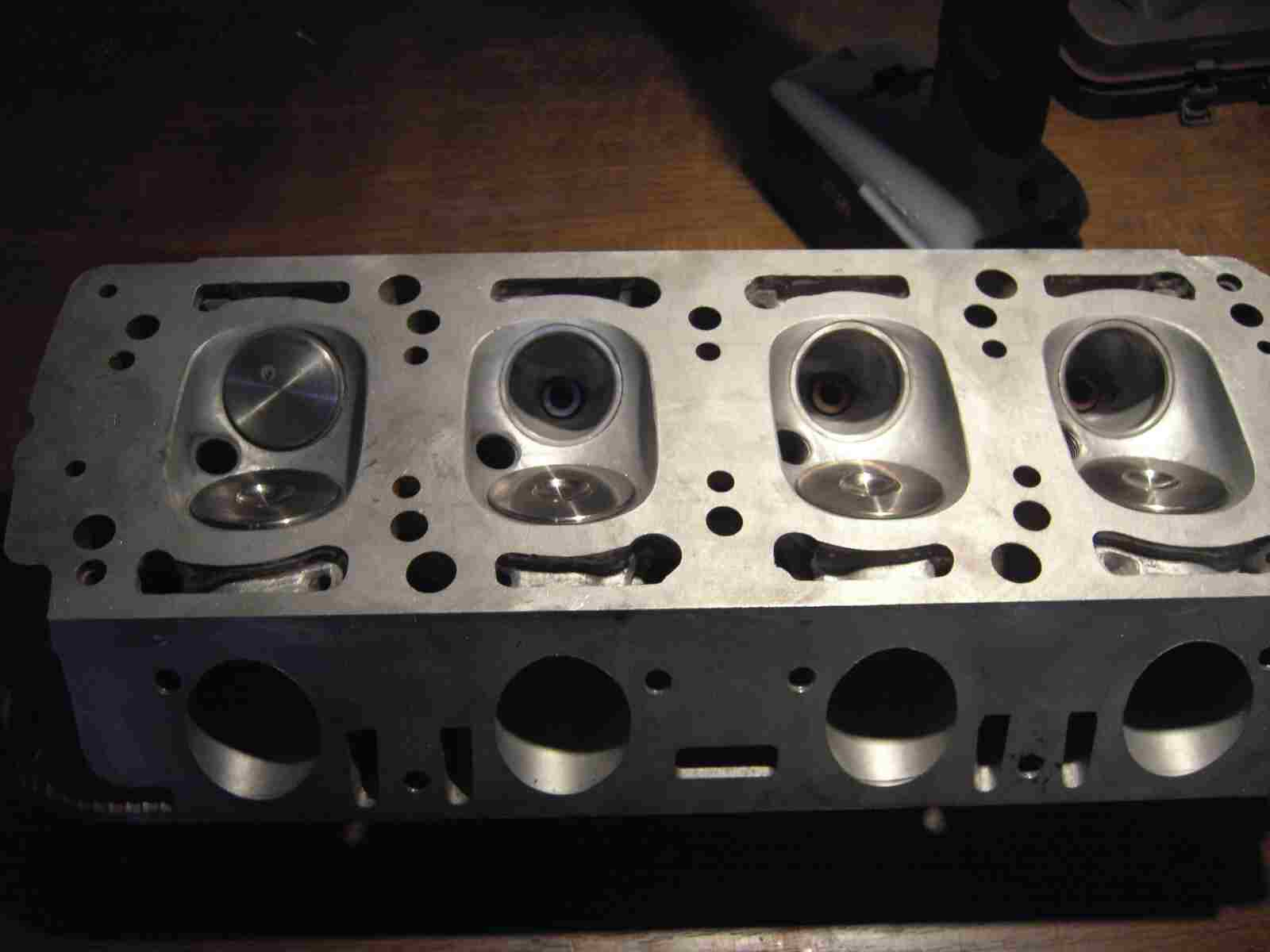 |
|
|
|
Das Ventil mit dem Ventiltrieb wird wieder eingebaut!
|
|
|
|
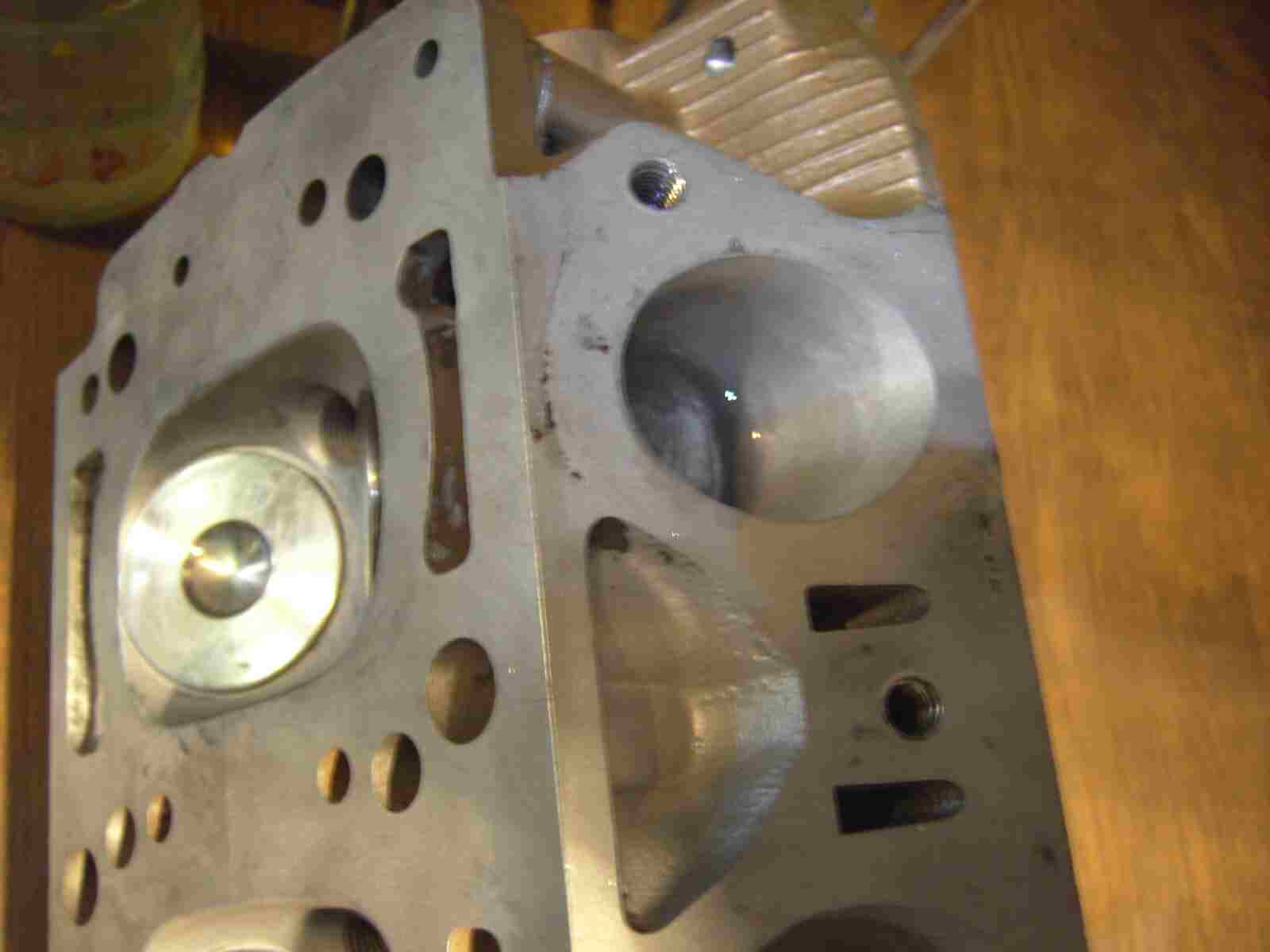 |
|
|
|
Und auf Dichtheit überprüft!
|
|
|
|
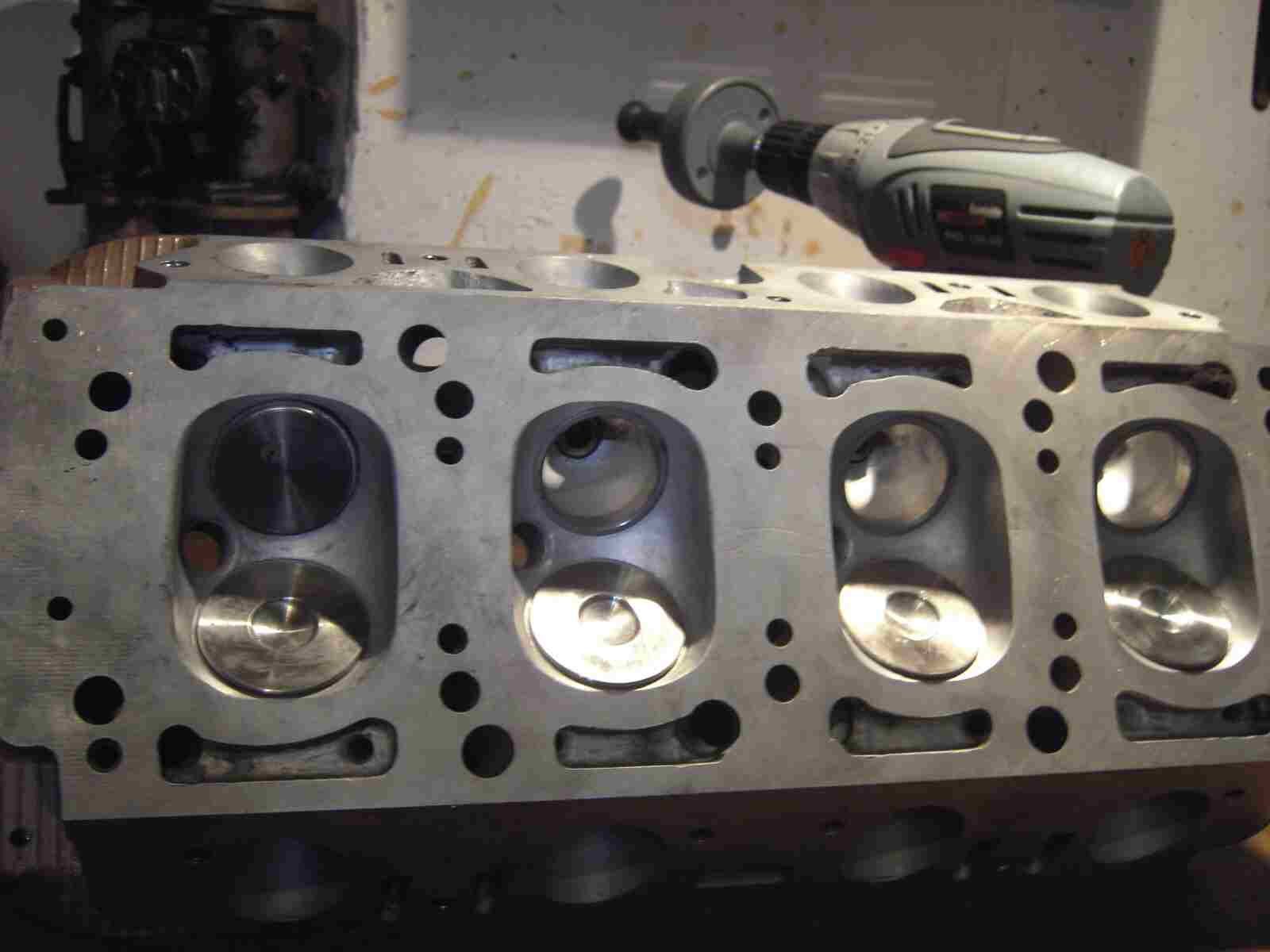 |
|
|
|
Ist es dicht?
|
|
|
|
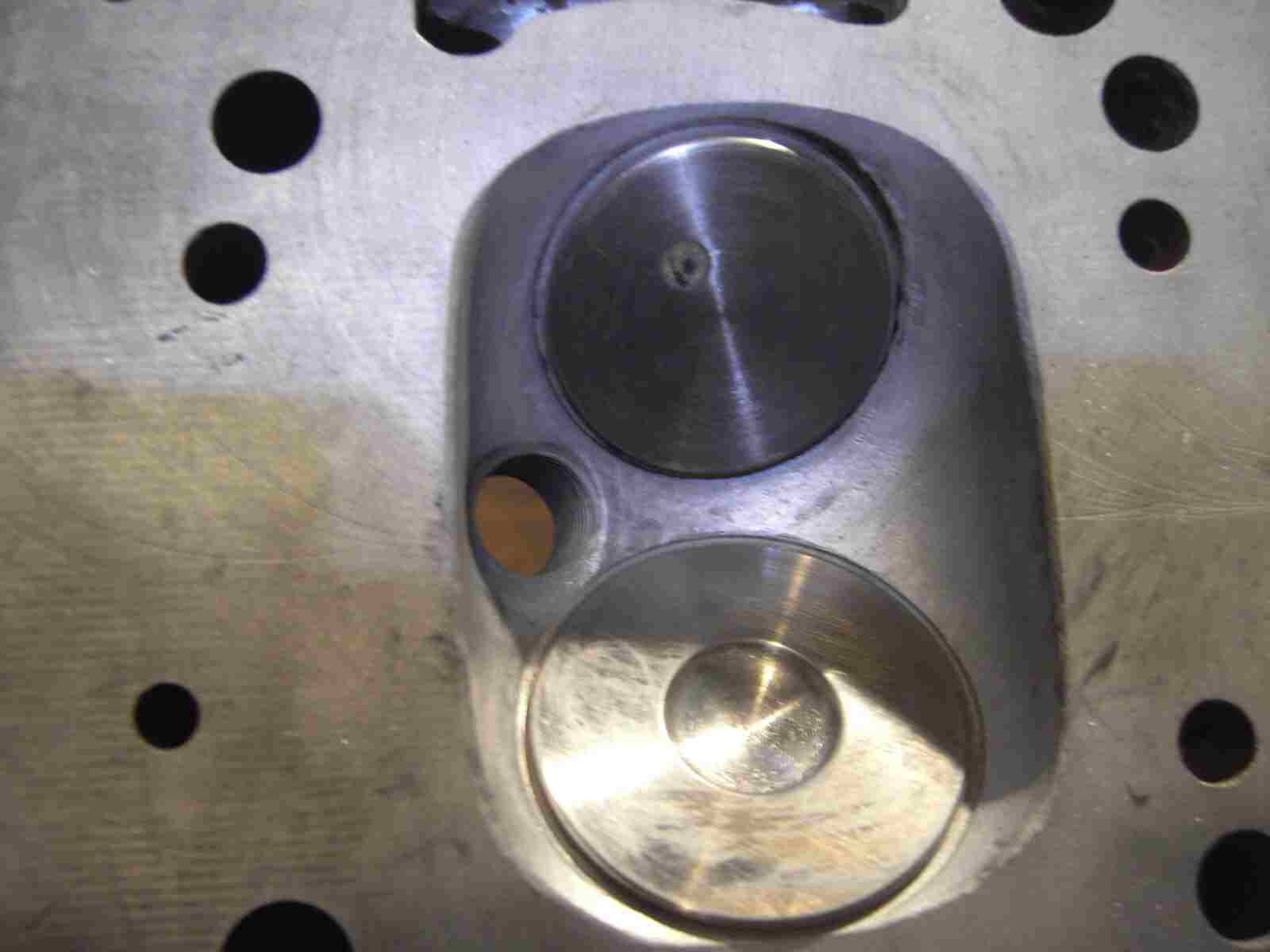 |
|
|
|
Es ist dicht! Das Nachdrehen hat funktioniert!
|
|
|
|
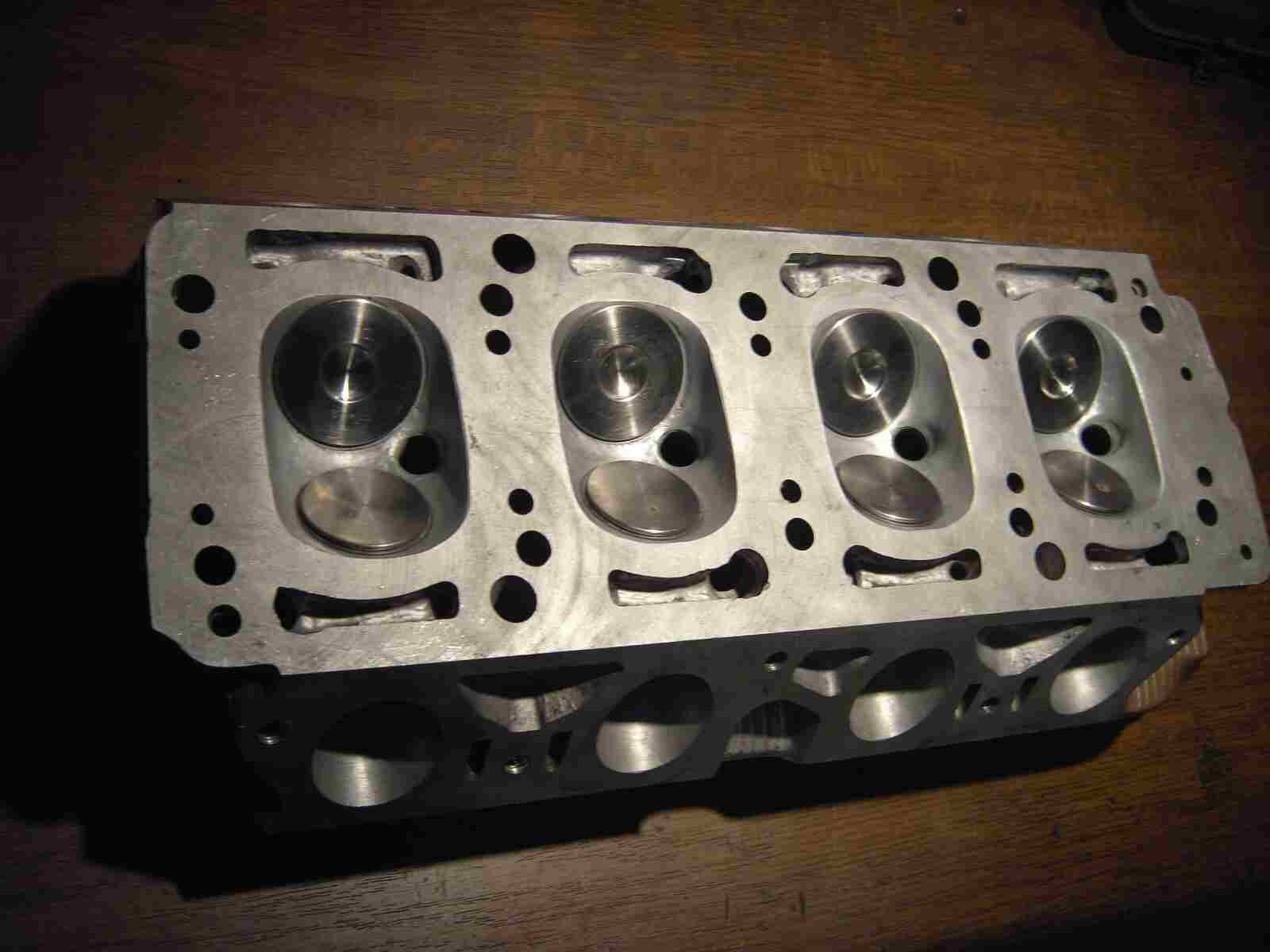 |
|
|
|
Die Ventile sind dicht und der Zylinderkopf ist einbaubereit. Bis zu diesem Punkt war es ein langer Weg. Also, mal schnell Ventile nachmittags einschleifen, das könnt Ihr Euch aus dem Kopf schlagen. Last Euch Zeit und macht es richtig! Nur so hat der Motor seine volle Leistung, alles andere ist Murks!
|
|
|
|
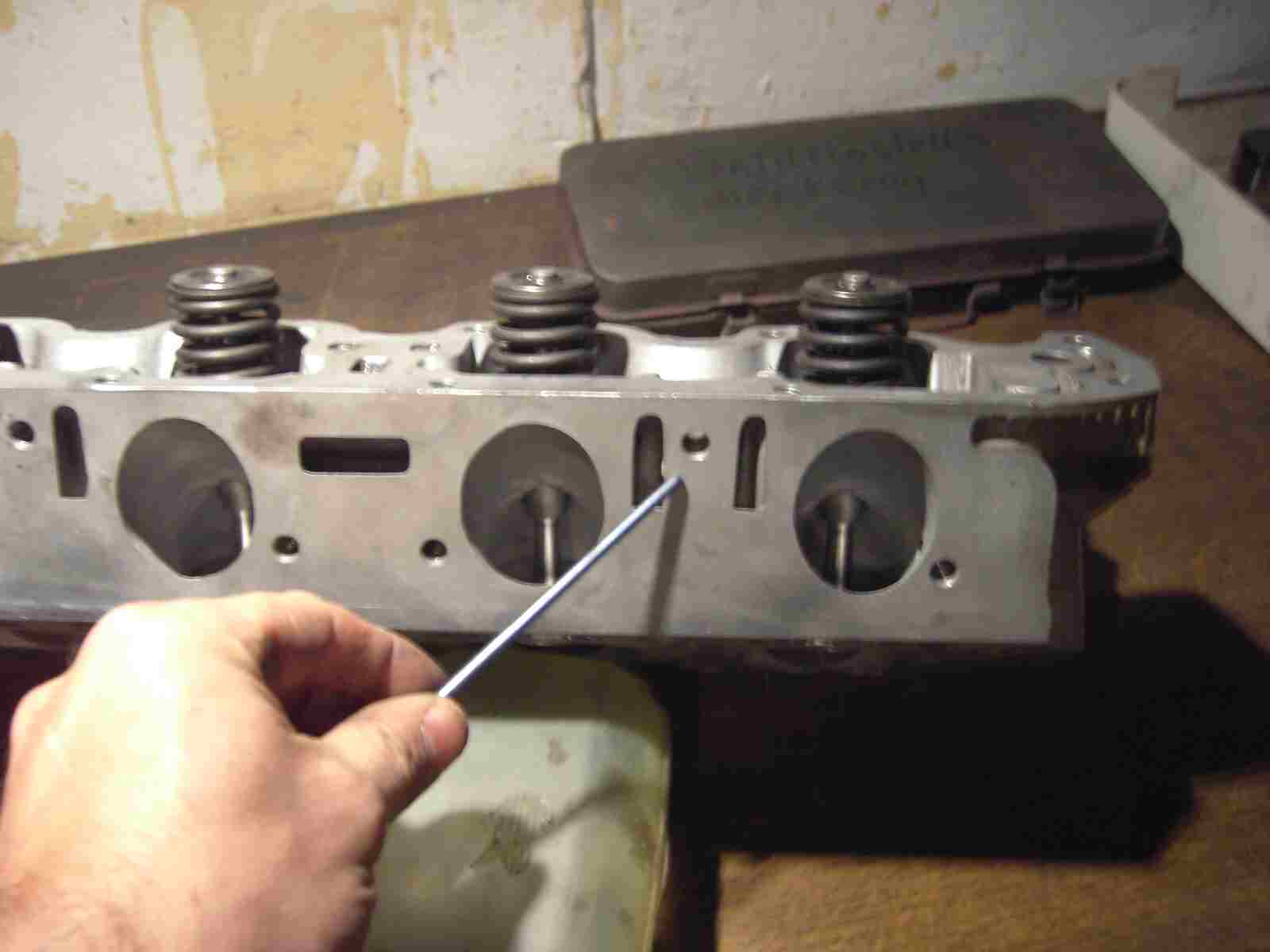 |
|
|
|
Jetzt noch eine kleine Information zum Zylinderkopf! In der Einlass- und Auslassseite befindet sich zwei obere Gewindelöcher!
|
|
|
|
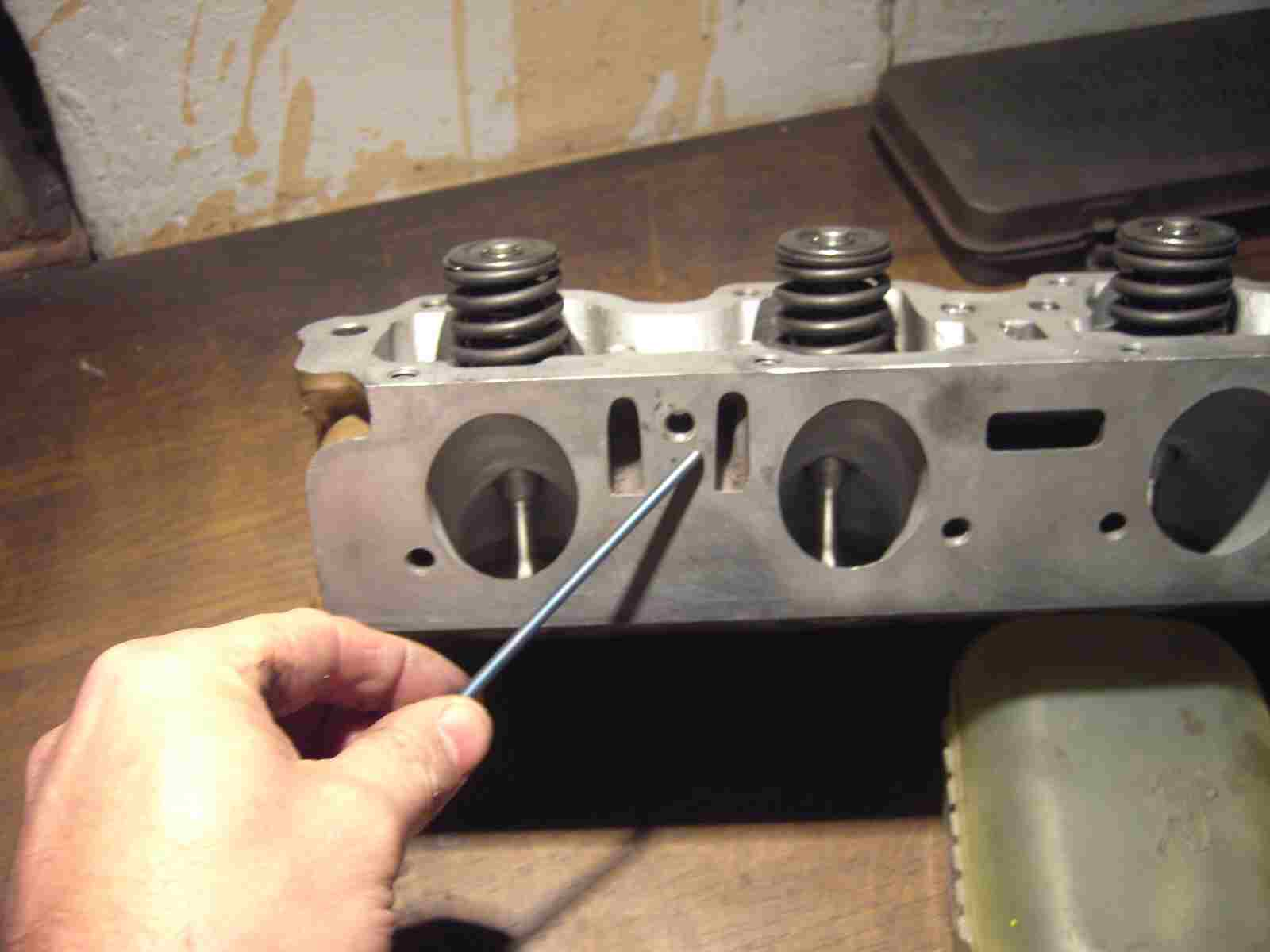 |
|
|
|
Diese sind ganz durchgebohrt und ragen in den Ölraum des Nockenwellengehäuses!
|
|
|
|
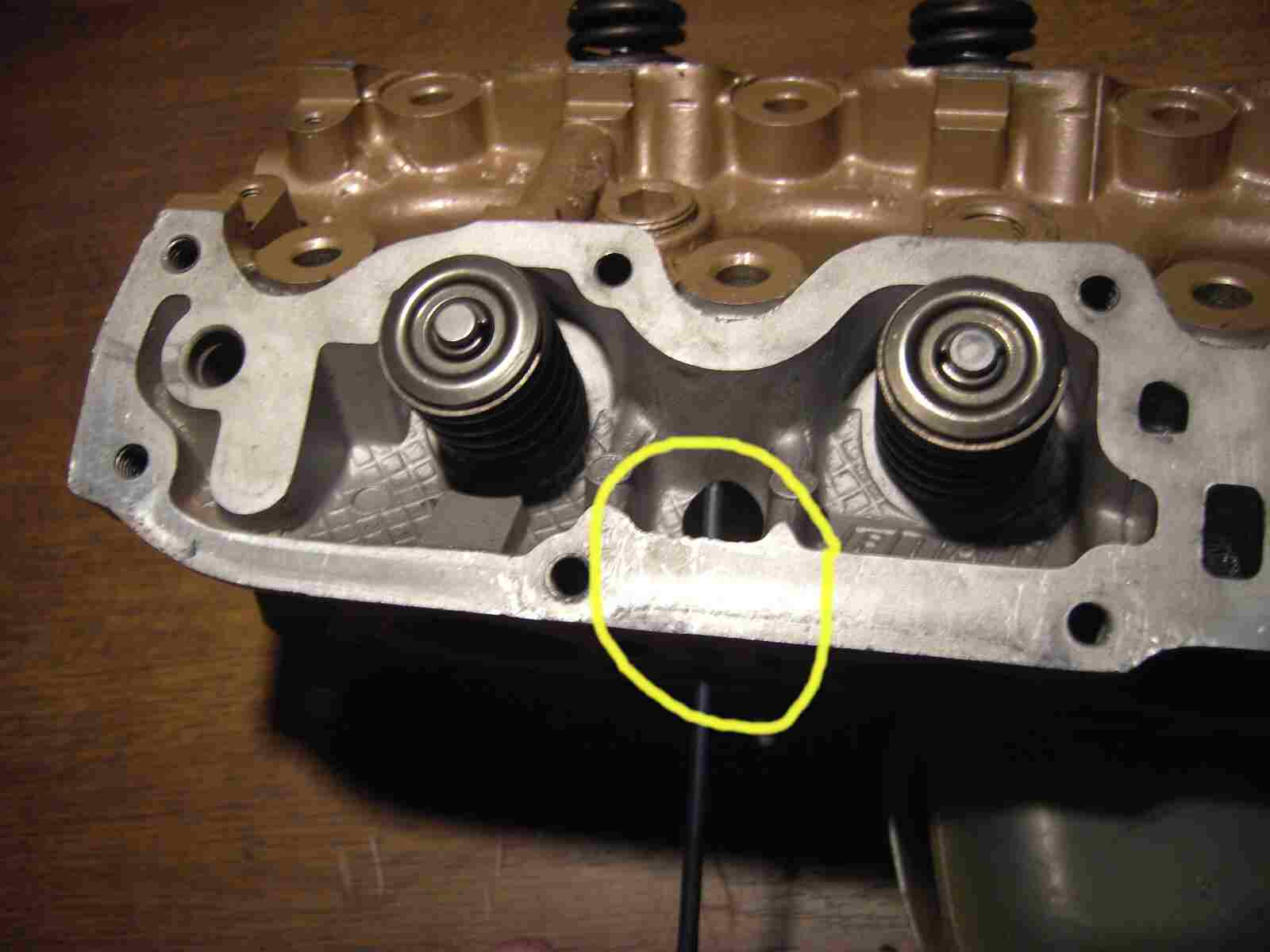 |
|
|
|
Wenn der Stehbolzen eingeschraubt wird, sollte auf das Gewinde etwas Dichtungsmittel aufgetragen werden. Dadurch ist das Gewindeloch dicht und es fließt beim warmen Motor kein Motoröl aus dem Gewinde und dann auf dem Auspuffkrümmer.
|
|
|
|
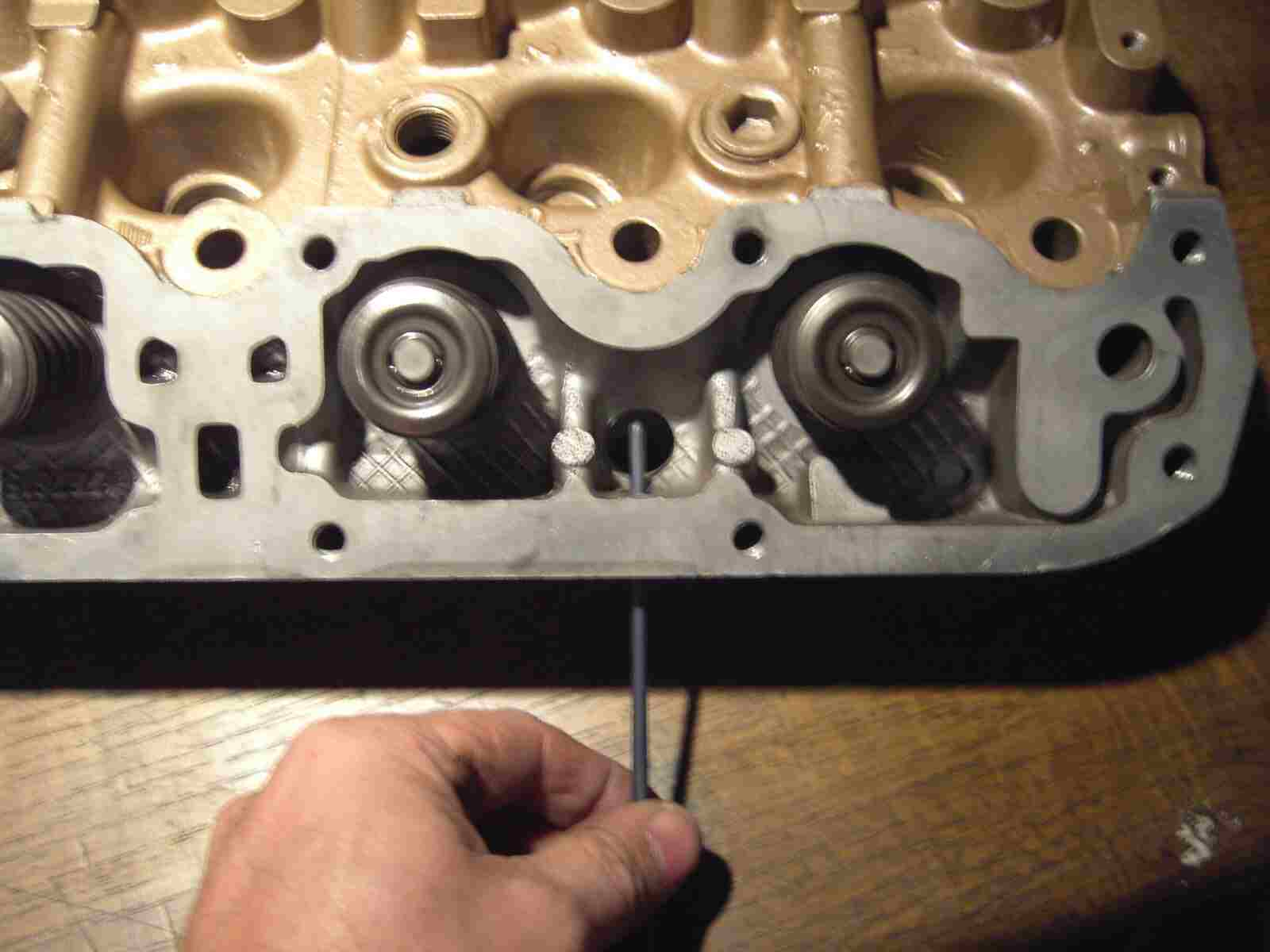 |
|
|
|
Also denkt auch hier daran, ansonsten leidet Euer Motor eventuell an Inkontinenz oder schlimmer sogar an Motorbrand!
|
|